Александр НОСКОВ
Заместитель директора по науке, д. т. н., профессор, ФИЦ «Институт катализа СО РАН»
e-mail: noskov@catalysis.ru
Максим КАЗАКОВ
Ученый секретарь, с. н. с., к. х. н., ФИЦ «Институт катализа СО РАН»
e-mail: kazakov@catalysis.ru
К нетрадиционным ресурсам углеводородов относятся ресурсы, залегающие в сложных геологических условиях, освоение которых нуждается в применении новых методов и способов их разведки, добычи, переработки и транспортировки с учетом геолого-технических, экономических, социальных и экологических факторов [1]. В таблице 1 приведена классификация основных видов нетрадиционных (трудноизвлекаемых) нефти и газа, представленная в [2].
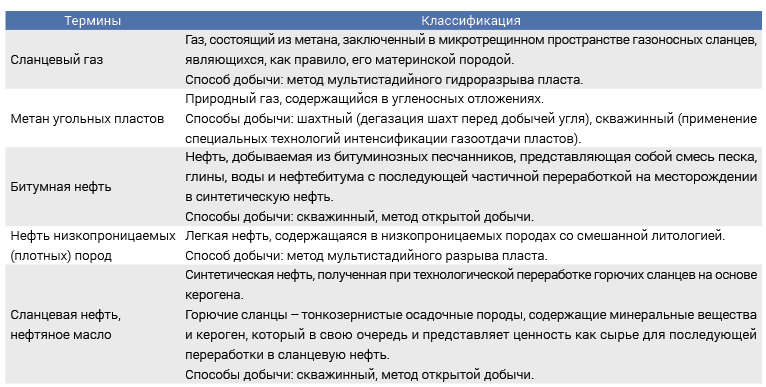
Отношение ресурсов природного газа/сланцевого газа/метана угольных пластов составляет 1:1:1 и оценивается по каждому из источников примерно в 200 трлн кубометров. Гораздо больший потенциал углеводородного сырья по сравнению с традиционной нефтью кроется в ресурсах природных битумов и горючих сланцев.
Оценки показывают, что в первой половине XXI века добыча традиционной нефти в мире достигнет исторического максимума, который будет удерживаться в течение около 10 лет, а затем уровень добычи начнет снижаться [3]. Нетрадиционное углеводородное сырье привлекает значительное внимание в качестве одного из наиболее очевидных источников для расширения сырьевой базы нефтеперерабатывающих предприятий. Это связано, прежде всего, с истощением запасов традиционной нефти с одной стороны, и ростом спроса на высококачественные нефтепродукты с другой стороны. Кроме того, суммарное содержание углеводородов в нетрадиционных источниках существенно превышает суммарные запасы традиционных нефтей (см. таблицу 2) [4].
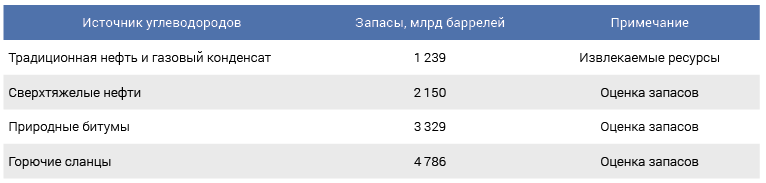
Суммарные мировые запасы углеводородов нефтяного направления оцениваются в 1,7–1,8 трлн тонн, причем, доля традиционной нефти в этом пуле не превышает 10–12 %. Вовлечение в производство источников нетрадиционного углеводородного сырья осложняется относительно низким соотношением водород/углерод в их органической составляющей (см. рис. 1) [5].
Далее приведем характеристики, оценки ресурсов в разных регионах и направлений переработки природных битумов и горючих сланцев.
