Олег НОВИКОВ
Генеральный директор
АО НПФ «УРАН-СПб», к. т. н.
Е-mail: onnovikov1941@mail.ru
Игорь АНАНЧЕНКО
Ведущий научный сотрудник
АО НПФ «УРАН-СПб», к. т. н.
Е-mail: anantchenko@yandex.ru
Никадим МИНЧЕВ
Заведующий лабораторией
метрологии АО НПФ «УРАН-СПб»
Е-mail: minivik@mail.ru
Специалисты по энергетике, экономике, автоматизации, приборостроению, метрологии, экологии и др., связанные со сжиганием разнообразных видов топлива в различных теплоэнергетических агрегатах (котлах, печах, сушилах и др.) пользуются терминами: «энергетическая эффективность», «энергосбережение», «качество и экономичность горения», «оптимальность использования топлива» и др. Вся эта терминология описывается общим понятием «энергоэкологическая оптимизация сжигания топлива», которая предусматривает инструментальный контроль процессов и внедрение прогрессивных технических решений [1, 2], для повышения экономической эффективности использования топлива и для снижения вредного воздействия продуктов сгорания на окружающую среду.
Для оценки экономической эффективности, технического уровня и качества эксплуатации теплоэнергетических агрегатов (на примере котлоагрегатов) служит система энергетических, экономических и режимных показателей [3].
1. Энергетические показатели, связанные с технологией сжигания топлива, характеризуют степень использования тепла топлива или тепла другого источника – тепловую экономичность различных агрегатов. Энергетические показатели: коэффициенты полезного действия (КПД) брутто

и нетто

любых устройств, сжигающих топливо; доля расхода тепла на собственные нужды

коэффициент теплового потока

удельный расход топлива на отпущенную тепловую энергию

коэффициент избытка воздуха, расходуемого на горение

и др.
2. К системе экономических показателей, которыми пользуются обычно экономисты при проектировании топливосжигающих установок, относятся: суммарные (K) и удельные капитальные вложения (k); ежегодные издержки производства (ΣS); себестоимость единицы продукции (тепловой энергии Sт); приведенные затраты (З).
Режимные показатели, не связанные напрямую с технологией сжигания топлива, характеризуют степень использования оборудования, условия работы топливосжигающих установок. К ним относятся показатели: коэффициенты рабочего времени (kг), средней нагрузки (kср), использования максимума нагрузки (kм), использования установленной мощности (kуст); годовое число часов использования установленной мощности (hгод) и максимума тепловой нагрузки (hо).
Большая часть показателей используется при проектировании и режимно-наладочных испытаниях агрегатов для периодических технико-экономических расчетов по известным формулам с помощью электронных калькуляторов или компьютеров. Другая часть показателей, в основном энергетических, которая интересует авторов данной статьи, используется непрерывно автоматическими устройствами для отображения результатов работы теплоэнергетического оборудования и корректирующего регулирования, с целью повышения эффективности.
Исходные величины для расчетов показателей эффективности работы в основном поступают от штатных контрольно-измерительных приборов (КИП) агрегатов и дополнительно от специальных, стационарных или переносных теплотехнических (газоаналитических) приборов в процессе эксплуатации или режимно-наладочных испытаний.
Для определения энергетической экономичности различных теплоагрегатов (например, котлов) в отечественной и зарубежной практике имеются различные стандарты [4, 5], которые устанавливают нормативные методы расчета (формулы), проведения испытаний, измерений и наилучшие доступные технологии (НДТ) сжигания топлива в технологическом оборудовании в стационарных режимах.
Важным показателем, характеризующим экономичность работы котлоагрегата, является коэффициент полезного действия брутто, который определяется прямым или обратным методом из уравнения теплового баланса по формулам:
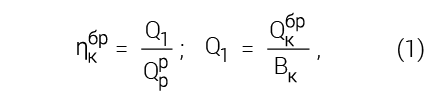
где

полезно использованное тепло котлоагрегатом;

– располагаемое тепло, содержащееся в расходуемом топливе, с учетом физического тепла, внесенного воздухом и топливом при горении;

