Ирина ИВАНОВА
Профессор, д. х. н., главный научный сотрудник, Московский государственный университет имени М. В. Ломоносова, химический факультет
e-mail: iiivanova@phys.chem.msu.ru
Ольга ПОНОМАРЕВА
Ведущий научный сотрудник, к. х. н., Московский государственный университет имени М. В. Ломоносова, химический факультет
e-mail: oaponomareva@phys.chem.msu.ru
Егор АНДРИАКО
Младший научный сотрудник,
Институт нефтехимического синтеза им. А. В. Топчиева РАН
e-mail: e.andriako@mail.ru
Николай НЕСТЕРЕНКО
Руководитель программы НИОКР по конверсии природного газа в компании «Тоталь» и лаборатории «Наноклеанэнержи» в национальной инженерной школе
г. Кана (Франция), к. х. н.
e-mail: nikolai.nesterenko@total.com
Цеолитные материалы играют важнейшую роль в нефтепереработке и нефтегазохимии. На фоне новых экологических стандартов, необходимости интеграции процессов нефтепереработки и нефтехимии, возрастающей роли экономики «замкнутого цикла» и водородной энергетики, их вклад будет только увеличиваться. Сегодня эти материалы имеют первостепенное значение для большинства ключевых каталитических процессов нефтегазохимии. Они используются в осушке, очистке, поглощении СО2 из газов горения и позволяют снизить энергозатраты на разделение и очистку и избежать выбросов в атмосферу. Декарбонизация промышленности, необходимость в переработке отходов и пластиков, а также электрификация отрасли, поставят новые задачи перед нефтегазохимией, в которых цеолиты окажутся в центре внимания. Развитие катализаторов и производство адсорбентов на основе цеолитов будет являться приоритетным направлением для жизнеспособности отрасли в последующие 30 лет и сыграет ключевую роль в достижении нулевого уровня выбросов к 2050 году.
Технологии нефтепереработки и нефтегазохимии на основе цеолитных катализаторов
Революционный прорыв в нефтехимии и нефтепереработке, который произошел в середине XX века и привел к существенному повышению эффективности, был связан с внедрением цеолитных катализаторов и созданием современных инновационных технологий на их основе. В настоящее время цеолиты как компоненты катализаторов применяются более чем в половине современных процессов нефтегазохимии.
Цеолиты представляют собой микропористые кристаллические алюмосиликаты с варьируемым составом и размером пор, сравнимым с размерами нефтехимичесих продуктов (0,3–1,2 нм). Мировое производство синтетических цеолитов в 2020 году составило 2200 тыс. тонн, из них 18 % используют в качестве компонентов катализаторов [1]. Основными преимуществами цеолитсодержащих катализаторов являются экологичность, химическая инертность, высокая химическая и термическая стабильность, широкая вариабельность структур, форм-селективность, возможность изменения свойств путем модифицирования, длительность работы, технологичность использования, а также регенерируемость, т. е. восстановление активности путем отжига кокса.
В нефтеперерабатывающей промышленности цеолиты используют в процессах каталитического крекинга (процесс FCC, цеолиты FAU и MFI) и гидрокрекинга (цеолиты FAU), гидроизомеризации С5-С6 парафинов (MOR), гидродеароматизации (FAU, MFI), депарафинизации и изодепарафинизации топлив и масел (MFI, TON, AEL) (рис. 1).
