Александр ИШКОВ
Заместитель начальника департамента – начальник управления ПАО «Газпром», профессор кафедры ЮНЕСКО «Зеленая химия для устойчивого развития» Российского химико-технологического университета им. Д. И. Менделеева, д. х. н.
Николай НЕСТЕРОВ
Начальник Управления ПАО «Газпром», ученый секретарь научно-технического совета ПАО «Газпром», к. т. н.
Константин РОМАНОВ
Начальник отдела ПАО «Газпром», генеральный директор ООО «Газпром водород», ответственный секретарь координационного комитета ПАО «Газпром» по вопросам рационального природопользования, к. э. н.
Евгений КОЛОШКИН
Главный технолог ПАО «Газпром», ученый секретарь секции №19 научно-технического совета ПАО «Газпром»
Сергей НАСТИЧ
Главный научный сотрудник лаборатории исследований материалов Корпоративного научно-технического центра развития трубной продукции ООО «Газпром ВНИИГАЗ», д. т. н.
Владимир ЕГОРОВ
Начальник Корпоративного научно-технического центра развития трубной продукции ООО «Газпром ВНИИГАЗ»
Вячеслав ЛОПАТКИН
Начальник лаборатории исследований материалов Корпоративного научно-технического центра развития трубной продукции ООО «Газпром ВНИИГАЗ»
Введение
Развитие водородной энергетики требует обеспечения надежной и безопасной транспортировки водорода в больших объемах на значительные расстояния. Одним из возможных вариантов является трубопроводная транспортировка газообразного водорода, на ее развитие прогнозируется основная доля инвестиций в инфраструктуре [2]. Экспертами рассматриваются вопросы развития трубопроводной транспортировки водорода как путем создания специализированных трубопроводов, так и переназначения существующих магистральных газопроводов (МГ), предназначенных для природного газа [4, 5, 6, 7]. В публикациях [8,9] проведена оценка аспектов транспортировки и использования метановодородных смесей (МВС), по существующей газотранспортной инфраструктуре (ГТС) для природного газа. Наряду с этим используются и другие способы транспортировки и хранения водорода в разном агрегатном состоянии [1]. В последнее время водород используется в основном в качестве сырья для химической и нефтехимической промышленности (производство аммиака и метанола).
Водород имеет ряд особенностей, обусловленных малым размером атома и молекулы: малую плотность, большую летучесть, высокую растворимость и диффузионную подвижность в металлах и пластиках. Энергетические характеристики водорода (теплотворная способность CV (QН) и число Воббе W) отличны от природного газа, поэтому изменяются режимы работы энергетического оборудования [8, 9]. Теплота сгорания водорода больше, чем у метана, но плотность практически на порядок меньше, поэтому для получения такого же количества энергии в случае водорода должна обеспечиваться повышенная степень сжатия. При внедрении в конструкционные стали при относительно невысоких температурах (до 180–200оС) атомарный водород вызывает водородное охрупчивание (ВО) металла, в результате чего происходит деградация механических свойств, в особенности пластичности и сопротивляемости развитию трещины (трещиностойкости) [10, 11].
При развитии водородных проектов специфические физико-химические особенности водорода как транспортируемой среды оказывают существенное влияние на работоспособность, режим работы и надежность трубопроводов и оборудования. Статья посвящена рассмотрению технических, логистических и экономических рисков трубопроводной транспортировки водорода с использованием элементов сложившейся инфраструктуры для природного газа.
