Денис ХИТРЫХ
Директор Центра исследований
и разработок, MBA, директор
по маркетингу, АО «КАДФЕМ Си-Ай-Эс», к. т. н.
e-mail: denis.khitrykh@cadfem-cis.ru
Введение
Переход к Индустрии 4.0 подразумевает способность компаний интегрировать цифровые и физические технологии для улучшения работы и повышения производительности. Это требует глубоких изменений производственных и бизнес-процессов. Для промышленных предприятий цифровизация подразумевает как интеграцию производственных процессов внутри предприятия, так и интеграцию смежных и зависимых предприятий в цепочки создания стоимости, на всех стадиях жизненного цикла изделия, начиная с разработки и производства, и заканчивая послепродажным обслуживанием и утилизацией.
Внедрение ремонтов по фактическому техническому состоянию может принести выгоду предприятию в размере 30 % от общей стоимости оборудования
Основная цель цифровой трансформации в нефтегазовой и нефтеперерабатывающей сферах заключается в платформизации бизнес-процессов c учетом особенностей этих отраслей. Это предполагает цифровую трансформацию двух основных процессов: производства и организационных бизнес-моделей за счет использования современных технологий.
К сожалению, нефтяная отрасль является достаточно консервативной и наименее подвержена изменениям. Поэтому в настоящее время можно говорить о достаточно низкой активности при внедрении цифровых технологий в этой сфере. Однако именно цифровизация может существенно повысить конкурентоспособность предприятий данной отрасли, в частности нефтеперерабатывающих заводов (НПЗ).
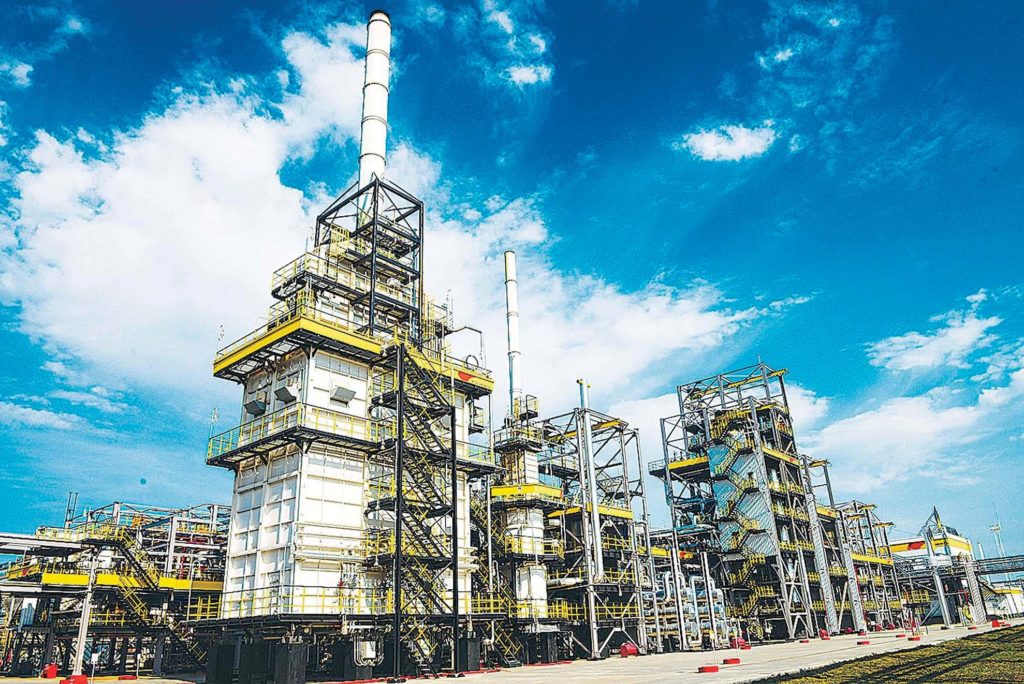
Источник: tonnametr.ru
Одним из стратегических направлений развития всех нефтеперерабатывающих заводов России является повышение надежности, безопасности, энергоэффективности и экологичности эксплуатируемого оборудования. Отечественный и зарубежный опыт эксплуатации НПЗ показывает, что повреждение или выход из строя насосного оборудования завода может повлечь за собой существенный материальный ущерб и даже гибель работников. Для обеспечения безопасной работы оборудования НПЗ необходимо обеспечить высокую вероятность снижения аварийных ситуаций. Кроме того, несмотря на относительно низкую стоимость насосного оборудования, суточный простой одной технологической установки, например, ректификационной колонны из-за ненадежной работы основных и вспомогательных насосов может повлечь за собой миллионные убытки.