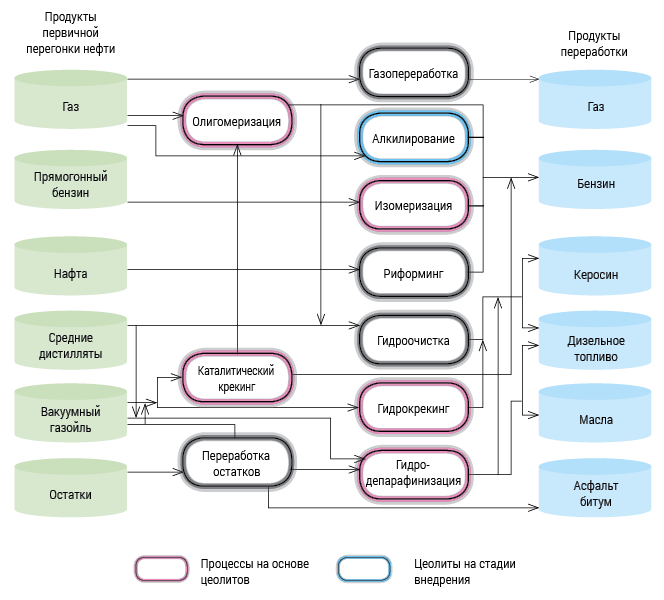
На базе цеолитсодержащих катализаторов созданы технологии изомеризации олефинов (FER) и их олигомеризации (MFI, MTT). В последние годы разработаны и внедрены три технологии твердофазного алкилиривания на цеолитах: Alkyclean® (ABB Lummus-Albemarle), Eurofuel® (Lurgi-Süd Chemie), ExSact ® (Excelus).
В нефтехимии и органическом синтезе цеолитные катализаторы применяются в процессах алкилирования бензола олефинами, ведущих к получению кумола и этилбензола, важных прекурсоров для полимерной промышленности, диспропорционирования толуола (MWW, MOR, MFI) и изомеризации С8 фракции алкилароматических углеводородов (EUO, MOR, MFI), ведущих к получению ксилолов, в процессе окисления пропилена в пропиленоксид (Ti-MFI), а также в ряде других (рис. 2). Замена цеолитсодержащими катализаторами жидких кислот Фриделя – Крафтса или фосфорной кислоты на кизельгуре, на которых проводили, а в большинстве стран, в том числе и в России, до сих пор проводят алкилирование, позволило решить целый ряд экологических, экономических и технологических проблем, связанных с низкой селективностью, коррозией оборудования, загрязнением окружающей среды, большим объемом сточных вод.
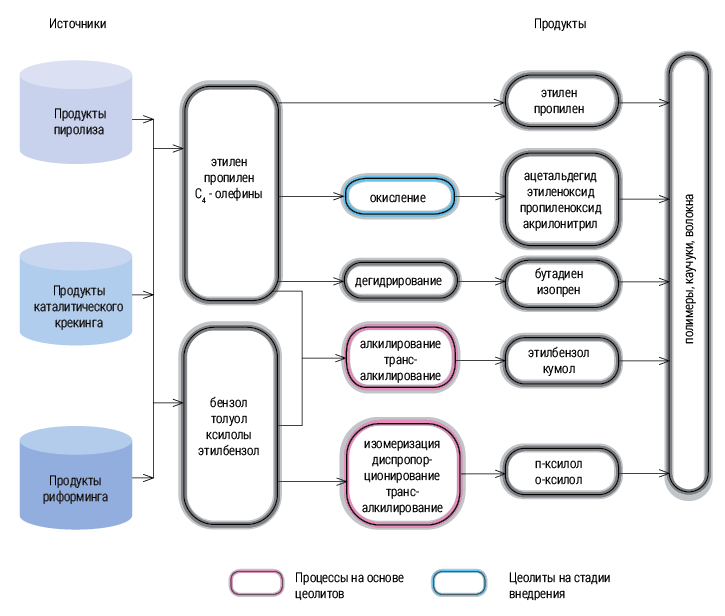
В области газохимии актуальной задачей сегодня является разработка цеолитсодержащих катализаторов целевой переработки алканов, которые позволят заменить пиролитические процессы переработки газа каталитическими, а также создание новых технологий монетизации газового сырья и получения на его основе ценных продуктов для промышленности. В настоящее время в газохимии на базе цеолитов MFI и SAPO‑34 внедрены процессы получения из природного газа через метанол/диметиловый эфир высокооктанового бензина (Mobil), этилена и пропилена (UOP, Lurgi, DCIP, Sinopec, JGC, ExxonMobil), изомеризации бутена в изобутилен на FER, и др. [2]
Состояние дел в России
В РФ, в отличие от других стран с высоким уровнем добычи нефти и газа, доля основных вторичных процессов переработки нефти от мощности первичной переработки в среднем составляет около 50 %. При этом общий объем процессов вторичной переработки нефти в России в разы меньше, чем в ведущих странах мира [3]. Решение проблем развития российской нефтегазохимии заложено в Плане развития газо- и нефтехимии на период до 2030 года, утвержденным приказом Минэнерго РФ 01.03.2012 г. Ключевым подходом для выполнения поставленных перед отраслью задач является внедрение новых и усовершенствование существующих технологий, в первую очередь, основанных на применении экологически безопасных твердых цеолитсодержащих катализаторов.
