Владимир АРУТЮНОВ
Член НАН Республики Армения, профессор,
д. х. н., главный научный сотрудник,
Федеральный исследовательский центр химической физики им. Н.Н. Семенова РАН, Институт проблем химической физики РАН
e-mail: v_arutyunov@mail.ru
Введение
Обильные ресурсы природного газа, включая его нетрадиционные разновидности, такие как сланцевый газ и газовые гидраты, позволяют рассматривать их как долговременную базу мировой энергетики. Существенным сырьевым ресурсом энергетики остается попутный нефтяной газ (ПНГ), мировой объем факельного сжигания которого, несмотря на все предпринимаемые усилия и законодательные меры, не снижается уже многие годы, оставаясь на уровне 140 млрд кубометров. Определенную роль в локальной энергетике может играть и биогаз, получаемый при переработке различных сельскохозяйственных и бытовых отходов. Но горючие газы не всегда являются удобным энергоносителем, особенно для транспорта и удаленных потребителей. Несмотря на постоянный рост потребления компримированного природного газа (КПГ) в транспортном секторе и расширение малотоннажного производства и распределенного потребления сжиженного природного газа (СПГ), они не могут полностью взять на себя ту роль универсального энергоносителя, которую играют в настоящее время нефть и жидкие продукты ее переработки. Поэтому проблема конверсии углеводородных газов различного состава и происхождения в более удобное жидкое топливо, а также более привлекательные с экологической точки зрения газообразные энергоносители, прежде всего водород, становится все более актуальной.
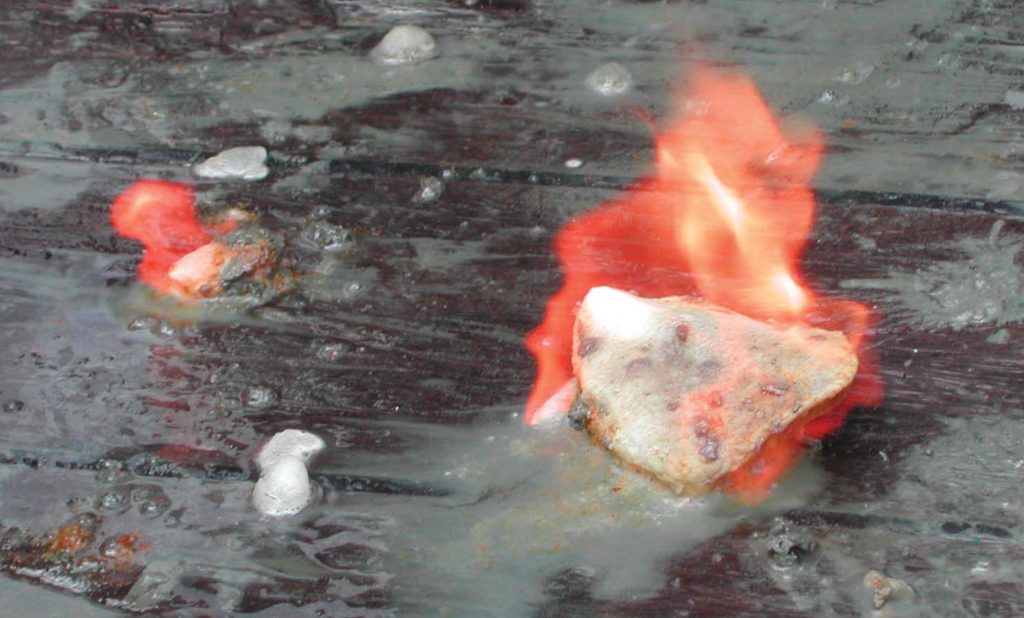
Источник: esys.org
Методы конверсии природного газа в жидкие углеводороды и более привлекательные виды газомоторного топлива хорошо известны, однако существующие технологии пока малопривлекательны для практического применения, особенно в отечественных условиях и для малотоннажных производств [1, 2]. Причина в том, что конверсия метана, основного компонента природных и попутных газов, в другие химические продукты – крайне сложный и энергозатратный процесс. При нормальных условиях метан – наиболее стабильный углеводород, обладающий очень прочными химическими связями, разрыв которых требует больших затрат энергии. Это основная причина серьезного различия традиционных нефтехимических процессов, в которых преобладают разрыв и изомеризация относительно слабых С–С и С-Н связей в жидких углеводородах, и газохимии, начальным процессом в которой является разрыв очень прочной С-Н связи в молекуле метана. Химическая переработка всех остальных углеводородов, начиная уже с этана, требует значительно меньших усилий, и может быть отнесена к хорошо освоенным традиционным нефтехимическим процессам.
Сложность реализации первой стадии активации метана заставляет прибегать к обходным путям его конверсии, наиболее эффективным из которых оказалась его предварительная конверсия в синтез-газ – смесь молекул Н2 и СО, для которой давно разработаны эффективные каталитические процессы превращения в метанол, синтетические жидкие углеводороды (СЖУ, синтетическая нефть) и другие продукты. Главное преимущество такого пути в том, что при определенных условиях метан может быть практически полностью превращен в синтез-газ, но это требует высоких (~900оС) температур, а следовательно, значительных энергозатрат.
