Олег Валерьевич ЖДАНЕЕВ
Руководитель дирекции технологий ТЭК ФГБУ «РЭА» Минэнерго России, к. ф.-м. н.
e-mail: Zhdaneev@rosenergo.gov.ru
Василий Сергеевич ЧУБОКСАРОВ
Директор проекта дирекции технологий ТЭК ФГБУ «РЭА» Минэнерго России
e-mail: chuboksarov@rosenergo.gov.ru
В статье рассматриваются технологии Индустрии 4.0 и их потенциальное влияние на мировой и российский топливно-энергетический комплекс (ТЭК). Проведен анализ глобальных технических инициатив и предложено внедрение индекса оценки технологического развития предприятий ТЭК России. Массовое внедрение цифровых технологий в российский ТЭК уже в среднесрочной (3–5 лет) перспективе позволит повысить эффективность извлечения углеводородов на 5–10 % и снизить капитальные и операционные затраты на 10–15 %, а также сократить количество несчастных случаев на более чем 30 %. Авторами разработана методика оценки индекса технологического развития, позволяющая оценить готовность к внедрению элементов Индустрии 4.0 в российских компаниях ТЭК.
Ключевые слова: ТЭК, Индустрия 4.0, цифровые технологии, цифровая трансформация.
Введение
Концепция четвертой промышленной революции (Индустрии 4.0) впервые была представлена в Ганновере в 2011 году [1], как прогнозируемое событие массового внедрения «киберфизических систем» (систем, связывающих цифровые инструменты с материальными объектами) в производство и обслуживание человеческих потребностей. Предполагается, что эти системы объединятся в одну сеть, будут связываться друг с другом в режиме реального времени, самонастраиваться и самостоятельно учиться новым моделям поведения. Такие сети смогут выстраивать производство с меньшим количеством ошибок, взаимодействовать с производимыми товарами и при необходимости адаптироваться под новые потребности производителей и потребителей. Предполагается, что все это будет происходить в полностью автономном режиме без участия человека.
Ежегодно компании
инвестируют порядка 1 трлн долларов на цифровую трансформацию.
Ожидается, что к 2025 году она позволит европейской промышленности генерировать до 250 млрд евро в год
По оценкам отраслевых экспертов, ежегодно компании по всему миру инвестируют порядка одного триллиона долларов США на цифровую трансформацию [2]. Ожидается, что к 2025 году она позволит европейской промышленности генерировать дополнительно до 250 миллиардов евро ежегодно [3].
Массовое внедрение цифровых технологий в российский ТЭК уже в среднесрочной (3–5 лет) перспективе позволит при необходимости нарастить добычу углеводородов на 100 миллионов тонн, создать более 50 тысяч высококвалифицированных рабочих мест и сократить количество несчастных случаев примерно на 30 %, а также повысить эффективность и производительность труда до 50 %.
Для эффективного внедрения технологий Индустрии 4.0 необходимо оценить текущее состояние – готовность отрасли и компаний для трансформации. Некоторые страны для данных целей ввели единую систему оценки состояния отрасли и предприятий. Авторами разработан и в данной статье представлен показатель для отраслей ТЭК России. Составляющие данного индикатора охватывают технологические аспекты, процесс и анализ организации (всего 16 показателей), что позволяет отразить ключевые стороны деятельности предприятий ТЭК и определить направления развития.
Государственные программы внедрения элементов Индустрии 4.0 в России и мире
Цифровая трансформация экономик – один из ключевых приоритетов во множестве стран мира. При этом данный инструмент используется для решения разных задач: от завоевания превосходства в области производственных систем до фундаментальных изменений в общественном сознании (таблица 1).