Сегодня на каждом НПЗ стран СНГ находится в эксплуатации в среднем до 3000 единиц насосно-компрессорного оборудования мощностью до 1200 кВт, которые потребляют до 80–90 % всего объема электроэнергии. При этом возраст 20–30 % насосов превышает 30 лет и большинство отказов оборудования происходит как раз по причине его неудовлетворительного технического состояния [4].
Поэтому большинство нефтеперерабатывающих компаний страны осознают необходимость и важность внедрения интеллектуальных средств мониторинга технического состояния насосных систем, и переход с системы планово-предупредительных ремонтов на систему ремонтов по фактическому состоянию [1].
По данным работ [2] и [3] внедрение ремонтов по фактическому техническому состоянию может принести выгоду предприятию в размере 30 % от общей стоимости эксплуатируемого оборудования, а цифровой двойник оборудования является ключевым элементом стратегии внедрения ТОиР по фактическому состоянию на нефтеперерабатывающих предприятиях.
В мире существуют примеры удачного внедрения цифровых двойников насосных агрегатов разного уровня. Однако точной оценки эффективности и стоимости внедрения цифровых двойников насосных систем НПЗ в открытой печати до сих пор нет.
Российская нефтеперерабатывающая отрасль на современном этапе развития
Эффективность работы нефтеперерабатывающей отрасли в целом следует за тенденцией основных макроэкономических показателей страны и зависит от изменений потребительского спроса. Действие демпфирующего механизма в условиях резкого падения цен на нефтепродукты в 2020 г. на мировых рынках привели к тому, что внутренний рынок стал для нефтяников премиальным, но в результате, они были вынуждены платить в бюджет обратный акциз на нефть. Таким образом в условиях пандемии были решены две стратегические государственные задачи: наполняемость бюджета и сохранение цен на топливо при резком снижении стоимости нефти. Однако этот же механизм привел к падению рентабельности нефтепереработки.
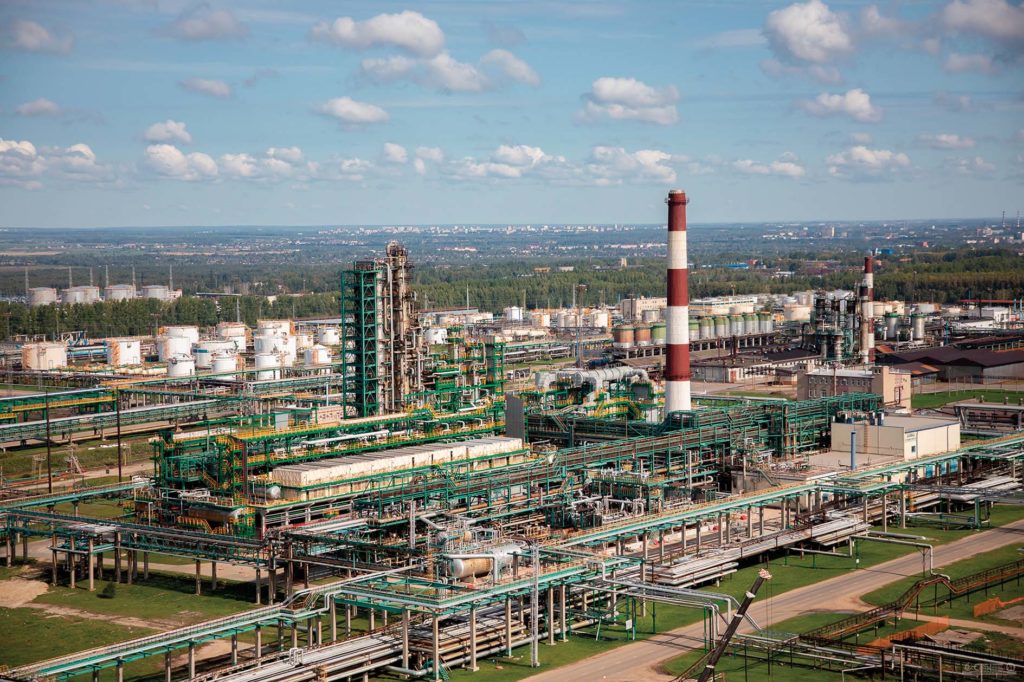
Источник: «Славнефть-ЯНОС»
Данные из открытых источников позволяют оценить техническое состояние нефтеперерабатывающей отрасли в России. Так, согласно информации Минэнерго России (реестр НПЗ) из 38 крупных НПЗ с объемами переработки более 1 млн тонн в год, 24 завода эксплуатируются уже более полувека. Наиболее показательными в данном контексте являются следующие НПЗ:
Туапсинский, который эксплуатируется с 1928 года;
Саратовский, работающий с 1934 года;
Московский, функционирующий с 1938 года.