Традиционные процессы на основе синтез-газа
Практически все современные промышленные технологии превращения природного газа в химические продукты, за исключением процессов галоидирования и сульфидирования, основаны на его предварительной конверсии в синтез-газ. Затем уже из синтез-газа получают такие крупнотоннажные химические продукты, как аммиак, водород, метанол и синтетические жидкие углеводороды, которые сейчас рассматриваются как потенциальные альтернативные энергоносители. Конверсия природного газа в синтез-газ – наиболее сложная и затратная стадия современных газохимических процессов, на которую приходится до 60–70 % всех затрат на получение целевых продуктов. Высокие затраты на эту стадию являются основным фактором, сдерживающим развитие современной газохимии.
Наиболее распространенным промышленным процессом, на основе которого сейчас производится более 80 % синтез-газа, является паровая конверсия метана.
СН4 + Н2О <−> СО + 3Н2
∆Н = +226 кДж/моль
Этот сильно эндотермический процесс, в котором получают богатый водородом синтез-газ с отношением Н2/СО = 3, начал широко внедряться в промышленных масштабах с 1960‑х гг., когда в качестве исходного сырья вместо угля стали использовать природный газ. Паровая конверсия обычно проводится с использованием относительно недорогих никелевых катализаторов при температурах 800–1000оС, давлениях выше 2 МПа и высоком отношении Н2О/СН4 = 2,5–3,0 и более для снижения зауглероживания катализатора. Процесс проводят в трубчатых печах с внешним обогревом реакционных труб, заполненных нанесенным металлическим катализатором (рис. 1).
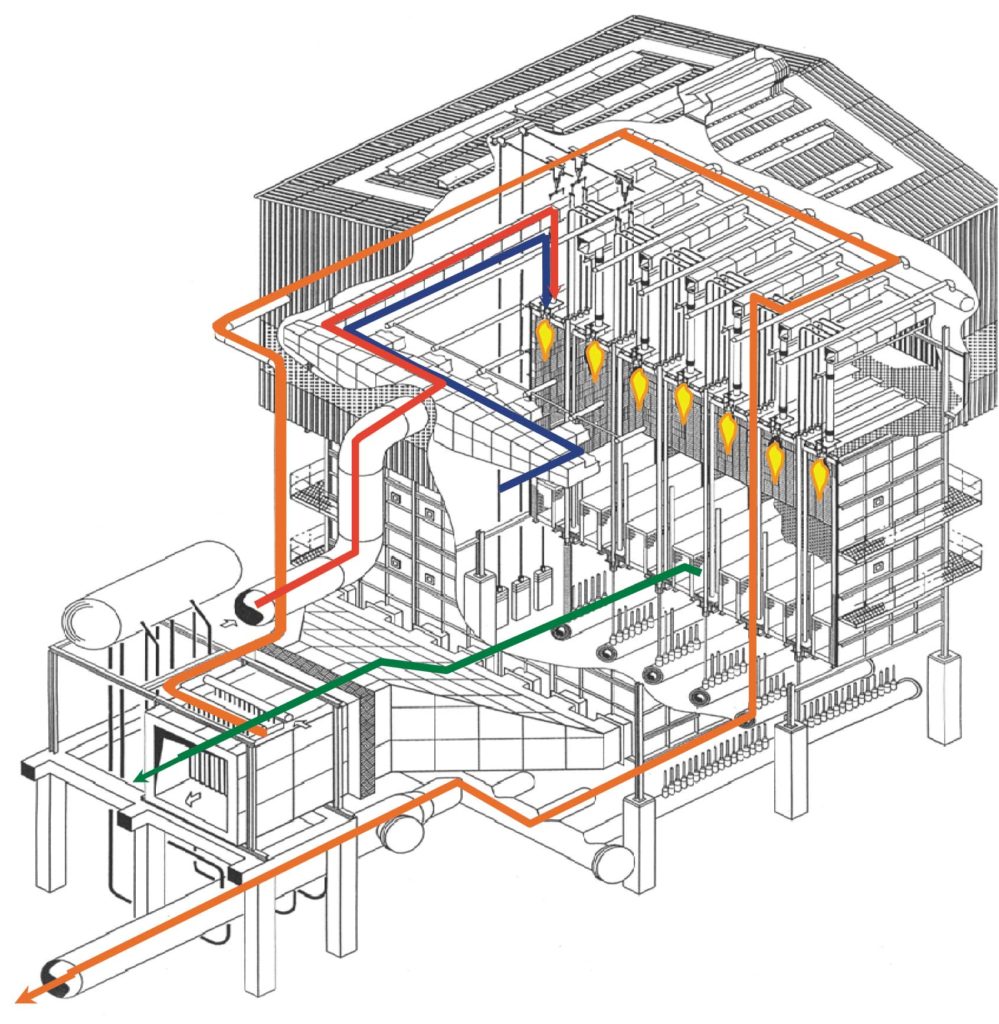
Ведущими компаниями-разработчиками процесса паровой конверсии являются Howe-Baker (США), Haldor Topsoe (Дания), Foster Wheeler Corp. (США), Technip (Франция), Lurgi (Германия) и ряд других, конструкции реакторных печей (риформеров) которых различаются в основном схемами нагрева реакторных труб с катализатором. Тепло отходящих дымовых газов используется для производства пара, а также для предварительного подогрева сырья и воздуха, подаваемого на горелки. Если в составе сырья много тяжелых гомологов метана, приводящих к ускоренному зауглероживанию катализатора, то в схему процесса включают реактор предварительного риформинга, в котором при температуре до 600оС проводят паровую конверсию тяжелых гомологов метана в метан и частично в синтез-газ.