– выработанное тепло и – расход топлива котлоагрегатом.
Прямой метод определения КПД брутто является сложным и трудоемким, так как сопряжен с использованием большого количества параметров, измеренных с высокой точностью. Он применяется для камеральных расчетов при проектировании теплоэнергетических установок и их испытаниях. Результаты расчетов этим методом можно использовать как «эталонные».
Обратный метод определения КПД брутто котлоагрегатов является предпочтительным. Он пригоден для оперативного использования при эксплуатации существующего оборудования и заключается в определении величин всех потерь теплового баланса по формуле:
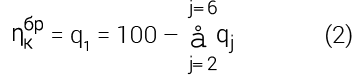
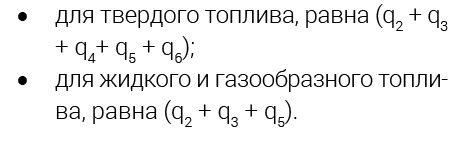
В свою очередь, каждый вид потерь определяется уравнениями.
1. Потери тепла с уходящими дымовыми газами
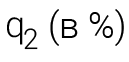
– по формулам:
По «классической» формуле [4]:
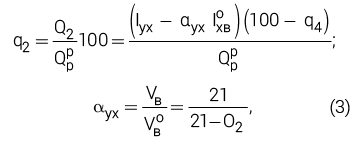
где

– удельная энтальпия уходящих газов при коэффициенте

температуре

и полном сгорании топлива;

– удельная энтальпия теоретически необходимого количества холодного воздуха на входе в котел;

– коэффициент избытка воздуха;

– фактический объем воздуха, расходуемый на горение;

– теоретически необходимый объем воздуха для стехиометрического горения;

– измеренная концентрация кислорода в уходящих газах в об. %.
По упрощенной формуле М. Б. Равича [6]:
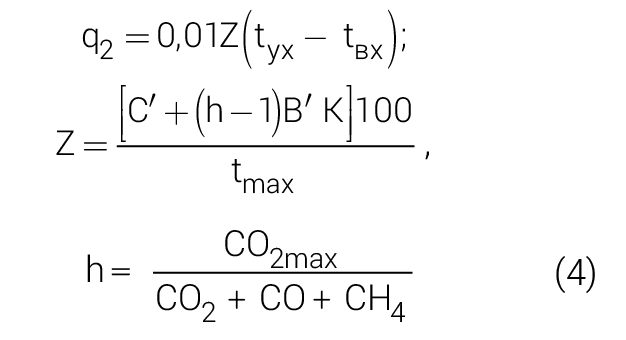
где

– температура уходящих дымовых газов;

– температура воздуха, поступающего в топку;

– жаропроизводительность топлива из таблиц;
h
– коэффициент разбавления дымовых газов воздухом;

– наибольшая концентрация диоксида углерода в дымовых газах при полном сжигании топлива из таблиц;
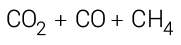

– сумма углеродсодержащих газов;

– усредненная характеристика топлива и С;
К
– поправочные коэффициенты, зависящие от температуры дымовых газов из таблиц.
По упрощенной формуле Siegert (Зигерта) в стандарте DIN [7]:
или
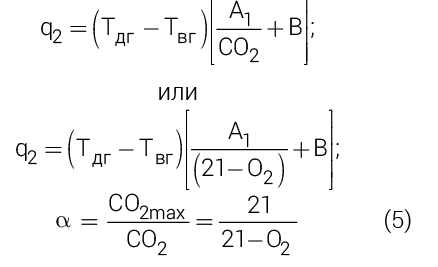
где

– измеренная температура дымовых газов и воздуха, подаваемого на горение (в °C);

– измеренная или рассчитанная концентрация диоксида углерода в дымовых газах (в об. %);

– измеренная концентрация кислорода в сухих дымовых газах (в об. %);

– наибольшая концентрация диоксида углерода в дымовых газах при полном сжигании топлива из таблицы 1 (в об. %);

– коэффициент избытка воздуха;

– эмпирические коэффициенты, зависящие от вида сжигаемого топлива из таблицы 1.
Потери тепла от химической неполноты сгорания топлива (в %):
По «классической» формуле:
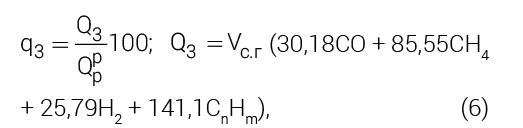
где