До недавнего времени инновационное развитие отечественной нефтегазохимии строилось на приобретении готовых технологий за рубежом, основанных на импортных катализаторах. В последние годы ситуация несколько изменилась.
В области нефтепереработки были разработаны, внедрены или находятся на стадии внедрения отечественные катализаторы крекинга на основе цеолитов FAU и MFI и гидрокрекинга (FAU), ведущие к получению бензина и дизельного топлива. Основными производителями этих катализаторов в России являются «Ишимбайский специализированный химический завод катализаторов» (10 тыс. т в год при мощности 20 тыс. т в год) и «Газпромнефть – Каталитические системы» (проектная мощность производства 15 тыс. т в год) [4]. В 2017 году на Московском НПЗ «Газпром нефти» внедрен катализатор процесса олигомеризации бутан-бутиленовой фракции, разработанный совместно со специалистами компании УНИСИТ, созданной на базе лаборатории кинетики и катализа химического факультета МГУ. Переход на новый катализатор позволил увеличить пробег и выход целевого продукта, сократить количество регенераций. По подсчетам специалистов Московского НПЗ, годовой эффект от использования нового катализатора олигомеризации превысит 200 млн рублей.
Разработан и готовится к внедрению новый катализатор гидродепарафинизации («Газпром нефть», ВНИИ НП), на основе цеолита MFI, модифицированного гидрирующим компонентом. Ведутся работы по созданию новой технологии твердокислотного алкилирования бутан-бутиленовой фракции на основе цеолитсодержащего катализатора (ИНХС РАН, «Газпром нефть»).
В области нефтехимии ведутся работы по внедрению технологий алкилирования и изомеризации ароматических углеводородов, основанных на цеолитных катализаторах. В 2003 г. в ОАО «Салаватнефтеоргсинтез» внедрен отечественный процесс жидкофазного алкилирования бензола этиленом, разработанный ИНХС РАН, «ГрозНИИ» и «Салаватнефтеоргсинтез» (мощность по этилбензолу 230 тыс. т/год). В настоящее время процесс работает на импортном катализаторе EBEMAX‑1 на основе цеолита MWW (Süd Chemie). С 2010 г. на предприятии «СИБУР-Химпром» действует установка алкилирования бензола этиленом по жидкофазной технологии EBMax с использованием в качестве катализатора цеолита MWW (мощность по этилбензолу 220 тыс. т в год). В 2018 году «Уфаоргсинтез» («Роснефть») завершило модернизацию установки по производству кумола по технологии ExxonMobil (170 тыс. тонн в год). Ведутся работы по модернизации производства кумола на «Омском каучуке» ГК «Титан» по технологии ExxonMobil (165 тыс. т в год), а также запланирована модернизация производства кумола на «Казаньоргсинтезе» на заводе «Бисфенол А» по технологии MobilBadger с использованием цеолитного катализатора MWW.