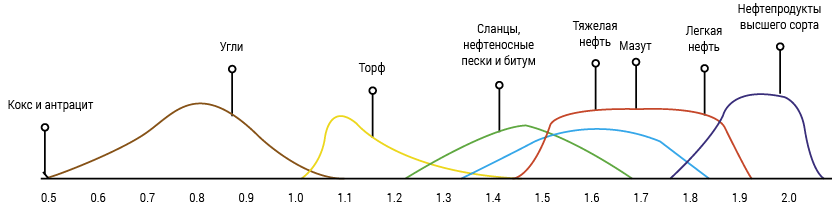
Природные битумы
Природные битумы находятся преимущественно в форме битуминозных песков. Понятие битуминозный песок обычно используется для описания песчаника, пропитанного тяжелым вязким битуминозным материалом природного происхождения, который практически неподвижен в условиях месторождения. Битуминозный песок представляет собой смесь песка, воды и битума [6,7]. Тяжелый органический материал имеет очень высокую вязкость в условиях пласта и не может быть извлечен из скважины обычными методами добычи, включая применяемые в настоящее время методы интенсификации нефтедобычи [8]. Наиболее высококачественные битуминозные пески содержат до 18 мас.% битума, который по своей консистенции может быть эквивалентен атмосферному или вакуумному нефтяному остатку.
В таблице 3 приведены данные о запасах природных битумов в различных регионах мира [4].
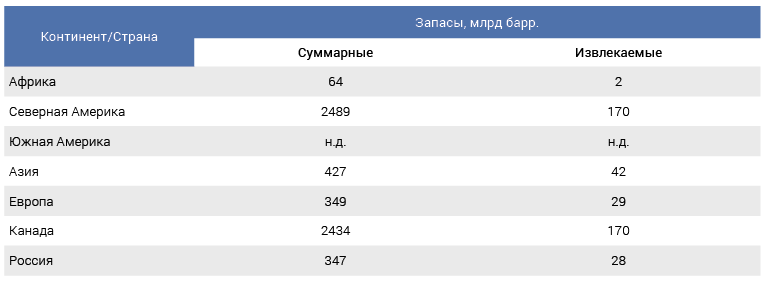
Как видно из приведенных данных, основная часть мировых запасов природного битума (около 2/3) находится в Канаде. В большинстве стран, для проведения точных оценок запасов природных битумов, данных явно недостаточно. Например, предварительная геологическая информация указывает на значительные ресурсы природных битумов на Восточно-Сибирской платформе. Однако в данной местности получены оценки ресурсов только для Оленекского месторождения. Подробная геологоразведка с целевой установкой на природные битумы приведет, по-видимому, к существенному пересмотру отношений ресурсов природных битумов между регионами мира.
По сравнению с традиционной нефтью, в которой содержание углеводородов может достигать 97 мас.%, природный битум может содержать не более 50–60 % углеводородных компонентов. Остальная часть представлена соединениями, содержащими серу, кислород, азот, металлы. Высокое содержание в природных битумах асфальтенов и смол также осложняет их квалифицированную переработку в товарные нефтепродукты (моторные топлива, сырье для нефтехимии).
Горючие сланцы
Горючие сланцы являются полезным ископаемым, состоящим из органической (сапропелевой или гумусово-сапропелевой) и минеральной (известковой, глинистой, кремнистой и др.) частей. Содержание органического вещества в горючих сланцах может составлять от 10–30 до 50–70 мас.%, а содержание водорода достигает 7–10 % масс. Основная масса (90–95 %) органического вещества представляет собой нерастворимое в органических растворителях твердое вещество, называемое керогеном. Потенциальные ресурсы горючих сланцев в мире огромны и оцениваются примерно в 4,8–5 трлн баррелей сланцевого масла (продукта термической переработки). Ресурсы горючих сланцев по регионам и странам приведены в таблице 4.
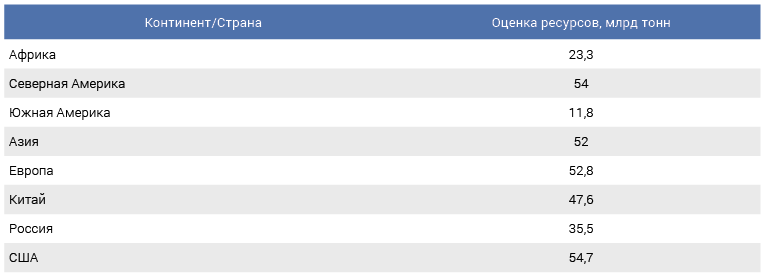
Точность приведенных данных оставляет желать лучшего. Только запасы нескольких месторождений горючих сланцев описаны достаточно точно (например, месторождение Грин-Ривер в США, месторождения в Эстонии). Стоит обратить внимание на относительную равномерность распределения ресурсов углеродистых сланцев по регионам мира.