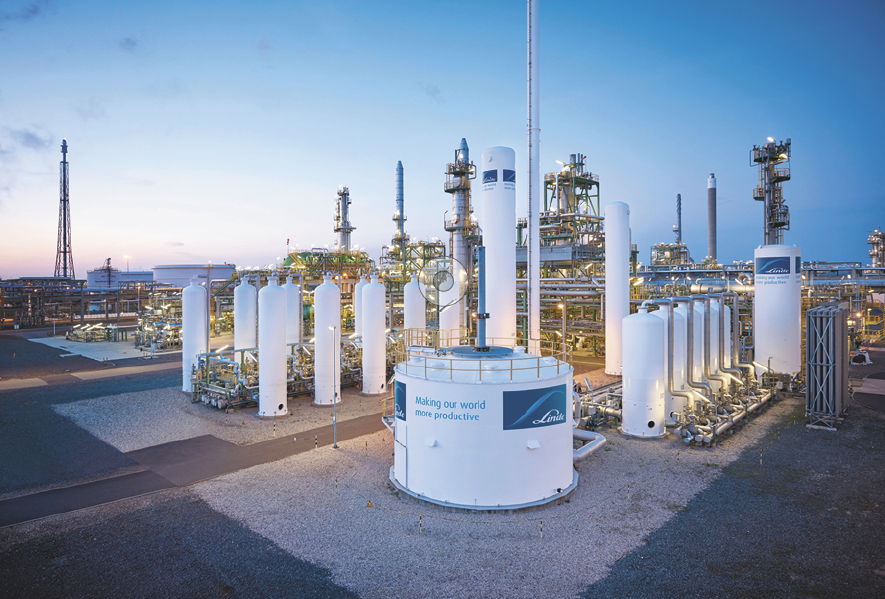
Источник: linde-engineering.com
Варианты транспортировки газообразного водорода по трубопроводам
В зависимости от расстояния изменяются параметры трубопроводной системы, главными из которых являются рабочее давление и диаметр трубы, что определяет пропускную способность. Эффективность транспортировки водорода на расстояние до 2–2,5 тыс. км обеспечивается при работе на 75% от проектной мощности: для трубопровода диметром 508 мм (20“) при пропускной способности на уровне примерно 100 тыс. т в год, а для трубопровода диаметром 1219 мм (48”) – примерно 2000 тыс. т в год [4]. При увеличении рабочего давления и диаметра трубы значительно возрастают окружные напряжения в металле, поэтому для обеспечения надежности приходится увеличивать прочность стали или толщину стенки трубы.
Допустимое содержание водорода в транспортируемом природном газе в России не нормируется (ГОСТ 5542-2022), а в странах Европы ограничено 2% (2023 г., вместо 5% ранее), но «обычное» содержание водорода оценивается как 400–1,000 ppm (0,04–0,1% об.) [4].
Логистика трубопроводной транспортировки водорода в больших объемах основывается на трех основных подходах [2, 7, 8, 9, 12]. Возможные варианты для выбора варианта трубопроводной транспортировки водорода представлены в [2].
По первому варианту планируется строительство специализированных трубопроводов для водорода, подобных промышленным водородопроводам, но с более высокими эксплуатационными параметрами. В перспективе новые протяженные трубопроводы должны иметь диаметр 1219 мм (48”) для высокой производительности [4], но при этом усиливается склонность металла труб к ВО.
Второй вариант состоит в переназначении существующих участков ГТС или отдельных МГ на транспортировку водорода. Узким местом этого подхода является не только склонность металла труб к ВО, а также изменение компрессоров и режима их работы. Предполагается, что существующие трубопроводы сохраняются кроме отдельных участков или труб (по результатам инспекции), но компрессоры в обязательном порядке заменяются. При переназначении требуется всесторонняя инспекция технического состояния системы. Однако при переназначении МГ на транспортировку водорода экономическая эффективность МГ улучается при уменьшении производительности из-за снижения затрат на менее мощные компрессоры [5].
По третьему варианту, водород подмешивается к транспортируемому природному газу в небольшой концентрации (обычно рассматривается до 20%) в существующем или модернизированном МГ для получения МВС. В конечном пункте либо водород извлекается из газа (известно несколько технологий), либо МВС используется непосредственно в качестве топлива для энергетического оборудования [8, 9]. Этот вариант предлагают для использования водорода, производимого возобновляемыми источниками энергии (ВИЭ) посредством электролиза в периоды спада потребления электроэнергии. Даже при малых концентрациях водорода в МВС может проявляться эффект ВО металла труб, требоваться корректировка режима работы компрессоров или их замена, смесь имеет пониженную энергоемкость. Однако технологии экстракции водорода из МВС в больших объемах до сих пор не доступна (по данным Global Hydrogen Review 2023) [4]. Вместе с тем имеется опыт китайской компании CNPC транспортировки МВС с концентрацией водорода 24% по МГ длиной 397 км в течение 100 дней (апрель 2023 г.) [4].