Средний возраст российских НПЗ – свыше 60 лет. Это говорит об изношенности нефтеперерабатывающих мощностей.
Вместе с тем, крупнейшие нефтеперерабатывающие заводы России продолжили в 2019–2020 гг. реконструкцию и ввод новых технологических мощностей в рамках национальной программы модернизации. Одной из целей этой программы является рост производства высокооктановых бензинов, соответствующих стандартам Евро‑5 и выше. В результате по данным работы [6], средняя глубина переработки нефти на российских НПЗ за последние 5 лет выросла на 17 % и в 2020 году составила 84,4 %.
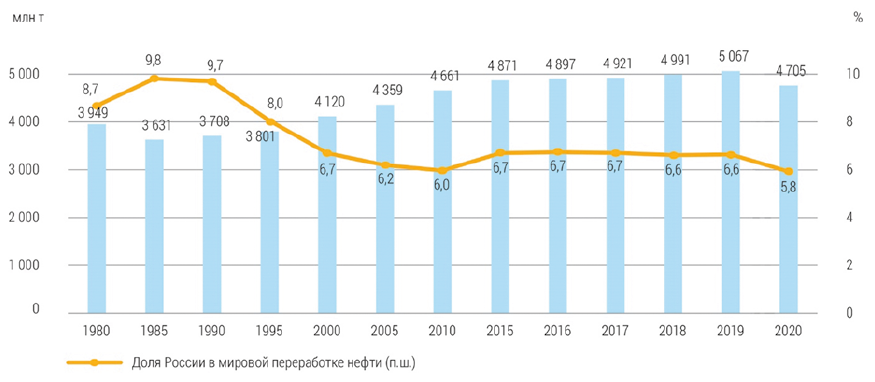
Поставки нефти на переработку в РФ в 2020 году составили 275 млн тонн, что на 5,2 % ниже 2019 года и соответствуют уровню 2013 года.
Сокращение объема первичной переработки нефти в России происходило двумя волнами: в 2015–2017 гг. и 2019–2020 гг. По данным ЦДУ ТЭК, объем нефтепереработки в России в 2020 году сократился на 5,4 % по сравнению с 2019 г. и составил 270 млн тонн.
Все изменения в отрасли за последние 5 лет связаны с законодательными решениями в сфере налогообложения, падением привлекательности экспорта темных нефтепродуктов, давлением на потребление нефти топливной экономичности в транспортном секторе, регулированием внутреннего рынка топлива с сокращением добычи в рамках сделки ОПЕК+ и со снижением рентабельности нефтепереработки вследствие пандемии коронавируса.
Так, налоговый маневр, завершившийся в 2018 году, привел к значительному сокращению производства мазута. В структуре производства основных нефтепродуктов его доля сократилась вдвое; часть независимых и простейших НПЗ прекратили свою деятельность, при этом выросла доля комплексных заводов. За весь период налогового маневра потери НПЗ, не удовлетворяющих критерию поставок на внутренний рынок либо не заключивших модернизационные соглашения, превысили 50 млрд рублей.
В апреле 2020 года участники соглашения ОПЕК+, включая Россию, заключили новую сделку по сокращению добычи нефти после резкого падения спроса на нефть из-за пандемии коронавируса. Согласно [5], параметры нового соглашения ОПЕК+ предусматривают три этапа сокращения добычи нефти:
1 этап: с мая по июнь 2020 г. – сокращение добычи на 9,7 млн б/с по сравнению с базовым уровнем;
2 этап: с июля по декабрь 2020 г. – сокращение добычи на 7,7 млн б/с по сравнению с базовым уровнем;
3 этап: с января 2021 г. по апрель 2022 г. – сокращение добычи на 5,8 млн б/с по сравнению с базовым уровнем.
В качестве базового принят уровень добычи в октябре 2018 года. Для России базовый уровень установлен на 11 млн б/с.