Основным органическим составляющим горючих сланцев является кероген, который представляет собой случайное сочетание углеводородных мономеров. Получение жидких углеводородов из горючих сланцев возможно за счет термического разложения керогена. Температура, при которой начинается активное разложение керогена, достаточно близка для горючих сланцев различного происхождения и составляет около 350 °C [9].
В таблице 5 приведены данные о составе органической и минеральной части горючих сланцев различных месторождений.
Для горючих сланцев характерно повышенное содержание водорода, что способствует образованию жидких и газообразных продуктов при их термической обработке. По показателю углерод/водород горючие сланцы ближе к нефти, чем другие горючие ископаемые (каменные угли, торф, битумы).
Получение жидких нефтепродуктов из природных битумов и горючих сланцев
При переработке битуминозных песков и горючих сланцев получают жидкое углеводородное сырье, которое не встречается в природе. Получаемый при переработке продукт чаще всего называют синтетической нефтью.
Добыча и переработка природных битумов. Промышленная добыча природных битумов из битуминозных песков началась в Канаде в 60‑х годах XX века. Меньшая часть (до 20 %) природных битумов Канады может быть извлечена карьерным методом. Для добычи природных битумов также активно используются скважинные методы, базирующиеся на обработке битуминозных песков горячим теплоносителем или растворителем.
Основной коммерческой технологией извлечения природного битума из добытых карьерным методом битуминозных песков является экстракция горячей водой. Этот метод предусматривает размягчение битумов при смешении с горячей водой или паром с последующим разделением песка и битума. Дальнейшая очистка битумов от воды и твердых частиц производится на второй стадии процесса путем экстракции битумов легкими углеводородными растворителями (нафта, керосином и др.). После экстракции растворитель выделяет из состава битумов.

Одной из основных проблем, возникающих при отделении битума от битуминозного песка экстракцией горячей водой, является необходимость дорогостоящего процесса утилизации хвостовых шламов, содержащих остатки битумов, щелочи и другие загрязнители, осаждение которых происходит в осадительных прудах (шламовых озерах), занимающих огромные площади. Шламовые отходы содержат большое количество глин и состоят примерно из 49–50 мас.% песка, до 1 мас.% битума и примерно 50 мас.% воды. Кроме того, для этих технологий характерны значительный расход воды, тепла, растворителей.
Скважинные методы начали активно применяться для промышленного извлечения битумов позже, чем открытые карьерные методы. Степень извлечения битумов для таких методов варьируется от 10 % (холодное извлечение битума с песком) до 70 % (метод парогравитационного дренажа) и потенциально более 80 % для технологий подземного сжигания [10]. Из тепловых методов впервые был освоен метод циклического воздействия паром на пласт, позже – метод непрерывного парогравитационного дренирования с использованием двух горизонтальных скважин, расположенных одна над другой.
Скважинные термические методы, как правило, требуют для извлечения битумов значительно больших энергозатрат, чем методы открытых карьерных разработок. Поэтому, в настоящее время ведутся исследования и разработки новых скважинных технологий, без использования водяного пара. Наиболее перспективной из них является технология подземного сжигания части битумов по направленному фронту вдоль горизонтальной скважины.
В соответствии с этой технологией [11] на пути извлекаемых горячих битумов в пласте вдоль горизонтального участка продуктовой скважины размещается слой катализатора крекинга тяжелых углеводородов. Он может размещаться внутри горизонтального перфорированного участка скважины, или в пласте вокруг него. В эту же зону, при необходимости, по отдельной скважине, проведенной внутри или рядом с воздухонагнетательной скважиной, могут закачиваться восстановительные газы (Н2 или СО). Под действием высоких температур в присутствии восстановительных газов в слое катализатора происходит расщепление тяжелых углеводородов, деметаллизация и обессеривание битумов, снижение их вязкости. Поскольку катализатор распределен вдоль всей скважины, и участки катализатора постепенно, по частям открываются перерабатываемым битумам по мере перемещения фронта горения, то для каждого участка сохраняется соответствующая зона свежего катализатора высокой активности.