Уровень развития газохимической отрасли в РФ отстает от передовых стран, только 5 % добываемого газа используется как сырье для вторичной переработки [5]. Процессы, основанные на цеолитсодержащих катализаторах, в России пока не внедрены.
Качество производимого в России цеолита FAU соответствует мировым стандартам, но цеолит MFI по своим свойствам значительно уступает своим импортным аналогам. Цеолит MFI в РФ производится, главным образом, под товарными марками ЦВК, ЦВМ и ЦВН по отечественной технологии, разработанной во ВНИИНП еще в 1970–1980 гг. Если основные мировые производители выпускают цеолиты с размерами кристаллов 200–400 нм, то отечественные предприятия поставляют на рынок цеолит MFI с размером кристаллов 2–5 мкм. Как следствие, катализаторы на основе таких цеолитов характеризуются низкой эффективностью, повышенным коксообразованием и высокой скоростью дезактивации.
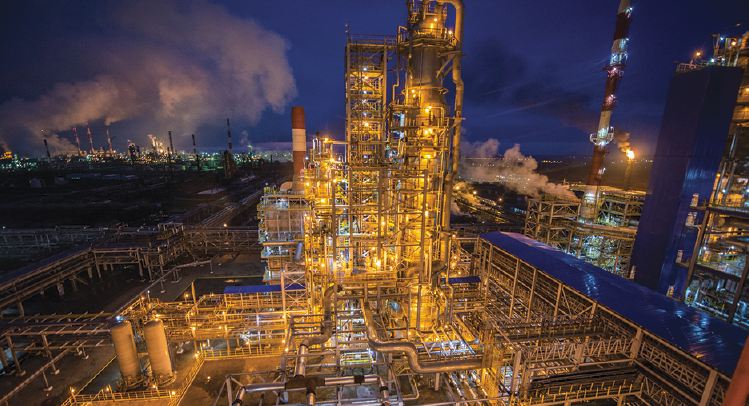
Источник: vbashkortostane.gazprom.ru
Вышеперечисленные факторы значительно снижают эффективность отечественных цеолитов MFI в качестве компонентов катализатора крекинга и делают невозможным их применение в процессах олигомеризации и депарафинизации. На настоящий момент потребность российского рынка в высококремнистых цеолитах MFI высокого качества составляет более 500 тонн в год для процессов крекинга, олигомеризации, депарафинизизации, ароматизации и др. Что касается цеолитных катализаторов нефтехимических процессов и процессов органического синтеза на основе высококремнистых среднепористых цеолитов ВЕА, MWW, MOR, ведущих к получению важных мономеров для полимерной промышленности – кумола, этилбензола, ксилолов, то их производство в России отсутствует.
Необходимость перехода к новым экологически чистым технологиям, обеспечивающим устойчивое развитие и прогресс нефтеперерабатывающей, нефтехимической и газохимической отраслей, требует разработки отечественных технологий производства цеолитов. Учитывая введение санкций в отношении России, эта проблема становится крайне актуальной.
В 2019 году в рамках программы Фонда содействия развитию малых форм предприятий в научно-технической сфере, на базе лаборатории кинетики и катализа МГУ была создана компания ООО «Цеолитика», целью которой является разработка новых современных технологий синтеза отечественных наноразмерных цеолитов разных структурных типов (MFI, BEA, MEL, MWW и др.) и их производство в промышленных масштабах для замены импортируемых катализаторов на отечественные. Научным коллективом была предложена новая технология парофазной кристаллизации в отсутствие свободной воды, конкурентными преимуществами которой являются высокое качество получаемых наноразмерных цеолитов, а также отсутствие жидких отходов кристаллизации, эффективное использование исходных реагентов и темплата, уменьшение времени кристаллизации, снижение энергозатрат [6].