Перспективным направлением в технологии паровой конверсии природного газа, особенно с точки зрения снижения эмиссии основного парникового газа СО2, является использование в качестве источника тепла высокотемпературных гелиевых атомных реакторов (ВТГР) – нового типа универсальных атомных источников энергии, способных вырабатывать тепло с температурой до 1000 °C. С участием концерна «Росэнергоатом» разработан проект установки с модульным реактором МГР-Т из серии ВТГР для производства водорода и электричества (тепловая мощность блока – 600 МВт). Реактор испытан в технологии комбинированной выработки высокопотенциального тепла с температурой теплоносителя на выходе из реактора 950–1000оС и электроэнергии с эффективностью газотурбинного цикла преобразования энергии 48 %. Высокопотенциальное тепло, получаемое в реакторе, отводится теплоносителем первого контура (гелием), имеющим на выходе из реактора температуру 950оС. Это тепло передается конвертируемой парогазовой смеси в химико-технологической части установки в высокотемпературных теплообменниках. Оставшаяся тепловая энергия в блоке преобразования энергии преобразуется в электрическую энергию в прямом газотурбинном цикле. Из общей тепловой мощности реактора, составляющей 600 МВт, 160 МВт идет на процесс паровой конверсии метана и 435 МВт – на производство электроэнергии. Расчетный срок службы реактора составляет 60 лет.
Другая промышленная технология конверсии природного газа в синтез-газ – парциальное окисление (окислительная конверсия) – была разработана в начале 1950‑х гг. Это слабо экзотермический процесс, не требующий дополнительного подвода тепла.
СН4 + 0,5О2 <−> СО + 2Н2
∆Н = -44 кДж/моль
Как правило, процесс осуществляют при давлении 30–100 атм в небольшом избытке чистого кислорода по сравнению со стехиометрией реакции, чтобы обеспечить более полную конверсию и достижение необходимой для реакции температуры, что приводит к образованию некоторого количества продуктов глубокого окисления СО2 и Н2О. Окислительная конверсия метана может протекать как в присутствии катализатора, так и без него. Для некаталитического процесса необходимы температуры 1200–15000С и давления 2,5–8 МПа, при которых достигается полная конверсия углеводородов и предотвращается сажеобразование. Термическая эффективность процесса достигает 60–75 %. В каталитическом процессе обычно используют никелевый или родиевый катализатор, чаще всего на цеолитах ZSM‑5. При этом возможны более мягкие условия (800–9000С, 2,5–3,5 МПа), что позволяет использовать технологию в малотоннажных процессах, а также повышает ее мобильность.