Выделенные из битуминозных песков битумы имеют очень высокую вязкость и непригодны для транспортировки трубопроводным транспортом. Для того чтобы удовлетворить требованиям перекачки по трубопроводам по показателям плотности и вязкости, используют два подхода. Первый подход основан на разбавлении битумов более легкими углеводородами (легкой нефтью, нафтой, газовым конденсатом). Второй подход предполагает частичную переработку битумов в более легкую синтетическую нефть вблизи районов добычи и транспортировку полученной синтетической нефти на НПЗ без разбавления.
Для переработки битумов в синтетическую нефть используются следующие основные подходы:
- Удаление углерода: висбрекинг, паровой крекинг, коксование. Процессы удаления углерода достаточно привлекательны, поскольку они проводятся при низком давлении и не требуют дорогостоящих катализаторов. При переработке битумов в синтетические нефти этот способ используют в большинстве случаев.
- Добавление водорода: каталитическая гидроконверсия (гидроочистка, гидрокрекинг), гидровисбрекинг и донорно-сольвентные процессы. Процессы гидроочистки битума обеспечивают удаление серы, азота, металлов и, таким образом, подготовку для дальнейшей переработки другими процессами. Гидрокрекинг обеспечивает получение более легких дистиллятов (керосины, дизельные фракции) и низкосернистых остатков.
Процесс переработки битумов в синтетическую нефть осуществляется в два основных этапа. Сначала производят первичную переработку битумов при которой достигается увеличение соотношения водород/углерод за счет: а) удаления углерода или б) добавления водорода. После этого полученные продукты первичной конверсии разделяют и перерабатывают в процессе гидроочистки для удаления серы и азота. Полученная синтетическая нефть далее может транспортироваться на НПЗ для переработки в различные жидкие топлива, такие как бензин, керосин и дизельное топливо. При дальнейшей переработке синтетической нефти необходимо учитывать, что составы синтетических нефтей отличаются от естественных нефтей той же плотности. Во-первых, в большинстве из них нет вакуумного остатка, что непривычно для НПЗ, работающих по схеме с коксованием вакуумного остатка. Кроме того, в синтетических нефтях мало бензина, много газойлей, в том числе тяжелого вакуумного газойля, а также высокое содержание ароматических соединений. Поэтому дизельные топлива, получаемые из такого сырья, имеют низкое цетановое число. В связи с этим для переработки синтетических нефтей требуются увеличенные мощности гидрокрекинга вакуумных газойлей. Поскольку часто синтетические нефти являются продуктом термического крекинга, то для них характерно высокое содержание олефинов, что в случае отсутствия гидроочистки и их насыщения вызывает их нестабильность при хранении и транспортировке. Чаще всего при переработке на действующих НПЗ синтетическую нефть смешивают с естественными нефтями для приближения к обычным составам.