Примером проекта глобальной системы водородных трубопроводов с использованием элементов существующей ГТС является «Европейский водородный каркас» (European Hydrogen Backbone), по которому планируется к 2040 г. создание сети трубопроводов для водорода протяженностью около 53 тыс. км, из которых 60% составят переназначенные для водорода МГ, а 40% – новые специализированные водородопроводы [2, 6].
Стоимость реализации вариантов трубопроводной транспортировки водорода определяется большим количеством влияющих факторов. Затраты на создание линейной части трубопроводов (CAPEX) для водорода в случае перепрофилирования существующих газопроводов оцениваются ниже, по сравнению со строительством специализированных трубопроводов на величину от 50 до 80% (для труб диаметром 1200 мм при давлении 8 МПа и 500 мм при давлении 5 МПа, соответственно) [5]. Схожие данные по снижению стоимости трубопроводов до 60% в случае переназначения для труб разных диаметров (от 500 до 1400 мм) получены в [7].
Проблема развития трубопроводной транспортировки водорода заключается в неопределенности рынков сбыта водорода в больших объемах [1]. Для вариантов с переназначением МГ и подмешиванием водорода проблемой является нахождение баланса между ограничением прибыли из-за уменьшения поставок энергии и увеличения затрат на техническую инспекцию с одной стороны, и значительными капитальными затратами на модернизацию или замену труб и обязательную замену компрессоров с другой стороны [9].
Технические проблемы и риски трубопроводной транспортировки водорода
Технические параметры МГ для природного газа, такие как рабочее давление, диаметр трубы и класс прочности стали существенно отличаются от таковых у промышленных водородопроводов.
Современные протяженные магистральные газопроводы для достижения баланса производительности и металлоемкости имеют высокое рабочее давление (7,4 МПа, 9,8 МПа, 11,8 МПа) и изготавливаются из труб большого диаметра (с номинальным наружным диаметром от 530 мм до 1420 мм) высоких классов прочности, главным образом, К60 и К65 (предел текучести ≥ 485 МПа и ≥ 555 МПа, предел прочности ≥ 590 МПа и ≥ 640 МПа, соответственно). Распределительные газопроводы изготовлены из стали низкой прочности и работают при пониженном давлении. Для подводящих трубопроводов часто применяются трубы из пластика (полиэтилена (ПЭ), поливинилхлорида (ПВХ).
В свою очередь, трубопроводы для транспортировки водорода в промышленных целях (нефтехимическая промышленность), создаются по иной концепции. Для предотвращения эффекта ВО металла труб рабочее давление составляет около 6,9 МПа (1000 psi), трубы имеют небольшой диаметр (как правило, около 300 мм [13]), что обеспечивает низкие окружные напряжения в металле, а материалом труб являются стали низких классов прочности Х42 и Х52 по API 5L, которые имеют низкую твердость и хорошую способность к релаксации напряжений. Водородопроводы эксплуатируются длительное время (с 1940‑х гг.) без каких‑либо существенных инцидентов и аварий, но их производительность (объемы транспортировки) недостаточна для энергетики [8].
При транспортировке водорода в чистом виде или в составе МВС по трубопроводам в целом, и по существующим МГ в особенности, имеется несколько основных технических проблем, которые обусловлены вышеуказанными особенностями водорода.
Трубы большого диаметра для МГ изготавливаются из низколегированных ферритных сталей (например, 10Г2ФБ, Х70), которые склонны к ВО при контакте с транспортируемым водородом при повышенном давлении. В результате ВО происходит снижение сопротивляемости металла развитию трещины и пластичности, увеличивается скорость роста усталостной трещины при циклических нагрузках [11]. Изменение свойств металла происходит с разной интенсивностью в зависимости от типа и особенностей структуры стали, давления перекачиваемой среды и уровня внешних и внутренних напряжений в металле. Склонность трубных сталей к ВО, как правило, увеличивается с повышением их прочности, рабочего давления в трубопроводе, концентрации водорода в МВС. Заметное изменение свойств сталей под воздействием газообразного водорода происходит даже при малых концентрациях водорода в природном газе начиная с 2–5% об. [9, 14]. Металл труб МГ из стали Х70 (класса прочности К60) на рабочее давление 7,4–11,8 МПа считается более склонным к ВО по сравнению со сталью Х42 или Х52 для труб промышленных водородопроводов.