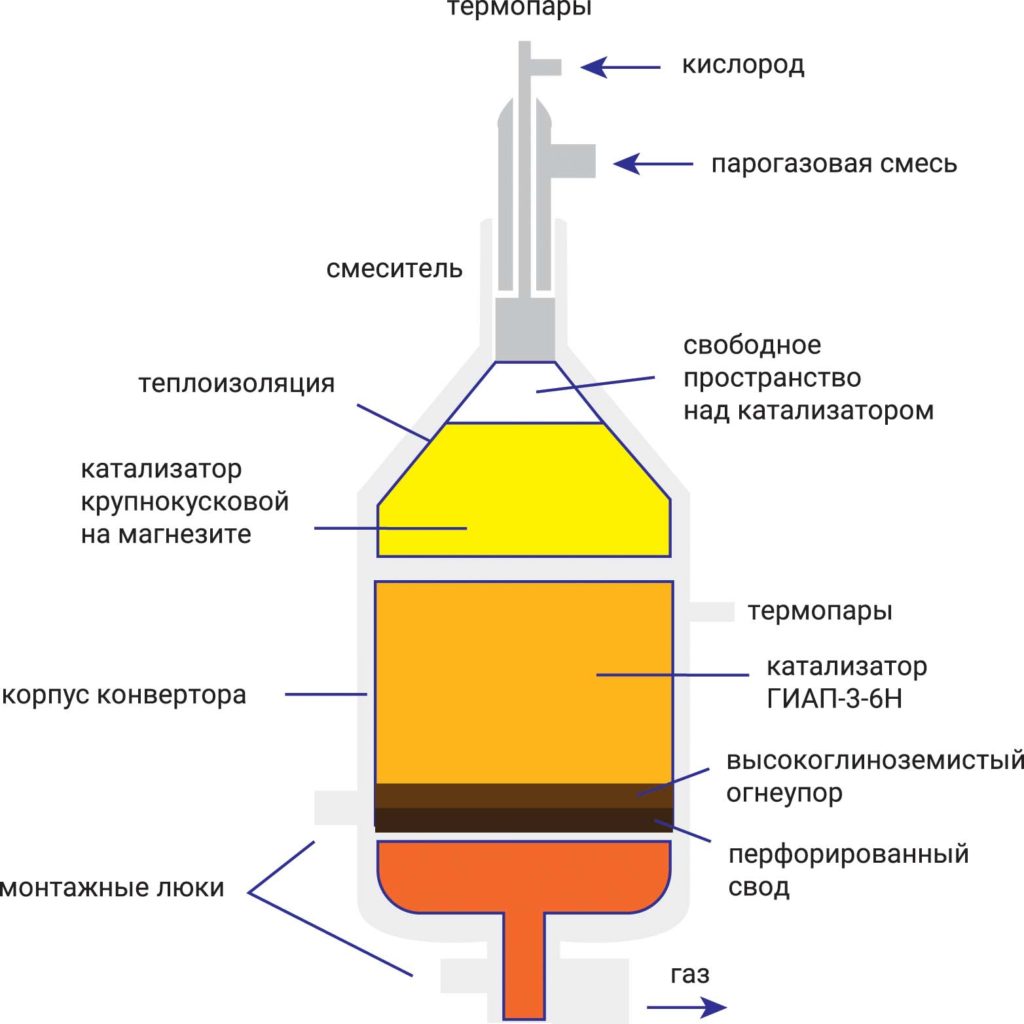
1 – монтажные люки; 2 – корпус конвертора; 3 – теплоизоляция; 4 – смеситель;
5 – термопары; 6 – свободное пространство над катализатором; 7 – катализатор крупнокусковой на магнезите; 8 – катализатор ГИАП‑3–6Н; 9 – высокоглиноземистый огнеупор; 10 – перфорированный свод.
На практике часто используют комбинированную парокислородную конверсию метана. Помимо снижения энергозатрат, это позволяет получать синтез-газ с соотношением Н2/СО2 »2, наиболее благоприятным для синтеза метанола и продуктов Фишера-Тропша. Такой процесс успешно реализован на крупнейшем в мире предприятии по производству синтетических жидких углеводородов Perl GTL компании Shell в Катаре. Главными недостатками технологии парциального окисления природного газа являются большие капиталовложения в установки по разделению воздуха, а также заметное образование сажи, которую необходимо удалять. Существуют также проблемы взрывобезопасности процесса. Помимо высоких температур и давлений для достижения высокого выхода синтез-газа необходимо обеспечивать низкое соотношение О2/СН4 = 0,6–0,7, то есть работать с очень богатыми смесями, соотношение метана и кислорода в которых фактически лежит вне области воспламенения для нормальных условий, что крайне сложно. Коммерциализацию процесса парциального окисления метана затрудняют также большие размеры реакторов. Ведущими разработчиками и лицензиарами технологии парциального окисления метана являются компании Shell и Chevron Texaco.
Популярной промышленной технологией конверсии природного газа становится автотермический риформинг (АТР) – комбинация экзотермической реакции гомогенного парциального окисления и эндотермической реакции парового риформинга, энергию для осуществления которой получают за счет парциального и полного окисления части углеводородного сырья в том же реакторе. Пионером и наиболее активным разработчиком этого процесса с 1960‑х гг. является датская компания Haldor Topsoe [3].
Основные показатели различных промышленных методов получения синтез-газа представлены в табл. 1 и на рис. 3.