– объем сухих дымовых газов при 0 °C и 0,1 МПа в месте отбора на анализ;
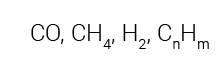
– содержание продуктов неполного сгорания топлива в дымовых газах.
По упрощенной формуле М. Б. Равича:
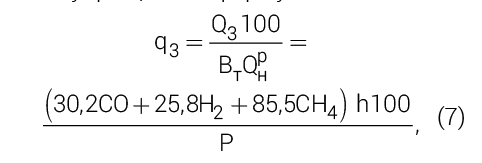
где P – максимальное теплосодержание сухих продуктов сгорания данного вида топлива (практически постоянная – обобщенная константа) из таблиц.
По упрощенной формуле Зигерта:
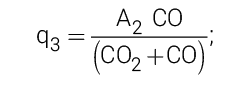
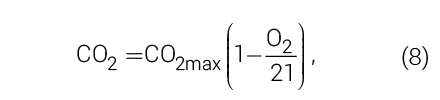
где CO – измеренная концентрация оксида углерода в дымовых газах (в об. %);

– измеренная или рассчитанная концентрация диоксида углерода в дымовых газах (в об. %);

– эмпирический коэффициент, зависящий от вида сжигаемого топлива из таблицы 1.

3. Потери тепла от механической неполноты сгорания топлива определяются наличием недогоревшего топлива в шлаке или золе (), выпадающей в газоходе и бункере (в %):
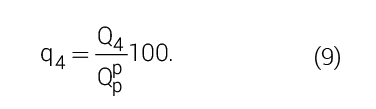
4. Потери тепла на излучение и конвекцию в окружающую среду (в %) включают теплоту, отдаваемую обмуровкой и другими частями котла окружающему воздуху. Они вычисляются нормативным методом по измеренным температуре поверхности котла и окружающего воздуха с использованием принятых коэффициентов теплоотдачи. Либо упрощенно, согласно нормативным табличным данным для номинальной нагрузки