При транспортировке водорода или МВС значительно возрастает нагрузка на компрессоры, поскольку для передачи сопоставимого количества энергии при фиксированном рабочем давлении требуется повышенная степень сжатия транспортируемой среды (в случае чистого водорода – более, чем в три раза) [9, 12]. С увеличением концентрации водорода потребность в мощности компрессора возрастает. Часто ограничивающим фактором для режима центробежного компрессора является скорость ротора турбины. Для стандартных компрессоров скорость не выходит за критические пределы при концентрации водорода 10…20% [9].
Газотурбинный привод компрессора также весьма чувствителен к примеси водорода в газе. Нормальный режим сгорания для стандартных приводов при использовании МВС как топлива возможен в узких пределах изменения числа Воббе: для немодифицированных турбин – 2–5%, для модифицированных – 10% и более [9]. Конвертированные газотурбинные двигатели, предназначенные для использования в качестве топлива МВС и водорода, должны иметь измененные топливные трубопроводы, системы дозирования, регулирования и топливные форсунки [15].
Вследствие высокой летучести водорода вероятны утечки водорода через различные соединения труб и элементов оборудования КС. Проницаемость водорода через сталь мала, поэтому основная часть утечек в стальном трубопроводе будет происходить через фланцевые и резьбовые соединения. В свою очередь, в распределительных и подводящих трубопроводах, изготовленных из пластика (ПЭ, ПВХ), утечка водорода будет происходить непосредственно через стенку трубы из-за достаточно высокой проницаемости пластика для молекулярного водорода (в 4–5 раз больше, чем у метана), но общая потеря водорода с экономической точки зрения считается незначительной [8, 9]. Кроме того, имеются определенные сложности с одорированием водорода и МВС, что может затруднять идентификацию утечек [8].
Риски безопасности, возникающие из-за более широкого диапазона условий воспламенения водорода по сравнению с метаном, возрастают, при этом они больше в случае распределительных сетей из-за повышенной возможности накопления газа при утечке по сравнению с МГ [8, 9].
Технологические риски при трубопроводной транспортировке водорода (опасность быстрого развития усталостных дефектов, изменение режима работы компрессоров и возникновение утечек в соединениях) приводят к необходимости увеличения объема и частоты контроля технического состояния, изменения в сторону усложнения программы управления целостностью системы трубопроводов (IMP – Integrity Management Program). Увеличение затрат на эксплуатацию МГ при его переназначении на транспортировку МВС из-за изменения программы управления целостностью оценивается на уровне 10% [8].
Стандарты на трубопроводы для транспортировки водорода
Требования по использованию трубопроводов для транспортировки водорода и водородсодержащего газа представлены в общих (базовых) стандартах ASME B31.12–2019, а также документах IGC Doc 121/14 и ISO/TR 15916:2015, которые дают указания по проектированию, обеспечению безопасности, выбору материала, эксплуатации и ремонту и т. п. В базовых стандартах даются указания по принципам и методам оценки склонности металла труб к ВО с использованием специальных методов испытаний (рис. 1).