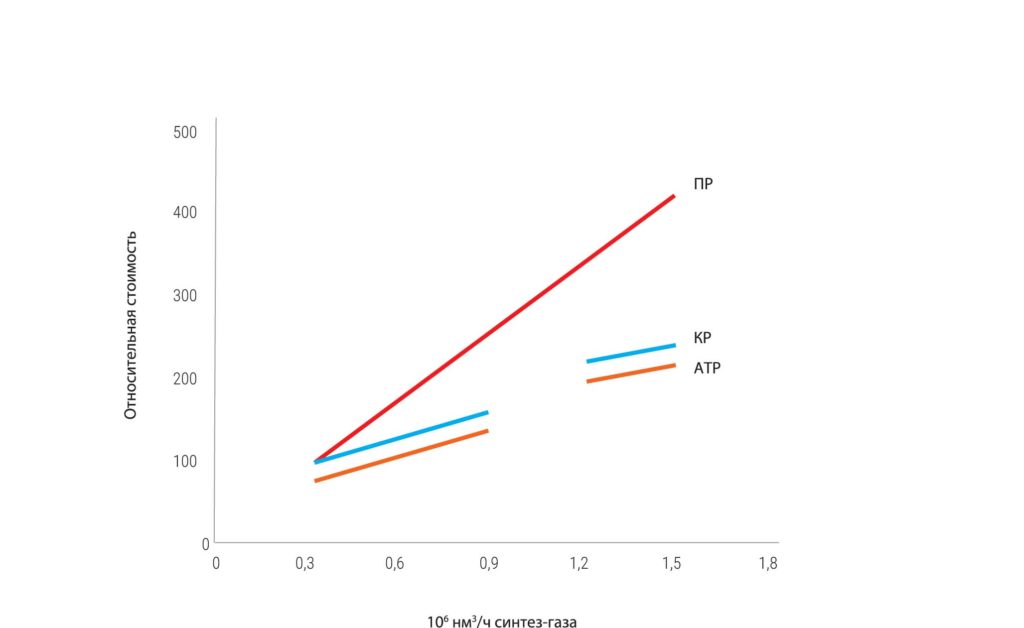
ПР – паровой риформинг; КР – комбинированный риформинг; АТР – автотермический риформинг [4]
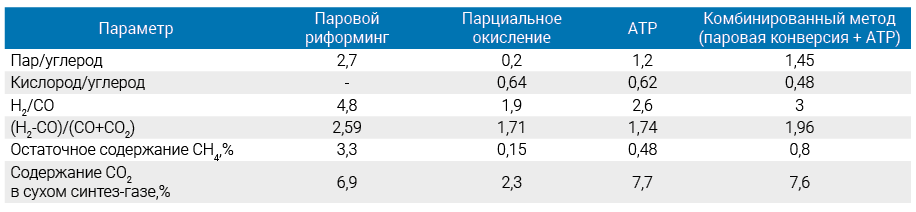
При небольшой производительности установок (до 300 тыс. м3/ч) их относительная стоимость для всех процессов примерно одинакова. С увеличением мощности стоимость всех процессов растет линейно, но для парового риформинга этот рост заметно круче. Поэтому при мощности в 1,5 млн м3/ч относительная стоимость парового риформинга почти в два раза выше, чем автотермического.
Наиболее крупнотоннажным продуктом (более 180 млн т/год), производимым на основе синтез-газа, является аммиак – основа производства азотных удобрений для современного высокопродуктивного сельского хозяйства. Хотя аммиак уже давно рассматривается как потенциальное транспортное топливо [5], а также источник получения водорода [6], серьезные проблемы, возникающие при его практическом использовании, пока сдерживают развитие данного направления.
Более очевидны перспективы использования для этих целей другого продукта, получаемого из синтез-газа – метанола. В настоящее время метанол – продукт газохимии с наиболее динамично растущим объемом производства. В мире более 90 заводов, производящих метанол, с суммарной установленной мощностью около 110 млн т/год. Его мировое производство превысило 80 млн т/год, а к 2025 г. прогнозируется достижение уровня в 120 млн т/год. Особенно быстрыми темпами производство метанола развивается в Китае, который обеспечивает почти половину его мирового производства. Объем производства метанола в России – 4,4 млн т/год. Метанол – универсальный продукт, который может заменить нефть во многих нефтехимических процессах, и универсальное топливо, которое можно использовать практически во всех типах двигателей внутреннего сгорания (ДВС), а также как топливо для газовых турбин и котельное топливо. Наконец, метанол – наиболее удобный жидкий носитель водорода. Водород для питания двигателей внутреннего сгорания или топливных элементов может быть получен из метанола непосредственно на борту транспортного средства при его относительно мягкой паровой каталитической конверсии.
На промышленном уровне уже давно освоен и процесс превращения синтез-газа в жидкие синтетические углеводороды (синтез Фишера-Тропша), способные заменить природную нефть [3]. Фракционный состав образующихся продуктов зависит главным образом от температуры процесса и природы используемого катализатора, и определяется коэффициентом α, отражающим соотношение констант скоростей роста и обрыва углеводородной цепи на катализаторе. Обычно он весьма широк, от метана до углеводородов C50 и выше (рис. 4).