Еще одной из ключевых проблем российской нефтеперерабатывающей отрасли является сильная зависимость от импортных технологий и оборудования. В настоящее время в отрасли отсутствуют жесткие запреты на использование импортного оборудования, что замедляет процесс импортозамещения.
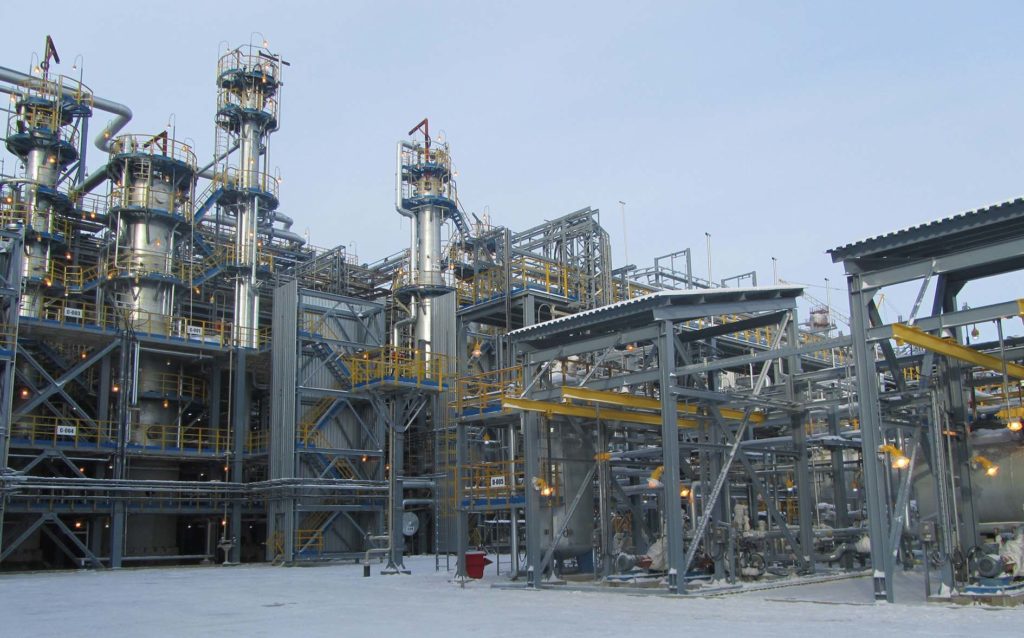
Источник: m.angi.ru
Концепция гибридного цифрового двойника компании Flowserve
В 2016 году компании PTC, Flowserve, National Instruments и Ansys представили инженерному сообществу прототип гибридного цифрового двойника, созданного на основе численных расчетов и использующего суррогатную модель поведения насосного агрегата [7].
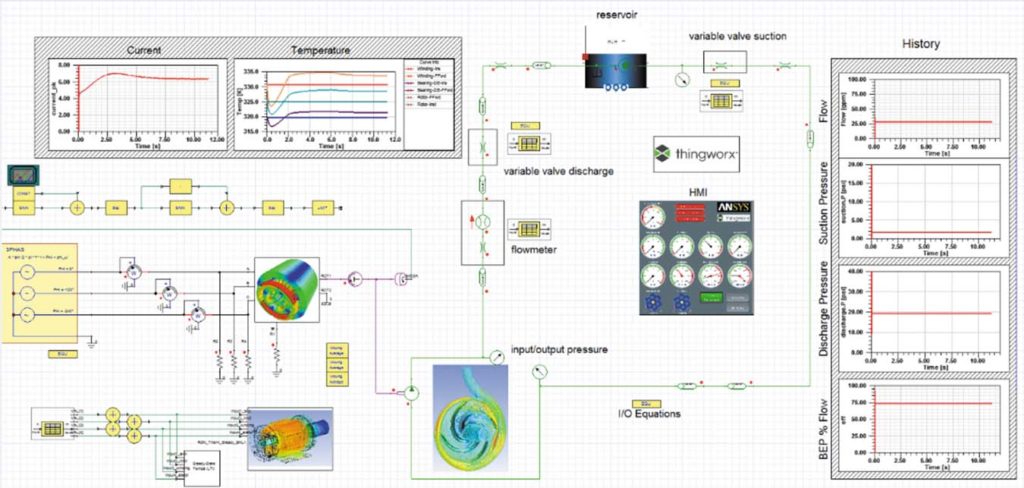
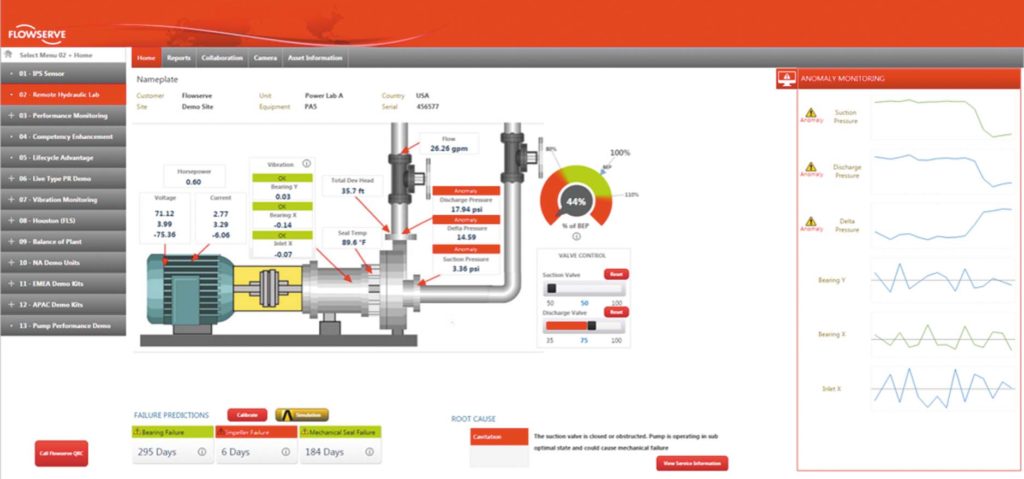
Через три года аналогичный цифровой двойник насоса, но уже на другой IoT-платформе, был создан компанией Grundfos.
Для пилотного проекта цифрового двойника насоса был выбран консольный центробежный насос Durco Mark 3 компании Flowserve, оснащенный базовой системой вибромониторинга, датчиками давления и расходомером. Для интеграции всех устройств, датчиков и анализа данных использовалась IoT-платформа ThingWorx компании PTC. Подсистема машинного обучения, встроенная в ThingWorx, использовалась для анализа информации с датчиков, построения шаблонов данных, характерных для нормальных режимов работы насоса, выявления аномалий, поиска закономерностей и прогнозов, а также для визуализации данных.
В 2019 году российская компания «КАДФЕМ Си-Ай-Эс» разработала собственный демонстратор цифрового двойника консольного центробежного насоса – первый в России пример реализации концепции гибридного цифрового двойника на промышленном уровне. В демонстраторе были реализованы следующие функции гибридного цифрового двойника:
Виртуальные датчики эталонного процесса, дублирующие показания физических датчиков.