Таблица 1. Обзор мировых технологических инициатив
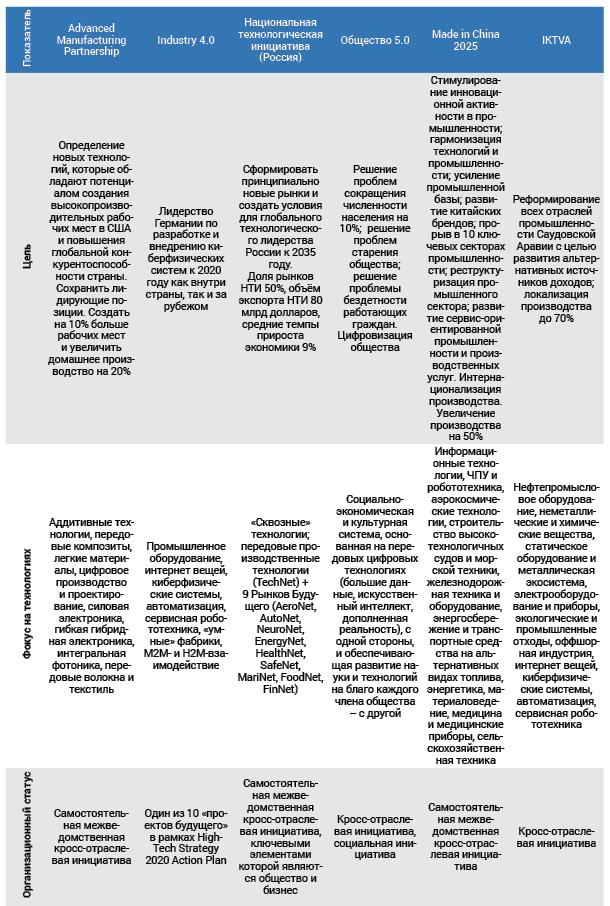
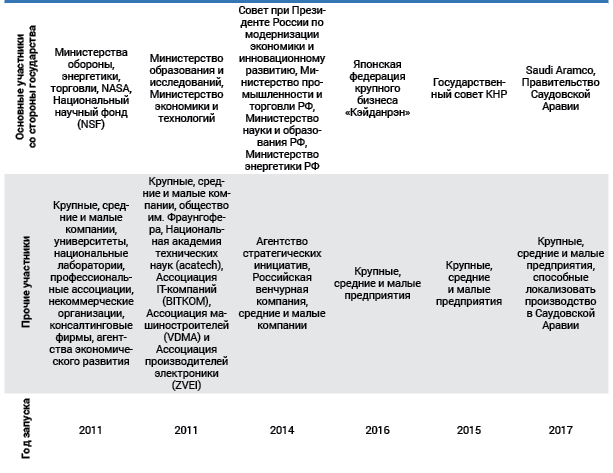
Цифровые технологии Индустрии 4.0
Ключевые технологии Индустрии 4.0 применимы ко всем отраслям ТЭК. Успешные примеры внедрения отдельных элементов продемонстрированы ведущими нефтегазовыми и нефтесервисными компаниями. Однако, существуют отдельные примеры, когда непродуманная трансформация в сжатые сроки с привлечением внешних инвестиций ставила под угрозу финансовое благополучие компании. Показателен пример компании General Electric, которая с 2015 года занималась цифровой трансформацией. GE в рамках реализации проекта Predix купила за 915 млн долларов облачный сервис управления сбором информации ServiceMax, а так же за 495 млн долларов компанию Meridium, специализировавшуюся на автоматизации обслуживания и повышении эффективности управления имеющимися ресурсами. General Electric планировала войти в рынок цифровых технологий и составить конкуренцию Amazon, Microsoft и Google, но уже в 2017 году пересмотрела стратегию из-за ее несостоятельности и больших финансовых потерь [4]. Стоит так же отметить, что, к сожалению, есть компании, сосредоточенные лишь на цифровизации существующих процессов, нежели на переосмыслении цепочки создания стоимости и выходу за счет цифровых технологий на новые горизонты.
С помощью цифровых технологий компаниям нефтегазовой, угольной и электроэнергетической отраслей возможно упростить и модернизировать комплексные процессы создания стоимости, снизить риски, удовлетворить индивидуальные потребности заказчиков, провести более быстрый и точный всесторонний анализ. Цифровизация полностью меняет саму парадигму планирования. Специалистам не придётся делать работу, которую их коллеги уже проделали в прошлом. А ведь ежегодно компании численностью в 1000 человек теряют в среднем 1 миллион долларов только из-за дублирования ранее проделанной работы. В масштабах глобальных корпораций эти значения вырастают в геометрической прогрессии.