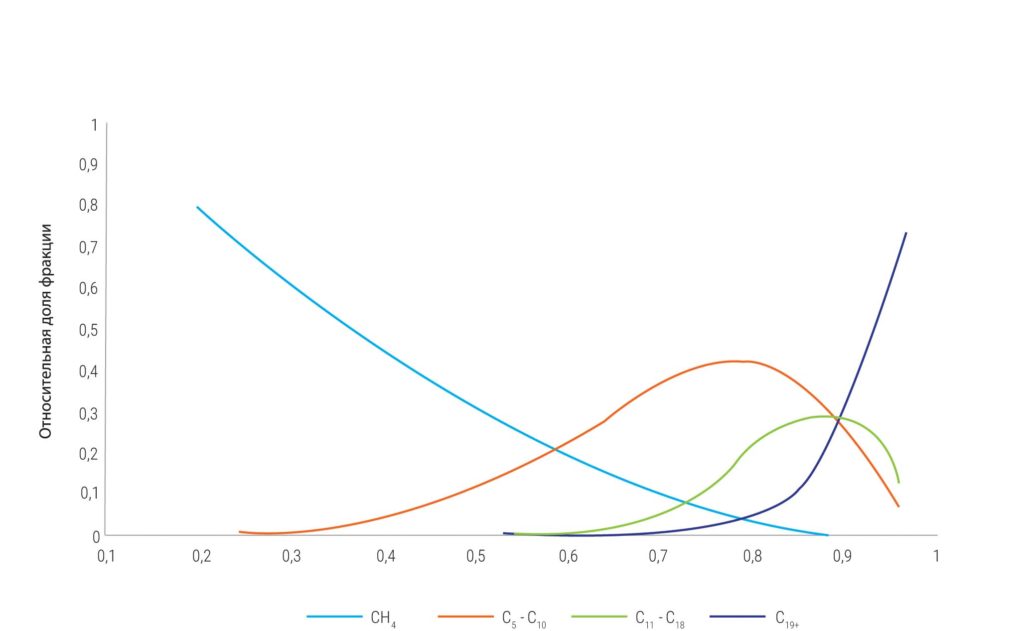
В мире существуют несколько крупных предприятий по производству жидких углеводородов на основе конверсии природного газа в синтез-газ и последующего синтеза Фишера-Тропша, то есть схеме, называемой технологией GTL (Gas to Liquid), суммарной производительностью около 10 млн т/год, а также ряд небольших пилотных установок различных компаний. Основной продукцией GTL предприятий, реализованных на основе технологии компании Shell (Perl GTL в Катаре и Bintulu GTL в Малайзии), является дизельное топливо. Предприятия, реализованные на основе GTL технологии компании Sasol (Oryx GTL в Катаре, Escravos GTL в Нигерии и ряд других) производят более широкий спектр продукции, включающей помимо дизельного топлива бензин, олефины и оксигенаты. В Китае и ЮАР действуют предприятия, производящие синтетические жидкие углеводороды по аналогичной схеме, но использующие в качестве сырья для получения синтез-газа уголь (Coal to Liquid, CTL-технологии).
Основной проблемой современных GTL предприятий является их технологическая сложность и высокие затраты на стадию превращения природного газа в синтез-газ, на которую приходится до 60 % всех затрат. Удельные капвложения в такие предприятия превышают 200 тыс. долл. за баррель ежедневной продукции, что в несколько раз превышает типовые капвложения в нефтеперерабатывающие предприятия. Поэтому после падения цен на нефть привлекательность таких предприятий резко упала (рис. 5), и в настоящее время при цене нефти на уровне 50–60 долл./баррель строительство новых подобных предприятий не планируется. Необходимо отметить, что, согласно оценкам специалистов ВНИИГАЗ, при реализации подобных предприятий в отечественных условиях удельные капзатраты будут примерно в два раза выше, чем для условий Мексиканского или Персидского заливов.
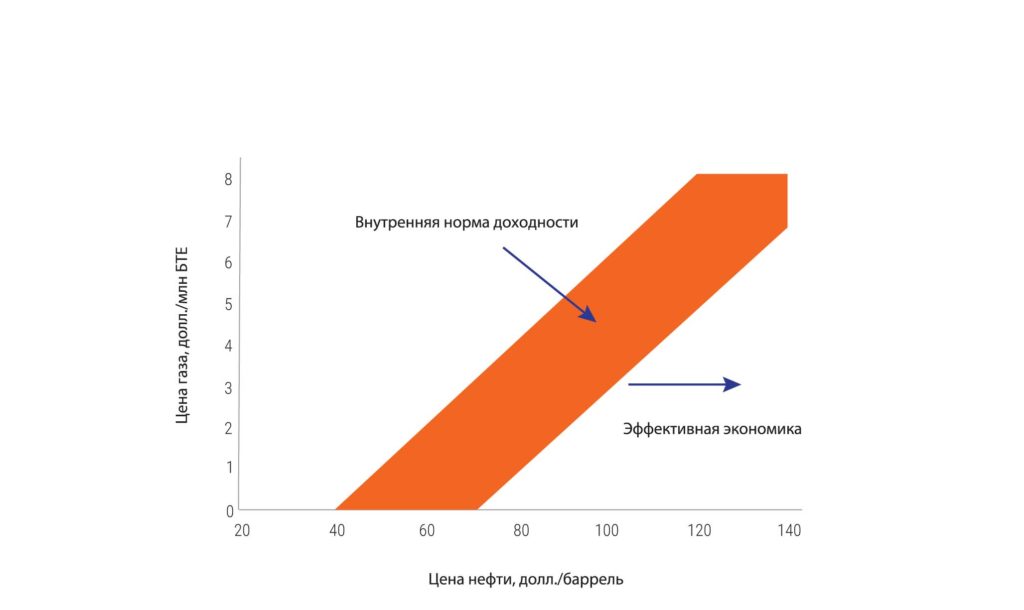
Альтернативные технологии конверсии метана в синтез-газ
Принципиальным недостатком современных сложных технологий GTL является то, что они непригодны для реализации в средне- и малотоннажном варианте, в то время как подавляющая часть перспективных традиционных и особенно нетрадиционных источников углеводородных газов относится именно к этой категории. Поэтому во всем мире ведется разработка альтернативных технологий GTL. Основной упор делается на создание более простых и компактных процессов получения синтез-газа. Уже предложен и испытывается ряд принципиально новых процессов, включая процессы на основе окисления природного газа на керамических мембранах, процессы в микроканальных реакторах, процессы фильтрационного горения, окисление метана при миллисекундных временах контакта, процессы на основе энергетических и электрохимических технологий [3]. Пока ни одна из этих технологий не реализована в промышленном масштабе, но интенсивные работы ведутся во многих странах. Мы лишь коротко отметим недавно разработанный нами метод матричной конверсии, который позволяет проводить процесс в автотермическом режиме без использования внешних источников тепла или энергии, не требует катализаторов и обеспечивает удельную объемную производительность по синтез-газу на порядок выше, чем паровая конверсия. Процесс позволяет использовать углеводородные газы практически любого состава и происхождения, а его рентабельность слабо зависит от объема перерабатываемого газа [8].