Аналитический расчет гидравлических характеристик насоса на основе данных системной модели – гидравлического КПД и кавитационного запаса насоса.
Расчет показателей энергоэффективности насосной установки.
Предсказание остаточного ресурса критических деталей насоса и электродвигателя на основе методов регрессии для предсказания отказов по непосредственным измерениям параметров работы оборудования.
Для взаимодействия с оператором был разработан пользовательский интерфейс, показанный на рис. 4.
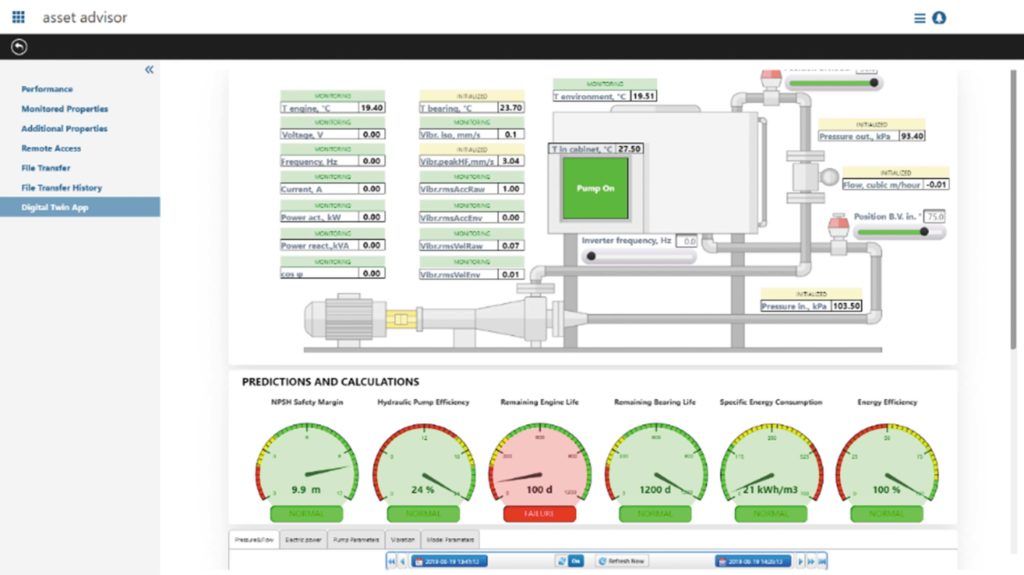
Экономический эффект от внедрения цифрового двойника насосного агрегата НПЗ
Экономический эффект от внедрения системы интеллектуальной (умной) и непрерывной диагностики технического состояния и регулирования режима работы насосного агрегата на основе цифрового двойника складывается из прямой и косвенной экономии. К прямой экономии относятся: снижение затрат на ремонт; увеличение межремонтного периода за счет необоснованных плановых ремонтов; минимизация объема ремонтных работ; экономия потребляемой электроэнергии (за счет регулирования режима работы насосной установки). Косвенная экономия складывается за счет снижения расходов, не связанных с производственными затратами: потери, возникающие в результате внеплановых простоев, например, убытки в виде неполученных доходов (упущенной выгоды) за отгрузку нефтепродуктов и затраты на исправление аварий.
Рассмотрим эффективность применения цифрового двойника на основе вибромониторинга и машинной аналитики на примере насоса циркуляционного орошения, используемого в вакуумной ректификационной колонне. Затраты на ремонт насоса по оценкам «ЛУКОЙЛ-ИНФОРМ» составляют 12000 долларов США, потеря прибыли 15000 долларов в час, общая утраченная прибыль 90000 долларов, общая стоимость отказа 158000 долларов.