По оценкам, внедрение цифровых технологий может дать следующий эффект для глобального ТЭК уже к 2025 году: [5]
- 2 триллиона долларов роста капитализации компаний;
- 200 миллиардов долларов, направленных на развитие общества;
- сокращение несчастных случаев в среднем на 9 %;
- сокращение разливов нефти более 500 тысяч баррелей;
- сокращение потерь нефти при добыче на 66 тысяч баррелей;
- 300 тысяч новых рабочих мест;
- сокращение выбросов CO2 на 200 миллионов тонн ежегодно.
Геологоразведка (нефть и газ)
Для трансформации основных рабочих процессов в геологоразведке, с целью снижения себестоимости и повышения эффективности работ, внедряется множество цифровых решений, например:
- используя компоненты робототехники и сенсорики, интеграции больших объёмов данных на стадии региональной геологоразведки, данных с высокотехнологических спутников и аэрофотоснимков с удалённо управляемых летательных аппаратов, специалисты смогут выявлять залежи полезных ископаемых в труднодоступных местах, где раньше геологические изыскания не проводились обычными методами;
- цифровой двойник сейсморазведочных работ – 30 % ускорение полевого этапа работ [6];
- на шельфе будущее за автономными необитаемыми аппаратами для проведения сейсморазведки, в том числе в тяжёлых ледовых условиях;
- когнитивные инструменты геологического анализа – 50 % сокращение времени камеральных работ [6];
- цифровой керн – кратное сокращение времени интерпретации, моделирование фильтрационных и физико-химических процессов [7];
- виртуальная лаборатория проведения экспериментов – 30 % оптимизация времени проведения исследований [8];
- использование технологий на основе больших данных, искусственного интеллекта и машинного обучения окажет значительное влияние на работы по составлению индивидуальных технических программ на строительство поисково-разведочных скважин. А именно до 80 % можно уменьшить время на интерпретацию и анализ геологоразведочных данных и создание технологических цифровых геологических моделей.
Программное обеспечение на основе структурирования данных и облачных технологий позволит инженерам по планированию бурения минимум в два раза быстрее обрабатывать геологические данные, полученные при сейсморазведке на выбранной территории, соотносить новые данные с историческими или с аналогичными по геологическому строению территориями, безошибочно выбирать интервалы отбора керна, основные параметры бурения, наиболее оптимальную траекторию скважин. В итоге, за счёт детального и всеобъемлющего машинного анализа большого объёма геологических данных, практическая информативность поисково-разведочных буровых работ достигнет 95–100 % [9].

Следующих результатов возможно будет достичь в геологоразведочной отрасли страны к 2030 году при планомерном внедрении цифровых технологий в существующие аналитические и производственные процессы:
- цифровые технологии будут внедрены в 70 % типовых видов ГРР;
- скорость принятия решения по результатам ГРР вырастет до 50 %;
- достоверность выводов по результатам ГРР и исходной информации в программах поисково-разведочного бурения вырастет до 30 %;
- геологическая изученность существующих лицензионных участков для проведения ГРР и планируемых участков для комплексных геофизических исследований на море и на суше вырастет не менее чем на 30 %.
Отдельно стоит выделить, что применение цифровых технологий на всех этапах геологоразведки значительно снижает риски – это ведет к росту максимальной ожидаемой стоимостной оценке проекта (EMV). Стоимостная оценка проекта рассчитывается с целью принятия решения по дальнейшим этапам работы, например, по поисковому или разведочному бурению, и в итоге напрямую влияет на количество открытий в новых и уже осваиваемых регионах.
В качестве успешного примера внедрения цифровых технологий в геологоразведке в России можно привести дизрапт-проект с применением передовых технологий машинного обучения «Газпром нефти» система «Когнитивный геолог». Она позволяет при минимальном наличии исходных данных определить с вероятностью более 90 % геологическую модель и выполнить подсчет запасов углеводородов в течение 2–3 дней. Ожидается, что система позволит в будущем сократить сроки геологоразведочных работ с трех лет до 6–12 месяцев [8].