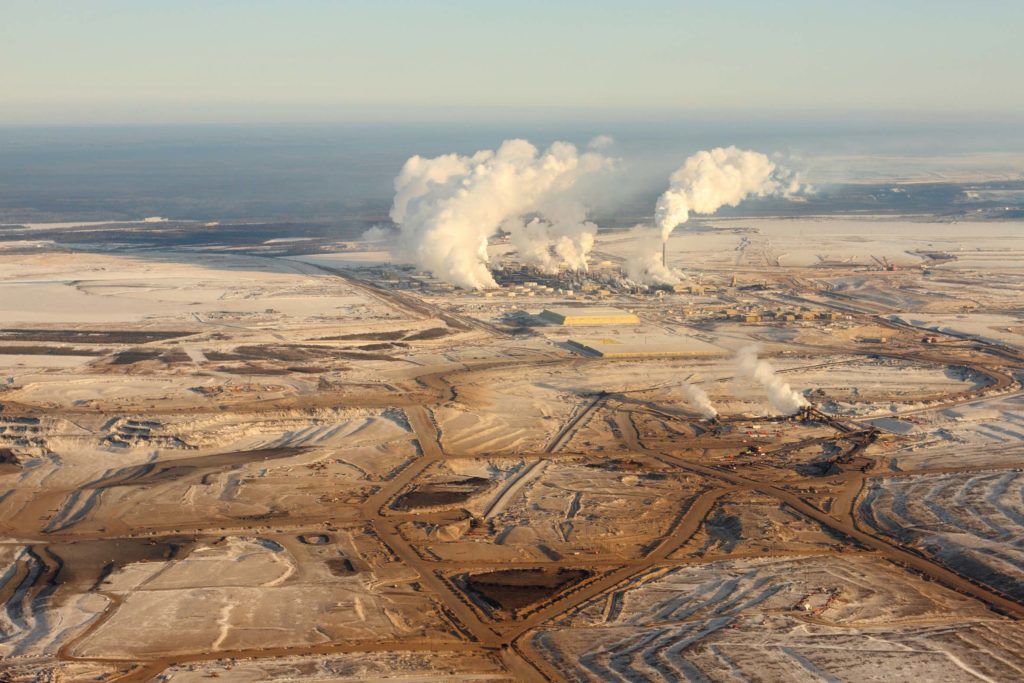
Источник: medium.com
Процессы коксования – основные процессы облагораживания битумов, с помощью которых они превращаются в дистиллируемые продукты. В процессе коксования битум конвертируется в дистиллируемые фракции, кокс и легкие газы. Полученные дистилляты подвергаются гидроочистке с получением малосернистой синтетической нефти. В целом состав продуктов, получаемых в результате коксования, близок для битума и тяжелых нефтяных остатков традиционной нефти.
Увеличение соотношения водород/углерод обеспечивается также использованием процессов гидрокрекинга [12]. Процессы гидрокрекинга могут рассматриваться как альтернатива процессам коксования. Общий выход жидкости при гидрокрекинге битума значительно выше, чем при коксовании. При этом также удаляются значительные количества серы и азота. Однако распространение данных процессов в настоящее время сдерживается в связи с необходимостью больших мощностей по производству водорода.
Переработка горючих сланцев. Современные практически реализованные технологии термической переработки горючих сланцев основаны на пиролизе с образованием газообразных, твердых (кокс) и жидких (нафта, дистиллятное топливо) продуктов [5]. При пиролизе происходит деполимеризация макромолекул керогена. Процессы пиролиза основаны на нагреве исходных горючих сланцев до определенной температуры в отсутствии кислорода. Наряду с традиционными процессами термической переработки развивается ряд альтернативных способов переработки горючих сланцев.
В качестве таковых можно отметить процесс гидрокрекинга в псевдоожиженном слое горючих сланцев и битуминозных песков. В этом случае синтетическая нефть из битуминозных песков, горючих сланцев, природных битумов образуется за счет гидрокрекинга и гидрогенизации в псевдоожиженном потоке сырья, в котором необходимый режим температуры и давления создается потоком горячего водорода под давлением. Проведение процесса в среде водорода обеспечивает более высокий выход целевых продуктов, а также более высокое их качество [13].
В 1950–1980‑е гг. был предпринят ряд попыток разработки технологий подземной переработки горючих сланцев. Интерес к методам подземной переработки горючих сланцев обусловлен рядом причин: отпадает необходимость в шахтной добыче сланца и сооружении наземных агрегатов для полукоксования сланца, что требует длительного времени и значительных капитальных затрат. Однако все работы по данным проектам были остановлены из-за низкой рентабельности и тех или иных недостатков предложенных технологий. В настоящее время подземной переработки горючих сланцев не ведется и данное направление можно считать неперспективным.