и с учетом фактической нагрузки котла

отличающейся от номинальной

по формуле (в %):
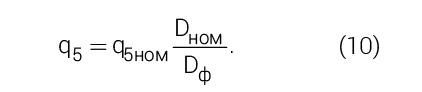
Потери тепла в шлаке или золе при слоевом и камерном сжигании твердого топлива определяются температурой шлака, удельной теплоемкостью и рассчитываются по формуле (в %):
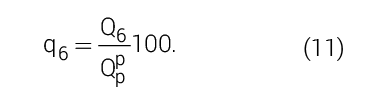
Анализ приведенных формул для расчета КПД брутто любого топливосжигающего агрегата по методу обратного баланса позволяет сделать выводы:
Нормативный (классический) метод расчета не применим для цели оперативного контроля и регулирования процессов сжигания топлива, так как требует громоздких вычислений удельных объемов, энтальпий продуктов сгорания и др., а также измерений калорийности топлива, химического состава дымовых газов и их расходов. Его можно использовать как проверочный для оценки точности других методов.
Для оперативного контроля и регулирования процессов сжигания топлива рационально использовать упрощенные, но достаточно точные (невязка составляет 0,2–1,5%) методы расчета по Равичу, Зигерту и др. При этом для вычислений требуется меньшее количество исходных данных и их легко получить: из таблиц; от штатных КИП агрегатов; от специальных стационарных или переносных газоаналитических приборов. Кроме этого, данные формулы проще «поместить» в микропроцессоры измерительных приборов и вычисления по ним не потребуют большого быстродействия и объема памяти.
Другим важным параметром, существенно влияющим на показатели экономичности и качества работы котлоагрегата, является количество воздуха, поступающее в топку для горения, вернее, соотношение «топливо – воздух», которое определяется коэффициентом избытка воздуха ().
В топливосжигающих агрегатах должно быть точно сбалансировано соотношение «топливо – воздух». Недостаток воздуха вызывает неполное сгорание топлива, появление «недожога» (преимущественно СО), уменьшение температуры дымовых газов и снижение КПД. Избыток воздуха приводит к появлению лишнего кислорода (О2) в дымовых газах, повышению их температуры и также к снижению КПД. В обоих случаях сжигание топлива сопровождается повышенным выбросом в атмосферу высокотоксичных газов СО и NOX, т. е. ухудшается экологическая обстановка.
Из приведенных кривых видно, что с уменьшением коэффициента α (альфа) избытка воздуха снижаются содержание кислорода (О2), температура дымовых газов и потребление электроэнергии вентилятором и дымососом и, как следствие, повышается КПД котла.
Котельные агрегаты, из-за отсутствия газового контроля отходящих дымовых газов и наличия значительных присосов в топке и газоходах, а также в результате применения наладчиками режимных карт (К), работают при необоснованно больших избытках воздуха (Ф). Поэтому уменьшение коэффициента избытка воздуха является эффективным методом снижения потерь теплоты с уходящими газами и подавления оксидов азота (NOx). Это достигается только регулированием, при этом не удорожается технологическое оборудование и не меняется конструкция горелочных устройств.
Появление СО определяет границу допустимого воздействия в сторону уменьшения избытка воздуха. Эта граница является гибкой и зависит:
- от характеристик горелочных устройств;
- от нагрузки котла;
- состава топлива (теплоты его сгорания);
- климатических условий;
- температуры топлива и воздуха;
- технического состояния оборудования и др.
Область экономически выгодного (оптимального) режима сжигания топлива (зона А), соответствующая малым значениям кислорода (0,5–1,5%) и содержанию оксида углерода на уровне 100–300 ppm, выделена на рис. 1 штриховкой. Она может быть обеспечена только автоматической коррекцией работы горелочных устройств.
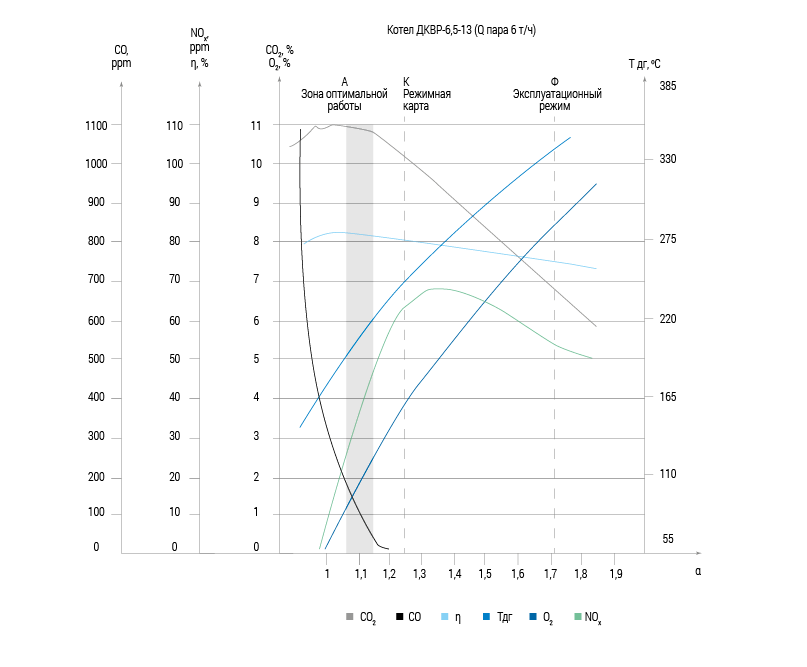
Для реализации этих принципов существующие и вновь проектируемые котельные агрегаты требуют оснащения надежным оборудованием, таким как:
- стационарные анализаторы дымовых газов;
- быстродействующие микропроцессорные регуляторы;
- интеллектуальные вычислительно-регистрирующие приборы.
Для создания АСУ-ТП и обмена информацией с другими приборами их следует соединить интерфейсом с управляющим контроллером котла [8]. Разнообразные переносные газоанализаторы, способные рассчитывать параметры горения, с которыми работают наладчики во время режимных испытаний агрегатов (повторяются через 3 года), не решают существующей проблемы. Так как эти приборы, содержащие датчики газов с жидкими электролитами, которые быстро расходуются, по надежности рассчитаны на кратковременную работу и не могут быть адаптированы в системы автоматического регулирования.
Для этой цели подходят газоаналитические приборы и автоматические системы энергосбережения, разработанные, изготавливаемые и внедряемые в течение 25 лет НПФ «УРАН-СПб», которая решает проблемы экономного сжигания топлива в теплоэнергетике [9, 10].
Для контроля экономичности, качества сжигания топлива и для управления этим процессом специально разработано в 2011 г. и серийно выпускается с 2016 г. семейство стационарных комбинированных автоматических анализаторов дымовых газов непрерывного действия, внесенное в государственный реестр средств измерений № 87382-22 [11].
В список входят такие модели приборов, как:
- многокомпонентный анализатор дымовых газов – КАДГ.
- интеллектуальный анализатор качества горения топлива – ИАКГ.
- корректор-анализатор качества горения топлива – КАКГ.
- отдельный вычислитель эффективности «Факел-К» с ЖК монитором.
- Комбинированные анализаторы дымовых газов предназначены для:
- измерения концентрации кислорода, оксида углерода и оксидов азота в отходящих газах топливосжигающих установок;
- измерения температуры дымовых газов и воздуха на горение;
- измерения избыточного давления/разрежения дымовых газов или (в моделях КАКГ) давление воздуха на горение;
- а также определения расчетным методом (в моделях ИАКГ, КАКГ) содержания диоксида углерода (СО2) и эффективности горения топлива (КПД), определения расчетным методом по ПИД-закону (в модели КАКГ) величины скорректированного давления воздуха или коэффициента коррекции с целью оптимизации процессов горения.
Анализаторы имеют встроенное программное обеспечение (ПО), разработанное специально для решения задач измерения содержания определяемых компонентов, температуры и давления анализируемой среды, а также вычисления параметров, характеризующих эффективность топливосжигающих установок. Функциональная схема вычислительного устройства для моделей ИАКГ, КАКГ приведена на рис. 2.
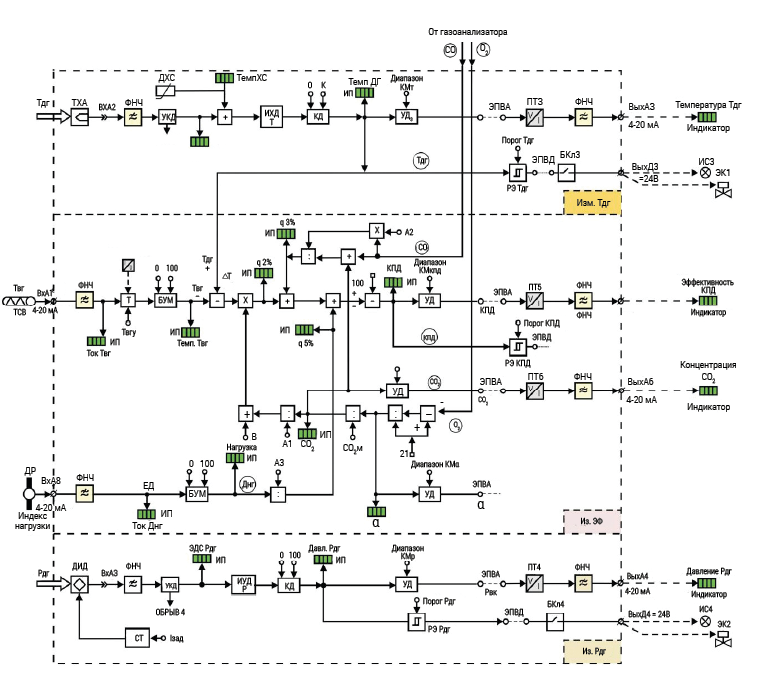
Все приборы унифицированы и выполнены на единой конструктивной платформе, изготавливаются в четырех модификациях (Н), (П), (Т), (Ех) с разной длиной погружной части и применяются в различных условиях окружающей (таблица 2)