Источник: worldoil.com
Бурение нефтяных и газовых скважин
Технологический процесс строительства разведочных и эксплуатационных скважин будет оптимизирован за счёт семи из девяти мировых приоритетных сквозных цифровых направлений развития. К ним относятся большие данные, искусственный интеллект, промышленный интернет вещей, компоненты робототехники, технология беспроводной связи, технологии виртуальной и дополненной реальности, новые производственные технологии. Только объединив их, компании смогут повысить эффективность бурения, внутрискважинных исследований и сервисных работ.
- Применение новых технологий и компонентов робототехники, заложенных в основу проектов наземного и скважинного бурового оборудования, повысит безопасность работ на скважине за счёт минимального применения ручного труда и исключения человеческого фактора. Они позволяют снизить время на бурение одной наклонно-направленной эксплуатационной скважины минимум на 17 % и скважины с горизонтальным окончанием в среднем минимум на 19 % от любых текущих средних показателей по месторождениям.
- Внедрение интернета вещей, цифровых двойников оборудования и системы предиктивной аналитики на основе машинного обучения на каждой буровой установке позволит исключить аварии на скважинах, сократить непроизводительное время из-за непредвиденных ремонтов оборудования с текущих фактических 15 % до 1 % от общего времени бурения.
- Адаптивная и автономная цифровая система управления процессом бурения, основанная на технологиях искусственного интеллекта, больших данных и скоростной беспроводной передачи данных, даст возможность одной инженерной команде одновременно управлять несколькими буровыми установками из центрального пункта управления на месторождении или из офиса, вести мониторинг состояния скважинного и наземного оборудования, своевременно предупреждать аварии и инциденты. Цифровая система в среднем снизит стоимость бурения скважины на 30 % и уменьшит срок строительства кустовой площадки из 20 скважин с горизонтальным окончанием в среднем с 24 месяцев до 13 месяцев.
- Итогом проникновения сквозных цифровых технологий станет создание полностью автоматизированного цифрового бурового комплекса – буровой установки 2.0. Современная классическая буровая установка как промышленный объект была создана в ходе второй и третьей промышленной революции.
В итоге цифровые технологии в бурении, при их полном внедрении, например, на отдельно взятом крупном месторождении в Западной или Восточной Сибири, разрабатываемом с нуля, дадут следующие безусловные результаты:
- снижение затрат на эксплуатационное бурение до 40 %;
- снижение капитальных затрат на разработку месторождения до 15 %;
- месторождение будет разбурено вдвое меньшим количеством буровых установок, вне зависимости от размера месторождения;
- средний срок основного периода буровых работ сократится с 8 лет до 4–5 лет;
- общее количество скважин уменьшится за счёт многоствольных скважин с увеличенными горизонтальными участками.
Потенциальное влияние цифровых технологий на блок добычи в России:
- снижение операционных затрат на обустройство и разработку месторождения до 15 %;
- снижение отказов скважинного насосного оборудования до 25 %;
- снижение трудозатрат на сбор информации о состоянии скважин до 50 %;
- возможность получения всех данных по скважине и наземному установкам на месторождении в режиме реального времени;
- сокращение несчастных случаев на производстве на 10 %;
- увеличение коэффициента извлечения нефти до 20 %.
Цифровизация в сферах бурения и добычи поможет при необходимости стабилизировать уровень добычи нефти в России в 550 млн тонн в год и 700 млрд кубометров газа в год.
В качестве примера проекта внедрения технологий Индустрии 4.0 в бурение можно привести разработку целой линейки программных продуктов ГК «Цифра» с целью сокращения срока строительства скважины за счёт увеличения скорости бурения по продуктивному пласту и почти полному исключению непроизводительного времени. При увеличении скорости проходки, комплекс специализированных программных продуктов позволяет достичь самой оптимальной траектории ствола скважины в пласте, что в итоге приводит к увеличению коэффициента извлечения нефти. Данные разработки могут стать основой для создания цифрового бурового комплекса (Буровая установка 2.0) с автономной и адаптивной системой принятия решений на основе цифровой интеграционной платформы [10].