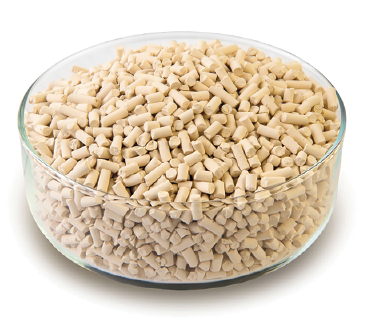
Источник: himiya-ufa.ru
Переход к новой энергополитике: инновации в области цеолитного катализа
В настоящее время человечество стоит на пороге очередной революции в области нефтепереработки и нефтехимии. Проблемы рационального использования природных ресурсов, а также все возрастающий вред антропогенного воздействия на окружающий мир вынуждают человечество к глобальному пересмотру подхода к своей деятельности. В ближайшие десятилетия будет осуществлен кардинальный пересмотр процессов нефтехимии и нефтепереработки с возрастающим ростом роли цеолитных материалов. Можно выделить пять основных приоритетных направлений:
- Интеграция нефтепереработки и нефтехимии.
- Операционная эффективность и цифровая трансформация (Индустрия 4.0).
- Декарбонизация нефтехимических комплексов и экономика «замкнутого цикла».
- Переход к новым сырьевым источникам, конверсия биомассы.
- Водородная энергетика и ренессанс газохимии.
Предполагается, что цеолитные катализаторы будут играть первостепенную роль в этом переходе.
Интеграция нефтехимии и нефтепереработки
Рост спроса на базовые продукты нефтехимии опережает рост спроса на топливо, поэтому многие предприятия, чтобы сохранить рентабельность, стремятся к созданию крупных нефтехимических комплексов, объединяющих нефтеперерабатывающие заводы и нефтехимические комплексы. Согласно Hydrocarbon Processing’s Construction Boxscore Database, на сегодняшний день в мире существует около 470 крупных проектов по увеличения мощностей нефтехимических комплексов стоимостью 10 миллиардов долларов. На долю России и стран ближнего зарубежья приходится около 55 проектов (12 %). Все большую популярность приобретают мегапроекты по глубокой интеграции НПЗ и НХК. Эти проекты нацелены на увеличение выхода химикатов на НПЗ с традиционных 10–15 % до 45–53 мас.% [7]. Реализация таких проектов в значительной степени зависит от доступности и готовности новых каталитических технологий. Большинство этих технологий опирается на инновации в области цеолитного катализа в процессах крекинга (FCC, гидрокрекинг), в целевой нефтехимии (селективный крекинг олефинов, каталитический крекинг нафты, дегидрокрекинг нафты, разделение линейных и разветвленных углеводородов, обратная изомеризация) и в ароматическом комплексе (новые технологии по получению ксилолов).
Существует пять основных стратегий интеграции с целью увеличения выхода нефтепродуктов на нефтеперерабатывающих комплексах путем введения технологий «целевой нефтехимии». Первая схема включает модернизацию FCC комплекса путем его интеграции с селективным крекингом тяжелых олефинов из бензиновой фракции в пропилен. Эта схема предполагает оптимизацию цеолитного катализатора для установки FCC и ведет к гораздо более высокому выходу этилена и пропилена. Вторая стратегия предполагает введение процесса гидрокрекинга дистиллята в легкие алканы и нафту с последующим пиролизом алканов в олефины и конверсией нафты в ароматические углеводороды. Следующая стратегия основана на «молекулярном рефайнинге» на цеолитах, включающем разделение СУГ на пропан и бутан с последующей их конверсией в пропилен и бутены, а также разделение линейных и разветвленных парафинов в нафте с последующей изомеризацией разветвленных углеводородов в линейные и их пиролизом в этилен и пропилен. В результате этой операции только нормальные парафины подвергаются конверсии в установке пиролиза, что увеличивает выход легких олефинов на 10–15 %. Четвертая стратегия связана с введением процесса метатезиса олефинов, что открывает широкие возможности для увеличения выхода этилена и пропилена. И, наконец, пятая стратегия основана на каталитическом (дегидро-) крекинге нафты, который позволяет значительно повысить выход пропилена и этилена по сравнению с процессом пиролиза. Реализация перечисленных стратегий позволит повысить выход нефтепродуктов с 10–15 % до 30–50 %, что соответствует полностью интегрированному комплексу.