Таким образом убытки от простоя оборудования в денежном выражении при отсутствии своевременной вибродиагностики и предиктивной аналитики циркуляционного насоса составляют 11 850 тыс. руб./год при двух внеплановых остановках. Если отмасштабировать эффект от внедрения цифровых двойников на все подобное оборудование НПЗ, то экономический эффект будет на несколько порядков больше. Срок окупаемости мероприятия при внедрении только виброанализатора стоимостью 1,5 млн руб. составит полтора месяца.
Расчет экономической эффективности разработки цифрового двойника насоса для НПЗ
Для расчета экономической эффективности реализации проекта гибридного цифрового двойника насосного агрегата необходимо оценить возможную длительность реализации проекта, а также его стоимость. Оценку длительности реализации проекта невозможно оценить методом сравнения/сопоставления с аналогичными проектами ввиду их отсутствия в России. При расчете стоимости проекта необходимо учитывать, как стоимость привлечения подрядных организаций, так и собственные расходы НПЗ. С учетом указанных фактов можно предположить примерные трудозатраты для реализации проекта цифрового двойника.
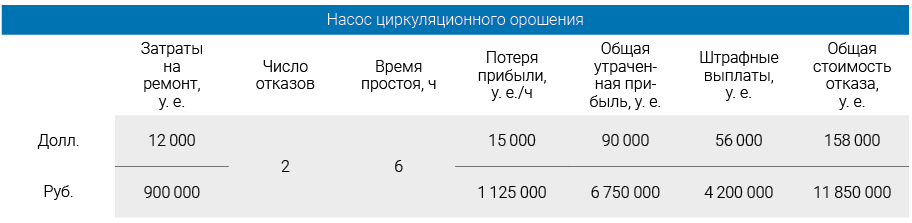
Команды из 10 технических специалистов будет более чем достаточно для реализации пилотного проекта цифрового двойника. Длительность реализации проекта цифрового двойника насоса на основе экспертной оценки составляет 12 месяцев, из них 6 месяцев – разработка программно-аппаратного комплекса, а оставшиеся 6 месяцев – опытно-промышленная эксплуатация (ОПЭ).
Суммарные затраты на инвестиционную стадию пилотного проекта составят 21,83 млн руб. Из них на проектные работы необходимо выделить 13 920 000 руб., на лицензирование программного обеспечения – 5 000 000 руб. и на аппаратное обеспечение – 2 910 000 руб.