Источник: «Уфагидромаш»
Другим успешным примером использования элементов Индустрии 4.0 в России является запуск «Роснефтью» проекта «Цифровое месторождение» в Башкирии в 2019 году. Компания при разработке широко применяла создание «цифровых двойников» отдельных элементов и всего комплекса в целом. Внедрение целого набора новых технологических решений на Илишевском месторождении позволило добиться существенного роста производственных показателей (ожидается, что в краткосрочной перспективе технология позволит получить дополнительно порядка 1 млн тонн нефти за счёт оптимизации производства). Количество дистанционно управляемых объектов увеличилось почти на 60 %, энергоэффективность процессов добычи повысилась на 5 %, на 5 % снизились логистические издержки [11].
Транспортировка углеводородов
Для трансформации основных процессов и операционных алгоритмов транспортировки нефти с целью снижения себестоимости и повышения эффективности работ внедряется также значительное количество цифровых решений:
- использование облака сенсоров (коррозии, сероводорода, хлорорганических соединений, воды, рН и т. д.), интеграция и обработка получаемых данных позволяют вести наблюдение за состоянием трубопроводной системы и качеством транспортируемой нефти в режиме реального времени;
- цифровой двойник трубопроводной системы позволит имитировать опытно-промышленные испытания без проведения дорогостоящих натурных испытаний;
- системы автоматизированного управления задвижками, интегрированные с поточными анализаторами нефти, позволят оперативно блокировать участки с загрязненной нефтью до ее смешения с чистой нефтью [12];
- роботизированные системы дефектоскопии позволят оперативно отслеживать участки, которые необходимо заменить [13];
- роботизированные сварочные комплексы дают возможность менять трубопроводы с минимальным отклонением качества сварочного шва от требуемого;
- системы мониторинга и слежения за несанкционированными врезками позволят минимизировать ущерб и оперативно предотвращать незаконные действия. Реализация данной системы снижает до нуля не только финансовый, но и экологический ущерб, который зачастую может приобретать катастрофические формы [14].

Источник: «Транснефть – Диаскан»
Следующих результатов возможно будет достичь в области транспортировки нефти к 2030 году при планомерном внедрении цифровых технологий в существующие аналитические и производственные процессы:
минимизация рисков аварий в результате «человеческого фактора»;
снижение отказов насосного оборудования до 25 %;
снижение потерь нефти за счет испарения до 0,3 %;
сокращение несчастных случаев на производстве до 10 %;
вывод в ремонт участков трубопровода, которые действительно нуждаются в нем, позволит экономить до 20 % средств на капитальные ремонты;
существенное снижение влияния отрасли на окружающую среду;
снижение рисков непрерывности ведения бизнеса.
В случае полного или частичного отсутствия процессов внедрения новых технологий в блоке транспортировки сложнее будет реализовывать проекты по освоению новых месторождений в Арктике и Восточной Сибири. Отдельно следует отметить, что в случае внедрения современных цифровых технологий возрастает коэффициент возврата инвестиций (ROI) в отрасль, что позволяет обеспечивать «гибкость» индустрии в целом [15].
Нефтепереработка
Технологические процессы в нефтепереработке являются многомерными и сложными, поэтому очень трудно определять наилучшие параметры функционирования установки, тем более целого завода в неавтоматическом режиме [16]. В настоящее время, управление параметрами установки зачастую производится технологом производства исходя из собственных знаний и опыта.
Повсеместное внедрение цифровых технологий и компонентов робототехники позволят добиться существенного повышения энергоэффективности и снижения затрат НПЗ.
- Оптимизация резервуарного парка. В настоящее время заводы вынуждены держать несколько резервуаров с промежуточными продуктами для того, чтобы с помощью компаундирования различных фракций получать сырье или топливо с заданными качественными характеристиками.
- Создание цифровых двойников установок и завода позволит имитировать условия использования новых катализаторов, специальных реагентов, оборудования. В настоящее время необходимо проводить дорогостоящие опытно-промышленные исследования (стоимость которых может достигать сотен миллионов рублей) для определения оптимальных параметров функционирования в условиях НПЗ.
- Использование предиктивной аналитики и анализа Big Data позволит выводить НПЗ в ремонт «по состоянию», то есть тогда, когда это действительно требуется, а не тогда, когда это предусмотрено регламентом. Подобный подход позволит увеличить межремонтные интервалы на 50–100 % и снизить время ремонта на 10–300 %.