Следующим этапом эволюции будет прямая конверсия нефти в продукты нефтехимии путем крекинга. Этот вариант ведет к снижению производственных затрат и выбросов СО2 на тонну продукта. На настоящий момент существует как минимум три стратегии для осуществления этого этапа. Они основаны на процессах FCC, гидрокрекинга и пиролиза. Выбор схемы зависит от вида сырья и типа нефтепродуктов, которые завод должен производить. Во всех трех случаях, инновации в области цеолитного катализа будут играть основополагающую роль.
Операционная эффективность и цифровая трансформация (Индустрия 4.0)
Основой операционной эффективности производства является надежность и детальное знание процесса и катализатора. Цеолитные катализаторы более 60 лет используются в промышленности и зарекомендовали себя как надежные, безопасные и эффективные. Однако разработка новых технологий на основе цеолитов занимает длительное время, в среднем от 10 до 15 лет, что не совместимо с ростом спроса на эти технологии. Увеличение скорости внедрения новых разработок может быть достигнуто путем использования моделирования, информатики материалов и искусственного интеллекта. Необходимым условием внедрения технологий цифровой трансформации в этой области является создание библиотек цеолитных материалов и катализаторов, подготовка специалистов и поддержка научных школ в области цеолитного катализа.
Декарбонизация нефтехимических комплексов и экономика «замкнутого цикла»
В соответствии с Парижским соглашением по климату от 2015 года, главным врагом климата объявлены парниковые газы, в основном диоксид углерода, а значит, косвенно, и источники его образования – нефть, газ, уголь. В мировой практике по инициативе ЕС вводится система отчетности по так называемому «углеродному следу», другими словами при производстве любого вида товаров и услуг будет оцениваться эмиссия парниковых газов. Правительства практически всех стран мира вводят углеродный налог – плату за выбросы эквивалента углекислого газа в атмосферу. По оценке российской академии наук, финансовые потери отечественных экспортеров могут достичь 3–4 млрд евро в год.
Таким образом, для российской нефтегазохимии необходимо пересмотреть сложившиеся реалии экспортно-сырьевого развития. Основой развития должен стать выпуск высокотехнологичной, высококачественной продукции более высоких переделов на базе ресурсо- и трудосберегающих экологически чистых технологий.
В первую очередь потребуется внедрение технологий для улавливания углекислого газа, его хранения и переработки. Цеолитные технологии будут играть первостепенную роль в этом отношении [8]. Прежде всего, цеолитные материалы могут быть использованы для улавливания СО2 из газов горения при низком парциальном давлении компонентов и его очистки для последующей транспортировки. Использование цеолитов в процессах разделения позволит значительно снизить потребление энергии и, соответственно, выбросы антропогенных газов.
Помимо этого, важной задачей станет утилизация СО2 путем его конверсии в полезные продукты. В этом отношении перспективными являются процессы «замкнутого цикла». В настоящее время рассматриваются 2 таких цикла, которые взаимосвязаны между собой (рис. 3). Наиболее приемлемым решением для утилизации СО2 будет его конверсия в метанол. Метанол может найти большое количество применений на нефтеперерабатывающем комплексе, но одним из наиболее перспективных решений будет его конверсия в олефины, ароматические углеводороды и в топлива (процессы MTO, MTG). Процесс получения метанола потребует использования больших количеств водорода, который также может быть получен на основе цеолитных технологий (пп 3.5).