Оценим ожидаемый экономический эффект от внедрения системы за счет снижения затрат на техническое обслуживание насосного оборудования и предотвращения незапланированного простоя оборудования. Введем следующие допущения и предположения:
процент запланированных потерь мощности: подразумевается, что НПЗ может продать восстановленную мощность;
годовой бюджет на ТО насосного оборудования – на основе данных открытых закупок ведущих российских нефтяных компаний («Роснефть», «Газпром нефть» и др.);
годовой бюджет обслуживания насосного оборудования не учитывает капитальные ремонты;
предотвращение затрат, связанных с более серьезными повреждениями, по отношению к техническому обслуживанию, проведенному до наступления условий отказа оборудования;
сокращение затрат на излишнее ТО, которое не требуется для обеспечения надежной работы (например, профилактическое обслуживание без выявления проблем);
сокращение затрат на операции, вызвавшие повреждение вследствие кавитации, механического износа и пр.
маржинальность НПЗ (коэффициент прибыльности на баррель) – на основе прогнозов аудиторских компаний «Большой четверки».
Предположим, что производительность НПЗ составляет 10 млн т/год (или 7,28×10×1 000 000/365=199 452 баррелей нефти марки Urals в сутки). Коэффициент прибыльности на баррель примем равным 3 долл. США. Потери производственной мощности НПЗ, связанные с отказами насосного оборудования – 0,2 %. Снижение потерь производства благодаря дистанционному мониторингу технологических насосов и предсказательной аналитике – 30 %. Предполагаемый годовой рост чистой прибыли составит 199452×3×0,002×365×0,3 =131 039 долл. США.
Оценим снижение годовых затрат на техническое обслуживание насосного оборудования. Годовой бюджет на техническое обслуживание насосного оборудования НПЗ – 12 млн долл. США. Общие годовые затраты на техническое обслуживание технологических насосов НПЗ – 7 %. Снижение средней стоимости ремонта без непредвиденных отказов насосов – 30 %. Таким образом снижение годовых затрат на техническое обслуживание составит 12 000 000×0,07×0,3=252 тыс. долларов. При текущем курсе доллара в 75 руб. за 1 долл. США можно предположить, что общий годовой рост прибыли составит 28 727 925 руб. (или ~2,39 млн руб. в месяц).
Результаты оценки эффективности инвестиций в проект при ставке дисконтирования 13,8 % представлены в табл. 2.
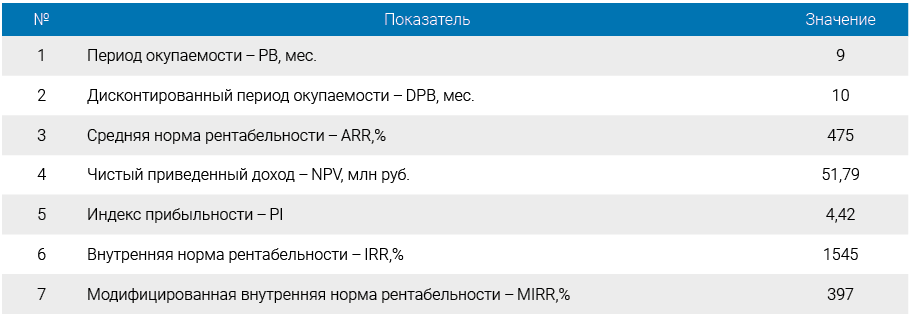
в проект цифрового двойника насосного агрегата
Анализ чувствительности проекта к цене сбыта показывает, что проект гибридного цифрового двойника насосного агрегата имеет более чем 70 % запаса по цене сбыта. При увеличении объема инвестиций в проект в два раза NPV проекта составит 30 млн руб.