- Цифровизация дает возможность рассчитывать тепловые и материальные балансы и оптимизировать их, что прямо повлияет на энергоэффективность предприятия.
- Внедрение поточных анализаторов помогает оперативно отслеживать физико-химические параметры сырья, промежуточных и готовых продуктов, с помощью интегрированной автоматизированной системы управления технологическими процессами можно оперативно менять технологические параметры установок для получения нефтепродуктов с заданными качественными характеристиками.
- Цифровые технологии увеличивают срок службы оборудования за счет сглаживания пиковых нагрузок на узлы и агрегаты.
- Они снижают количество дорогостоящих присадок для выправления качественных характеристик топлив.
- Виртуальная и дополненная реальность позволит производить обучение сотрудников НПЗ.
- Система датчиков оперативно определяет утечку газа и останавливает работу производства.
- Цифровизация производства снижает вред экологии на 20–50 %, в том числе за счет эффективного использования ресурсов.
- Новые технологии уменьшают затраты на строительный контроль на 60–70 %.
- Умные технологии снижают на 30 % нарушения требований к выполнению работ и повышают оперативность контроля на 100 %.

Источник: Iurii / Depositphotos.com
Ожидается, что в обозримом будущем НПЗ станут «цифровыми» или «умными», то есть перейдут к полностью автоматизированному производству, которое управляется интеллектуальными системами. Это сделает нефтепереработку более эффективной и безопасной, менее затратной и лучше управляемой. На данный момент такие технологии применяются на российских НПЗ фрагментарно, на отдельных стадиях или установках, но первые успешные испытания являются ключом к полной трансформации системы.
В 2018 году воронежская площадка «СИБУРа» завершила первый этап реализации проекта по внедрению «технического зрения» в процесс производства растворных каучуков. Оборудование позволило повысить эффективность процесса автоматической упаковки готовой продукции [17].
Добыча угля
Угольная отрасль на протяжении многих лет была и остается основой электроэнергетики многих стран. Сегодня перед отраслью стоят серьёзные вызовы. В первую очередь это все более и более жесткие экологические требования к производству, а также конкуренция со стороны других источников энергии. Для угольной отрасли внедрение технологий Индустрии 4.0 предоставляет шансы для изменения роли в глобальной экономической конкуренции.
- На стадии геологоразведки технологии виртуализации, дистанционного зондирования земли (спутниковая геодезия, лазерное сканирование), интерактивного планирования и проектирования позволят операторам точно определять наиболее перспективные для разработки участки и эффективно проводить доразведку действующих месторождений.
- Использование роботизированных фронтальных агрегатов, инновационных технологий физико-химических, гидравлических, электромагнитных способов разрушения горных пород позволит операторам повысить производительность труда в два раза.
- Автономные транспортные средства (большегрузы) и высокотехнологичное оборудование, оснащенные датчиками интернета вещей, передающих в режиме реального времени информацию со всех узлов, на 25 % снижают время простоя оборудования благодаря анализу данных и предсказанию времени отказа систем. Использование автономных роботов в шахтах уже сегодня сокращает количество несчастных случаев на 20 %.
- Логистика поставок с использованием систем интеграции с информационными системами клиентов кардинально меняется.
Примеры потенциального влияния цифровых технологий на блок добычи угля в России:
- увеличение добычи угля до 15 %;
- экономия до 900 миллиардов рублей в год (капитальные и операционные затраты в целом по отрасли в течение одного календарного года);
- уменьшение вреда экологии на 40 % за счет внедрения новых цифровых методов контроля аварий на производстве;
- сокращение несчастных случаев на производстве на 20 %.
В качестве успешного комплексного проекта по цифровой трансформации в России можно привести компанию «Евраз», которая благодаря внедрению дистанционного управления, машинного обучения, расширенной аналитики и сценарной оптимизации смогла не только увеличить выработку угля, но и снизить затраты [18].
Электроэнергетика
Массовое внедрение киберфизических систем в производство, передачу, сбыт и потребление электрической энергии происходит уже сейчас. Технологии четвертой промышленной революции, описываемые такими собирательными понятиями, как «блокчейн», интернет вещей, дополненная реальность, виртуальная реальность, большие данные, 3D‑печать, квантовые вычисления, беспилотные устройства (роботы) уже сегодня оказывают существенное влияние на производственные процессы, происходящие в Единой энергетической системе России, трансформируют ее [19].