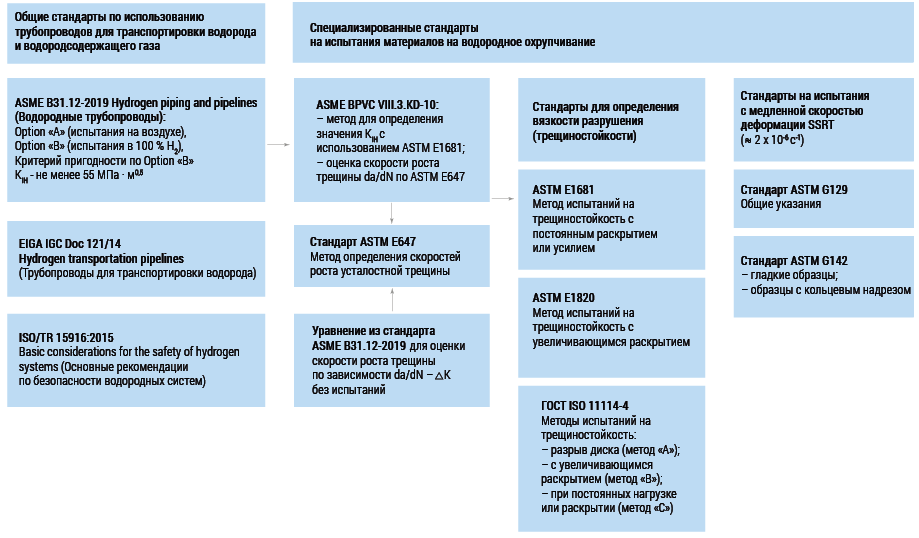
Стандарт ASME B31.12–2019 прямо указывает, что основным требованием для металла является сопротивляемость развитию трещины. Проектирование водородных трубопроводов может проводиться по двум вариантам: с использованием нормативным свойств металла труб (“A”), когда не требуется испытаний в водороде, или с использованием фактических свойств металла труб в водороде при давлении не ниже рабочего (“B”). Критерием пригодности труб для метода “B” является получение для всех зон трубы (основного металла, сварного шва и зоны термического влияния (ЗТВ) порогового коэффициента интенсивности напряжений для водородного растрескивания KIH не менее 55 МПа·м0,5. Стандартом допускается использование труб категории прочности Х70. В свою очередь, документы IGC Doc 121/14 и ISO/TR 15916:2015 основываются на производственных практиках и ограничивают прочность металла труб категорией прочности Х52, дают общие указания по оценке сопротивляемости металла ВО.
Условия испытаний влияют на допустимое рабочее давление, которое в пределах до 20 МПа определяется по формуле из стандарта ASME B31.12–2019. При использовании подхода “B” благодаря более высоким коэффициентам, отражающим параметры и условия работы трубопровода, работоспособности материала (Hf) рабочее давление оказывается существенно выше (в ≈ 1,5–2 раза), чем при по варианту “A”, но для этого посредством испытаний в водороде должна быть получена необходимая сопротивляемость развитию трещины. Основное значение при этом имеет коэффициент работоспособности материала Hf, поскольку он значительно понижается с увеличением прочности металла (по специфицированным значениям) и проектного давления в трубопроводе. Пример расчета рабочего давления по этой методике представлен в таблице 1 для разных труб: категории прочности Х42 (Ø300 х 8 мм) как характерного типа трубы для водородопроводов, класса прочности К52 (Ø530 х 12 мм) на давление 5,4 МПа для региональных МГ, класса прочности К60 (Ø1420 х 1420 мм) для протяженных МГ на рабочее давление до 9,8 МПа.
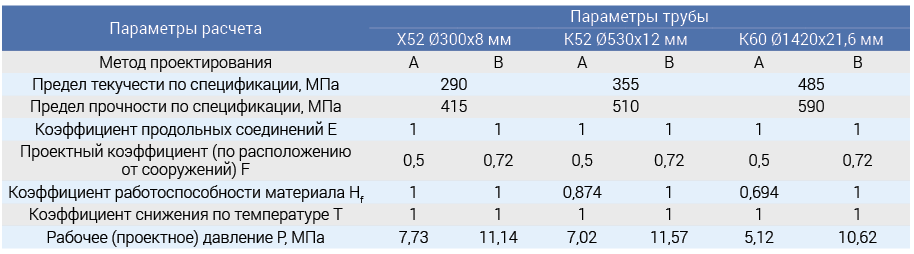
при использовании методов проектирования “A” и “B” по ASME B31.12–2019
Деградация свойств металла под воздействием водорода
Применительно к транспортировке и хранению водорода важно, что в молекулярной форме он не может проникать в металлы, но в атомарном виде водород при определенных условиях может внедряться, перемещаться и накапливаться в металлах. Диффузионная подвижность атомарного водорода значительно выше в ферритных сталях с кристаллической решеткой ОЦК (объемно-центрированная), по сравнению с аустенитными сталями с ГЦК решеткой (гранецентрированная), но растворимость водорода, наоборот, существенно выше в случае аустенитных сталей. Наводороживание стали из газовой фазы становится возможным при наличии концентраторов напряжений и несовершенств (микродефектов) на поверхности металла, повышенного уровня внутренних и внешних напряжений в металле труб. Суть взаимодействия водорода с внутренним строением стали состоит в накоплении водорода в междоузлиях кристаллической решетки и в ловушках водорода, которыми выступают элементы микроструктуры (границы зерен, дислокации, частицы карбидов и т. п.), перемещении водорода (посредством диффузии и взаимодействия с дислокационной структурой стали) и его концентрации в зонах повышенной интенсивности напряжений у кончика растущей трещины, облегчении развития трещины. Охрупчивание низколегированных трубных сталей описывается несколькими механизмами, часто действующим совместно: из-за снижения межатомных связей и облегчения декогезии атомарных слоев (“HEDE”), повышения подвижности дислокаций в микрообъемах (“HELP”), увеличения концентрации водородно-стимулированных вакансий (“HESIV”) [11]. Также для описания эффекта ВО известны и другие механизмы. Транспортируемый по трубам водородсодержащий газ или водород является осушенным, поэтому при взаимодействии водорода с металлом коррозионные и электрохимические процессы не происходят.