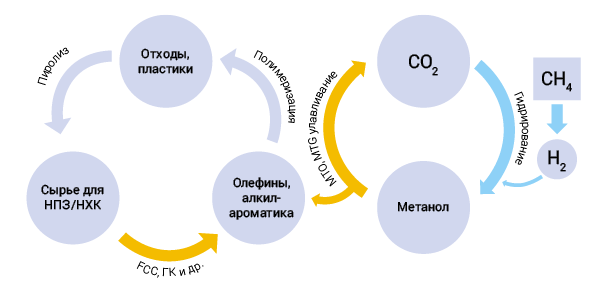
Процессы конверсии метанола в олефины и ароматические углеводороды весьма перспективны в связи со значительным ростом спроса на пластики, получаемые из этих мономеров. Получение пластиков из метанола будет решать задачу экономики «замкнутого цикла», которая является одной из наиболее важных задач для нефтехимии сегодня. Отходы от использования пластиков все больше рассматриваются как один из основных источников загрязнений и обеспечение их эффективной переработки является необходимым для существования отрасли. Наиболее оптимальным направлением такой переработки будет термический пиролиз, продукты которого будут перерабатываться на интегрированных нефтехимических комплексах, на установках FCC и гидрокрегинга на цеолитных катализаторах, давая в конечном результате олефины и ароматические углеводороды, необходимые для синтеза пластиков. Цеолиты, таким образом, будут продолжать играть первостепенную роль в процессах «замкнутого цикла».
Еще одним аспектом экономики «замкнутого цикла» является электрификация конверсии углеводородов. В настоящее время большинство печей, компрессоров и генераторов водяного пара на НПЗ используют углеводороды в качестве топлива. В результате сжигания этих продуктов образуются СО2‑содержащие газы. Абсорбция аминами не эффективна для этих типов потоков и улавливание углекислого газа из них стоит очень дорого. Поэтому одной из современных тенденций является замена топливных нагревательных элементов на электрические, в которых энергия будет подаваться в объем реактора. Другими словами, не стенки реактора будут подвергаться нагреву, а катализатор. Это также значительно упростит регенерацию и снизит инертность систем. Новое поколение катализаторов на основе цеолитов должно быть разработано для этих типов установок.
Переход к новым сырьевым источникам, конверсия биомассы
Растущий спрос на биотопливо обусловлен несколькими ключевыми причинами, первая из которых заключается в том, что биоресурсы являются возобновляемыми и нейтральными по отношению к CO2 в отличие от ископаемого топлива. Использование биомассы для производства топлива и химикатов может привести к частичному замещению ископаемых ресурсов возобновляемыми источниками. Многие государства в последнее десятилетие выделяют большие ресурсы для создания технологий для переработки биомассы [9].
Биомасса, как и нефть, состоит из высокомолекулярных компонентов. Основными источниками биомассы являются лигноцеллюлоза и липиды, которые содержат триглицериды из растительных животных жиров и микроводорослей. Из них наиболее распространенной является лигноцеллюлозная биомасса, состоящая из целлюлозы, гемицеллюлозы и лигнина. Кроме того, существует меньшая группа белковых фракций животного или растительного происхождения. Схема переработки биомассы приведена на рис. 4.