К технологиям, которые сегодня развиваются в рамках концепции Индустрии 4.0 в электроэнергетике России, следует отнести:
- Интеллектуальные приборы учета, которые позволят в будущем реализовать концепцию управления спросом. «Умные счетчики» дают возможность экономить не только энергоснабжающим компаниям (ввиду отсутствия затрат на проверку показаний счетчиков и получения данных в режиме реального времени), но и потребителям – за счет управления профилем потребления и различными энергозатратными устройствами.
- Дроны / роботы / роботизированная диагностика инфраструктуры. Беспилотные летательные аппараты (дроны) могут проводить проверку исправности инфраструктуры, быстрее и эффективнее находить обрывы линий электропередач, следить за растительностью в местах прокладки линий электропередачи и своевременно информировать обслуживающий персонал о необходимости вырубки, доставлять мелкие запасные части в места проведения аварийных работ.
- Активный энергокомплекс (в том числе виртуальная энергосистема) – система, в которой все субъекты электроэнергетического рынка (генерация, сети, потребители) принимают активное участие в процессах передачи и распределения электроэнергии. В составе такого комплекса электрическая сеть из пассивного устройства транспорта и распределения электроэнергии превращается в активный элемент, параметры и характеристики которой изменяются в зависимости от режима работы энергосистемы [20].
- Исследования показывают, что внедрение систем инфраструктуры интеллектуального учета (AMI) позволяет снизить потребление электроэнергии на 11–17 %. [21]
- Мониторинг работы производственных активов, в том числе протяженных (AR, VR, дроны). Применение в работе беспилотников значительно ускоряет осмотры линий электропередачи и поиск повреждений на них. Бригаде может понадобиться около 2 часов, чтобы пройти 5 километров вдоль ЛЭП на сложном рельефе, заболоченной и пересеченной местности. С беспилотника найти и сфотографировать оборванный провод, упавшую опору или поврежденный изолятор можно за считанные минуты. Если скорость передвижения бригады около 3 км/ч, то квадрокоптер может развивать более 50 км/ч [22].
- Предиктивное техническое обслуживание энергетических объектов экономит на техническом обслуживании до 10 %-40 %, сокращает простой оборудования до 50 %, увеличивает срок службы оборудования до 3–5 % и снижает затраты на замену на 3–5 % [23].
- Прогнозирование производства энергии. Данные решения позволяют существенно упростить интеграцию ВИЭ в сеть.
Внедрение технологий Индустрии 4.0 в электроэнергетике позволит:
- снизить продолжительность перерывов электроснабжения и средней частоты технологических нарушений (SAIDI / SAIFI) на 5 %;
- принимать более обоснованные решения, используя прогнозную аналитику и машинное обучение;
- вести более экономичную и производительную деятельность;
- повысить гибкость и коэффициент использования активов через интегрированную систему управления производством в режиме реального времени.
Цифровизация электроэнергетики – задача важная и сложная. Она требует системного целевого видения на уровне всей отрасли. Ключевыми результатами реализации перехода к цифровым технологиям должно стать повышение эффективности генерирующих и электросетевых компаний, дополнительное снижение сроков технологического присоединения к электрическим сетям, повышение уровня технического состояния производственных фондов электроэнергетики и рост надежности электроснабжения потребителей.
В качестве успешного кросс-отраслевого проекта внедрения цифровых технологий можно привести проект 2018 года, когда на линейной производственно-диспетчерской станции «Уват» «Транснефть-Сибири» было завершено строительство первой российской цифровой подстанции. В проекте были опробованы технические решения, разработанные специалистами «НИИ Транснефть», с использованием цифровых измерительных трансформаторов и централизованных устройств релейной защиты и управления электрической подстанцией, а также первой в России цифровой системой коммерческого учета электроэнергии [24].
Индекс оценки технологического развитий предприятий ТЭК
Для отраслей российского ТЭК предлагается ввести индекс технологического развития, в основу которого лег синтез индексов Smart Industry Readiness Index («SIRI») и «Industry 4.0 Readiness index».