Прямые методы конверсии метана в химические продукты
Высокие затраты на получение синтез-газа стимулируют интерес к прямым процессам превращения основного компонента природного газа – метана – в химические продукты и жидкое топливо, не требующим его предварительной конверсии в синтез-газ. Наиболее привлекательным направлением остается окислительная конденсация метана в этилен – процесс, который был открыт в начале 1980‑х и породил большие надежды на создание эффективных химических методов переработки метана. Так как этилен является базовым соединением для производства большого числа продуктов современной нефтегазохимии, такой процесс позволил бы полностью решить проблему химической переработки природного газа. За прошедшее время его исследованию были посвящены тысячи работ, но достигнуть уровня коммерциализации процесса пока так и не удалось [3]. Экономически более выгодным процессом превращения метана в этилен и далее продукты на его основе оказался многостадийный путь с последовательным превращением метана в синтез-газ, затем метанол и далее превращением метанола в этилен на цеолитных катализаторах [3].
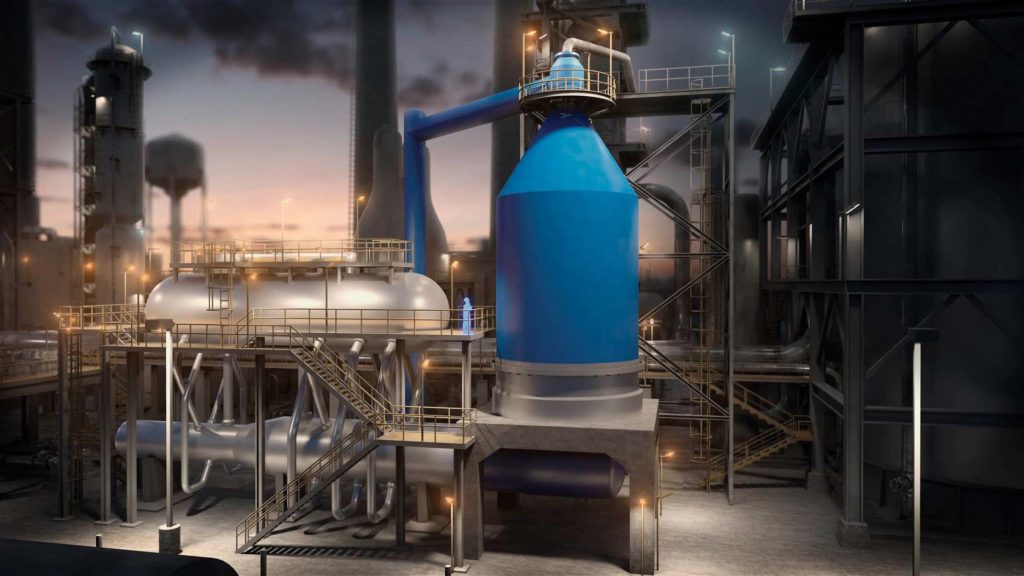
Источник: tecedu.academy
В настоящее время в Китае работает уже несколько таких заводов.
Другим методом прямого превращения метана в химические продукты является его парциальное (частичное) окисление в метанол, образующийся как промежуточный продукт неполного окисления метана при большом недостатке кислорода. Метод был предложен еще в начале прошлого века и применялся как промышленный, но из-за низкой конверсии метана за проход и невысокой селективности образования метанола уступил процессу на основе синтез-газа. Хотя в последнее время удалось значительно повысить его показатели, он остается привлекательным в основном для малотоннажных процессов, для которых определяющую роль играют его простота и низкие капзатраты [3].