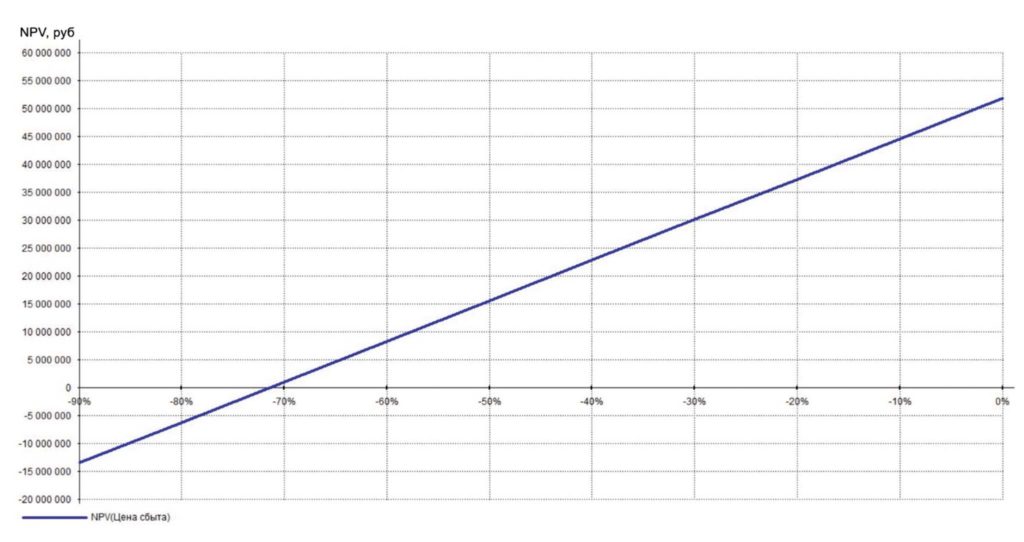
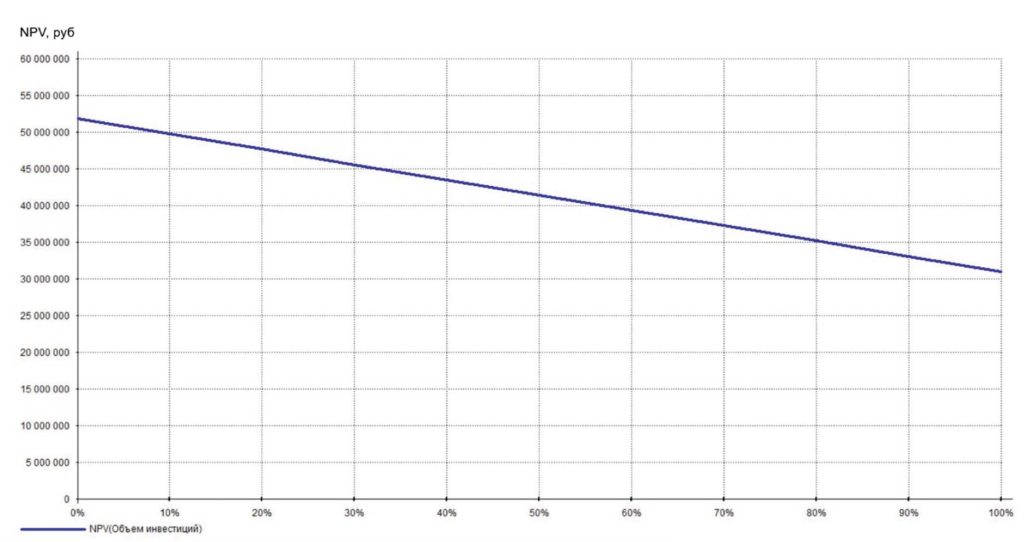
Заключение
Тенденция цифровизации большого количества рыночных сегментов набирает обороты. Нефтегазовая отрасль, являясь ключевой отраслью для российской экономики, не осталась в стороне от этого процесса.
Осуществление цифровой трансформации является сложной и неоднозначной задачей, при которой необходимо в первую очередь минимизировать риски внеплановой остановки предприятия из-за сбоев при внедрении новых технологий. Технология цифрового двойника насосного агрегата не вносит изменений в технологическую структуру, которые могли бы привести к остановке нефтеперерабатывающего предприятия (НПЗ).
Анализ международного опыта применения подобных проектов показал, что внедрение данной технологии на нефтеперерабатывающих предприятиях позволяет повысить эффективность технического обслуживания динамического оборудования на 20–30 %, сократить внеплановые простои оборудования на 15–20 %, уменьшить объемы обслуживания и ремонта на 15–20 % и снизить энергопотребление на одну тонну нефти на 2–5 %. В России также идут работы в этом направлении, но реальных примеров промышленного применения, оценки эффективности и стоимости подобных проектов пока нет.
Экономический эффект от внедрения гибридного цифрового двойника на НПЗ производительностью 10 млн т/год нефти составит порядка 30 млн руб. в год за счет снижения затрат на техническое обслуживание насосного оборудования и предотвращения незапланированного простоя оборудования.
Суммарные затраты на инвестиционную стадию проекта с учетом программного и аппаратного обеспечения и проектных работ составляют примерно 22 млн руб. Период окупаемости проекта (PB) – 9 месяцев, чистый приведенный доход (NPV) ~ 52 млн руб.