Индекс состоит из 3 основных групп Индустрии 4.0: технология, процесс и организация. Все 3 группы должны использовать весь потенциал Индустрии 4.0. В основе 3 групп лежат 8 ключевых подгрупп, на которых компании должны сосредоточиться, чтобы стать готовыми к будущему. Наконец, 3 группы и 8 подгрупп делятся на 16 метрик, которые являются областями оценки. Компании могут использовать их для оценки текущей готовности своих объектов в соответствии с требованиями Индустрии 4.0. Индекс рассчитывается как среднее из метрик, подгрупп и групп.

Принципы оценки:
- Индекс фиксирует текущее состояние объекта исследования, а не его потенциал в будущем.
- Индекс использует концепции Индустрии 4.0 в качестве ориентира. Будущие производственные и промышленные концепции и технологии также должны быть приняты во внимание, если это необходимо.
- Размеры объектов исследования должны быть приняты во внимание. Важность и актуальность каждого компонента и измерения будут варьироваться в зависимости от текущих и будущих потребностей компании.
- Внимание не должно быть сосредоточено на достижении диапазона 5 во всех измерениях. Вместо этого компании должны стремиться к более широкому диапазону, основанному на их специфических бизнес-потребностях и стремлениях.
- Индекс следует использовать на постоянной основе, а не для разовой оценки.
Заключение
Большинство цифровых решений, имеющихся в настоящее время на рынке, нацелены на снижение операционных расходов отрасли, которые в 2018 году в целом по России составили около 650 миллиардов рублей [25]. Внедрение цифровых технологий Индустрии 4.0 помогает сократить до 35 % операционных расходов в ТЭК. Даже 1 % прироста производительности капитала за счет внедрения цифровых технологий Индустрии 4.0 может означать экономию около 260 миллиардов рублей. При этом сами технологии дешевеют из года в год из-за более массового применения. Например, дроны в 2007 году стоили около 6,5 миллионов рублей, а сегодня – уже в районе 50 тысяч рублей.
Существует целый ряд страновых преимуществ для создания отечественных цифровых технологий:
- высокий уровень образованности населения (15 место в мире по данным ООН), включая STEM направления;
- большое количество научных институтов и предприятий (более 1000);
- конкурентоспособная стоимость труда;
- современная инфраструктура технологических парков (12 технопарков с современным оборудованием);
- административная и финансовая поддержка государства (в 2019 г. было выделено более 1 трлн рублей на развитие науки).
В России существуют компании, способные производить цифровые технологии на уровне лучших зарубежных образцов и все условия для создания большего количества таких компаний. Доверие к российским производителям технологий Индустрии 4.0 со стороны ТЭК и централизованная поддержка государства – одни из главных драйверов развития цифровой индустрии в России [26].
Среди рисков внедрения цифровых технологий в российском ТЭК можно выделить:
- динамика цифровизации, помимо требований компании и ее финансовых возможностей, должна отвечать развитию цифровых технологий в целом;
- недоверие сотрудников из-за опасений за рабочие места;
- ограничения на обмен опытом и данными между разработчиками технологий из разных стран из-за геополитической ситуации;
- определенный уровень недоверия руководства организаций по причине недостаточности успешных примеров внедрения решений;
- настороженность компаний при принятии решений по инвестициям в проекты, выгоду от которых сложно рассчитать на первоначальном этапе ввиду отсутствия статистических данных.
Примеры ожидаемых эффектов от внедрения технологий Индустрии 4.0 приведены в таблице 2.
Таблица 2. Примеры возможных эффектов
от внедрения цифровых технологий в Российский ТЭК в среднесрочной перспективе (3–5 лет)
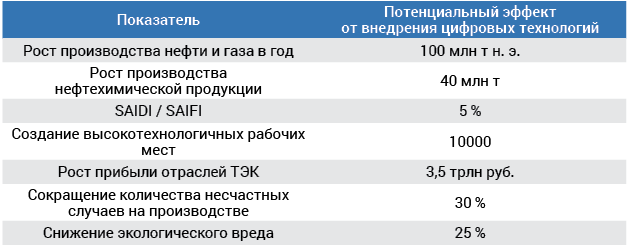