Горючие сланцы некоторых месторождений содержат целый ряд сопутствующих компонентов (например, молибден, ванадий, уран и др.) в количествах, близких к промышленным. Например, содержание U3O8 в урансодержащих горючих сланцах месторождения Ран Стад (Швеция) оценивается в 1 млн тонн. Если учесть, что образование сланцезольных остатков от сжигания сланцев в отдельных случаях достигает десятков миллионов тонн в год, то создаются благоприятные условия для извлечения некоторых минеральных компонентов. Сланцевая зола, полученная после пиролиза, также может найти применение в строительной промышленности для получения цемента. Таким образом, наличие сопутствующих полезных ископаемых и редких элементов может существенно изменить перспективы промышленного освоения сланцевых месторождений. При условии комплексного использования горючих сланцев и залегающих совместно с ними других полезных ископаемых может оказаться экономически целесообразным переработка сланцев с пониженной теплотой сгорания.
Заключение
Ресурсы нетрадиционного углеводородного сырья на Земле значительно превосходят аналогичные как по природному газу, так и по нефтяному сырью. Доля традиционного природного газа в суммарных ресурсах газообразных углеводородов не превышает 1/3. В этих оценках не учтены запасы метана в форме газовых гидратов, что еще более снизит долю традиционного природного газа. В нефтяном направлении доля традиционной нефти в мировых ресурсах нефтеориентированного сырья оказывается еще ниже и не превышает 10–12 %.
Для вовлечения в производство нетрадиционных ресурсов газообразных углеводородов (сланцевый газ, метан угольных пластов) требуется, прежде всего, решение проблем их добычи. При наличии эффективных технологий добычи дальнейшее использование этого газообразного углеводородного сырья, как правило, не вызывает каких-либо технологических проблем. Гораздо большие трудности открываются при вовлечении в промышленное использование нефтеориентированных нетрадиционных ресурсов (природных битумов, горючих сланцев). В данном случае требуется решение технических проблем как добычи этого сырья, так и переработки добытого сырья в подходящие жидкие углеводороды (синтетическую нефть). Только после этого возможна высококвалифицированная переработка полученных синтетических продуктов на существующих нефтеперерабатывающих заводах. В настоящее время себестоимость добычи битумной нефти составляет 20–40 долларов за баррель. Оценочная себестоимость получения синтетической нефти из горючих сланцев значительно выше. В современных рыночных условиях нетрадиционные нефтеориентированные ресурсы можно оценить как значимые для мировой экономики только в будущем.
Российская нефтедобывающая промышленность уже в обозримом будущем может столкнуться со снижением добычи нефти ввиду исчерпания ее разведанных запасов и отставания в приросте запасов нефти за счет геологоразведочных работ. При этом российские нефтегазовые месторождения характеризуются большой удаленностью от потребителя и сложными природно-климатическими условиями, что значительно увеличивает себестоимость добычи и повышает расходы на транспортировку. Одним из вариантов решения проблемы снижения добычи нефти в России может стать организация добычи углеводородов из нетрадиционных источников. Вероятнее всего традиционные технологии экстракции битумов горячей водой окажутся неприменимы для российских месторождений битуминозных песков из-за их физико-химических особенностей. Перспективным для России, вероятнее всего, будет использование процессов пиролиза или гидрогенизационной переработки без предварительного отделения битумов от битуминозных песков. Востребованными могут также оказаться скважинные методы извлечение битумов из битуминозных песков, с использованием интенсивных физико-химических методов, включая катализ в пластах. Широкое использование горючих сланцев откладывается, по-видимому, на более отдаленную перспективу в силу дороговизны их переработки и связанных с этим наличием серьезных экологических проблем.
Создание в России технологической платформы по расширению использования нетрадиционных углеводородных ресурсов возможно на основе интеграции крупных компаний (прежде всего нефтяных) и организаций научно-технической сферы. Необходимо создание полигонов по отработке новых технологий добычи нетрадиционного углеводородного сырья и его квалифицированной переработке в моторные топлива, водород, сырье для нефтехимии. Нетрадиционное углеводородное сырье может стать в перспективе одним из важнейших источников для водородной энергетики.
Статья подготовлена по результатам исследования, проводимого при финансовой поддержке России в лице Министерства науки и высшего образования в рамках научного проекта «Социально-экономическое развитие Азиатской России на основе синергии транспортной доступности, системных знаний о природно-ресурсном потенциале, расширяющегося пространства межрегиональных взаимодействий», Соглашение № 075-15-2020-804 от 02.10.2020 г. (грант № 13.1902.21.0016).