Использование ПНГ в энергетике
Главная причина неполного использования ПНГ и продолжающегося во всем мире его факельного сжигания – отсутствие рентабельных малотоннажных технологий переработки углеводородных газов [1, 2], которые позволяли бы перерабатывать ПНГ непосредственно на месте добычи. В настоящее время единственный безубыточный способ утилизации ПНГ удаленных месторождений, особенно в специфических условиях российских нефтедобывающих регионов – выработка электроэнергии и тепла для собственных нужд. До 30 % энергии сжигаемого ПНГ могло бы использоваться для удовлетворения потребности в энергии самих нефтяных промыслов, что позволило бы значительно сократить объем северного завоза жидкого топлива. Однако для этого необходимо предварительно тем или иным способом извлечь или преобразовать значительную часть содержащихся в ПНГ гомологов метана. Даже незначительная примесь более тяжелых алканов с низкими октановыми числами (ОЧ) и метановыми числами (МЧ) и высокой низшей теплотой сгорания Qн делает ПНГ склонным к детонации и не позволяет достигать номинальной мощности газопоршневого двигателя (ГПД), вынуждая работать со снижением нагрузки (дерейтингом) на 20–30 % и более, а также приводит к его быстрому выходу из строя в результате образования смолистых отложений. А существующие методы сепарации тяжелых компонентов из ПНГ требуют сложного оборудования и высоких энергозатрат и не окупаются для энергоустановок малой и средней (до 10–20 МВт) мощности [9].
Для превращения ПНГ в кондиционное газомоторное топливо, удовлетворяющее требованиям производителей газопоршневых электростанций небольшой мощности, нами был разработан метод селективного окислительного крекинга гомологов метана непосредственно в самом ПНГ [9, 10]. Окислительный крекинг позволяет обеспечить 82–85 %-ю конверсию этана и практически полную конверсию всех более тяжелых углеводородов. Суммарная конверсия гомологов метана составляет 92–95 %. Основными продуктами конверсии являются этилен, монооксид углерода, водород и метан. Метод селективного оксикрекинга позволяет на 11–19 пунктов поднять метановое число смеси и на 6–8 МДж/м3 снизить низшую теплоту сгорания, доведя оба эти показателя до значений, рекомендуемых производителями для устойчивой эксплуатации газопоршневых машин, то есть получить из ПНГ топливный газ, удовлетворяющий требованиям, предъявляемым производителями ГПД.
Получение водорода
Принятое в 2015 году Парижское соглашение по климату провозгласило своей целью разработку и реализацию стратегии снижения эмиссии парниковых газов, прежде всего СО2, за счет снижения доли углеводородных источников в мировом энергобалансе. Достигнуть это предполагается в основном за счет перехода на возобновляемые источники энергии, однако их реальный потенциал значительно ниже даже текущих потребностей мировой энергетики [11], и на обозримый период все серьезные прогнозы отводят им долю всего в несколько процентов мирового энергобаланса [12]. Поэтому неудивительно, что в последнее время основным направлением усилий по снижению «углеродного следа» энергетики провозглашен ускоренный переход на водородную энергетику, т. е. более широкое использование водорода в качестве энергоносителя для производства энергии, коммунального сектора и транспорта. Россия активно присоединяется к этим усилиям. Распоряжением Правительства РФ от 12 октября 2020 г. № 2634‑р утвержден План мероприятий (дорожная карта) по развитию водородной энергетики до 2024 года. План направлен на увеличение производства и расширение сферы применения водорода в качестве экологически чистого энергоносителя, а также вхождение страны в число мировых лидеров по его производству и экспорту.
Основным промышленным методом получения водорода остается и в обозримом будущем будет оставаться его выделение из синтез-газа, получаемого паровой конверсией природного газа (~80 % производства Н2) и угля (~20 % производства Н2). На долю возобновляемых источников приходится много меньше 1 % его мирового производства, а стоимость такого водорода минимум в 3 раза выше получаемого паровой конверсией. Поэтому помимо пока еще очень далеких от практически приемлемых решений вопросов хранения, транспортировки и распределения больших объемов водорода, фундаментальная проблема водородной энергетики – снижение затрат на получение водорода, прежде всего, на конверсию углеводородных газов в синтез-газ.
Учитывая нерешенные пока проблемы транспортировки и хранения больших объемов водорода, наиболее разумным подходом, особенно для транспортного сектора, может стать его распределенное малотоннажное производство из сетевого природного газа или легко транспортируемого жидкого углеводородного сырья непосредственно в местах потребления. Основой такого распределенного производства водорода мог бы стать метод матричной конверсии природного газа в синтез-газ [8], на базе которого может быть также организовано распределенное производство метанола, синтетических жидких углеводородов, аммиака и других потенциальных альтернативных энергоносителей и жидких источников получения водорода.
Заключение
Современная газохимия предлагает широкий набор уже освоенных промышленностью и потенциальных технологий превращения углеводородных газов различного состава и происхождения в более удобные или экологически приемлемые жидкие и газообразные энергоносители. Однако экономическая эффективность большинства этих технологий пока недостаточна для конкуренции получаемых из природного газа альтернативных энергоносителей с традиционными видами жидкого нефтяного топлива. Поэтому важнейшей проблемой перехода на такие энергоносители становится развитие технологической базы газохимии.
Работа выполнена в рамках Программы фундаментальных научных исследований государственных академий наук, тема ФИЦ ХФ РАН 0082-2019-0014, номер госрегистрации AAAA-A20-120020590084-9 и тема ИПХФ РАН 0089-2019-0018, номер госрегистрации АААА-А19-119022690098-3.