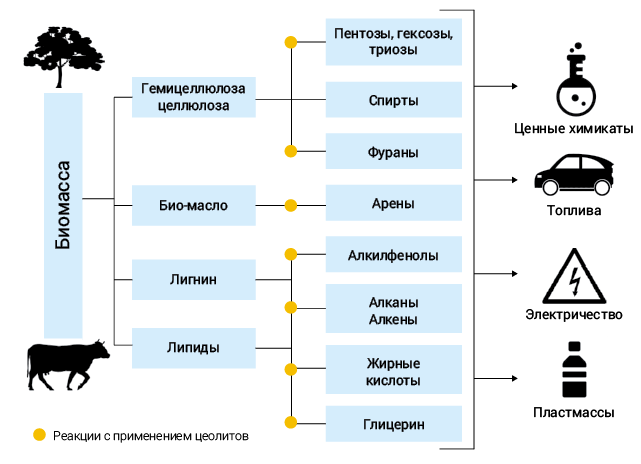
Основная цель валоризации биомассы состоит в уменьшении молекулярной массы. По аналогии с процессами конверсии нефти здесь могут быть использованы процессы каталитического крекинга на цеолитных катализаторах. Жиры и масла, имеющие длинные линейные углеводородные цепи, структурно наиболее близки к нефтехимическим углеводородам, поэтому в данных процессах цеолиты используются с большим успехом. Однако следует ожидать, что механизмы превращения громоздких субстратов биомассы, содержащих большое количество кислорода, более сложные и требуют создания новых каталитических систем [10]. Рядом компаний разработаны процессы прямого крекинга в установках типа FCC сухой биомассы. Ко-процессинг на установках FCC или гидрокрекинга нефтяного сырья с биосырьем, прошедшим этапы частичного гидрирования или термического пиролиза, является оптимальным решением во многих случаях. Это также позволяет избежать дополнительных инвестиций и значительных изменений в операционных схемах.
Другим интересным вариантом является конверсия спиртов. Этанол и бутанол в настоящее время в больших количествах производятся из возобновляемых источников. Помимо их использования в качестве биотоплива, конверсия биоэтанола и биобутанола в ценные химические вещества становится все более привлекательной. Перспективные технологии включают конверсию этанола в этилен, пропилен и бутадиен, а также конверсию бутанола в бутены, легкие олефины и ароматические углеводороды. Для этих процессов разработаны эффективные цеолитные катализаторы.
Водородная энергетика и ренессанс газохимии
Водород является высокоэнергетическим продуктом и может быть использован как для внутренних нужд нефтехимических комплексов, так и для конверсии CO2. На сегодняшний день основным способом производства водорода является паровая конверсия. Однако этот способ приводит к выделению 9,3 тонн СО2 на тонну водорода, который требует улавливания и соответствующей инфраструктуры для этого (рис. 5). Альтернативная технология, основанная на электролизе воды, поглощает в 5 раз большее количество энергии на тонну водорода. В связи с этим, прямая декарбонизация природного газа в углерод, олефины или ароматические углеводороды приобретает все большее значение для водородной энергетики. Первый процесс имеет серьезный недостаток, так как приводит к образованию большого количества кокса, который не имеет рынка сбыта. Поэтому, процессы превращения метана в водород и олефины или ароматику гораздо более перспективны. Эти процессы могут эффективно протекать на цеолитах. Многие из этих технологий находятся в стадии разработки и будут играть значительную роль для нефтегазохимии.
Кроме того, все большее значение в будущем будут иметь процессы получения водорода путем ароматизации легких алканов, доля которых увеличится из-за интеграции нефтехимических комплексов. В основе этих процессов также лежат цеолитные катализаторы (процессы CICLAR (UOP), ALPHA(ASAHI), AROMAX(CHEVRON)).
Заключение
Анализ перспектив развития нефтегазохимической отрасли в области цеолитного катализа показывает, что первоочередной задачей здесь является разработка и внедрение отечественной технологии синтеза наноразмерных высококремнистых цеолитов структурных типов MFI, BEA, MWW и MOR, необходимых для обеспечения действующих нефтехимических производств.
Кроме того, актуальной задачей представляется создание новых цеолитных катализаторов и технологий для обеспечения интеграции НПЗ и НХК; создания прямых процессов конверсии нефти в ценные продукты нефтехимии; реализации процессов «замкнутого цикла» – конверсии CO2, отходов и пластиков в мономеры и топлива; осуществление конверсии биомассы в топлива и ценные химические продукты, а также конверсии метана в водород и олефины или ароматические углеводороды. Реализация этих задач позволит осуществить переход к новой энергетической политике.