и анализируемой (таблица 3) сред, соответственно, нормальной, запыленной, высокотемпературной и взрывоопасной. Способ отбора пробы газа диффузионный или принудительный с использованием встроенного эжектора или воздушного компрессора.

Анализаторы выполнены в виде измерительных и вычислительно-индицирующих блоков, соединенных или разобщенных между собой, которые монтируются непосредственно на стенке дымохода у точки отбора пробы и перед оператором.
В анализаторах использованы надежные и долговечные датчики по измерительным каналам:
- концентрации кислорода, оксида углерода и оксидов азота – электрохимические на твердых электролитах;
- температуры – термоэлектрические и терморезистивные;
- избыточного давления/разрежения – пьезорезистивные.
Предлагаемые НПФ «УРАН-СПБ» газоаналитические приборы, системы коррекции соотношения «топливо – воздух» и комплексные системы автоматизации котлоагрегатов с функцией энергосбережения позволяют:
- реализовать общую концепцию энергосберегающей работы котлоагрегатов в непрерывном режиме;
- экономить до 6–10% топлива в течение года;
- сократить на 30–40% выбросы оксидов азота в атмосферу;
- уменьшить на 20–55% потребление электроэнергии вентиляторами и дымососами;
- повысить надежность работы теплотехнического и механического оборудования за счет диагностики и контроля работы газовоздушных трактов, датчиков, исполнительных механизмов и др.