В результате ВО снижаются, главным образом, показатели пластичности и трещиностойкости, в меньшей мере и прочностные свойства металла, а скорость роста трещины возрастает на порядок [9, 10, 11]. Механические свойства металла труб МГ классов прочности от К50 до К80 (Х52 – Х100) в результате насыщения водородом из газовой фазы при давлении до 10–12 МПа по результатам анализа современных источников [14] изменяются следующим образом: показатели пластичности (относительные сужение ψ и удлинение δ) и сопротивляемости развитию трещины (KIH) снижаются на величину до 50%, скорость роста трещины (da/dN) увеличивается в 10–30 раз, а прочностные свойства (предел текучести σт, предел прочности σв) изменяются мало.
Испытания для оценки эффекта ВО проводятся со статическим или медленным нагружением для диффузионного перераспределения водорода к местам концентрации напряжений, которые могут стать очагом разрушения. Наилучшим вариантом испытаний является совмещение процессов газофазного наводороживания и медленного нагружения.
Трещиностойкость (вязкость разрушения) металла труб по указаниям «базового» водородного стандарта ASME B31.12–2019 для метода “B” определяется по значению KIH посредством испытаний по методу с постоянным раскрытием (с использованием образцов с нагружением болтом) или по методу с постоянной нагрузкой. Эти способы испытаний основаны на определении способности материала тормозить трещину, в отличие от подобных испытаний по механике разрушения, когда определяется сопротивляемость развитию трещины. Значение KIH получают исходя из создаваемой в образце концентрации напряжений KIApp. Обычно при квалификационных испытаниях величина KIH не является предельно достижимой для сочетания материала и среды, либо для этого требуется весьма большой объем испытаний. Для пластичных материалов, к которым относятся углеродистые трубные стали, значительная пластическая деформация в очаге разрушения приводит к более высокому сопротивлению разрушению по сравнению с испытаниями по механике разрушения. В свою очередь, метод с увеличивающимся раскрытием на основе механики разрушения (ASTM E1820, ГОСТ ISO 11114-4-2017 метод B) позволяет получать значение KIH, которое можно корректно сравнивать со значением KIC для нейтральной среды, но этот метод не указан в «базовом» водородном стандарте.
Показатели прочности и пластичности стали в водороде определяются при испытаниях на растяжение с медленной скоростью деформирования (≈ 2 · 10–6 с‑1) по методу SSRT (Slow Strain Rate Test) в среде водорода или МВС в соответствии со стандартами ASTM G129 и ASTM G142. Суть метода состоит в определении изменения показателей пластичности и прочности материала под воздействием водорода при медленной деформации относительно базовых свойств материала в нейтральной среде. Влияние водорода на металл обычно оценивается по коэффициентам изменения свойств, которые представляют собой отношение значения в водородсодержащей среде к значению в нейтральной среде (азот). Низкое значение коэффициента показывает большое снижение свойства, и металл является склонным к ВО. Однако, несмотря на большое количество работ с испытаниями металла труб по методу SSRT, а также указания стандартов IGC Doc 121/14 и ISO/TR 15916:2015 об использовании метода SSRT для оценки склонности металла труб к ВО, утвержденного критерия для определения хорошей сопротивляемости металла ВО при этих испытаниях к настоящему времени нет. В качестве критерия приемлемого снижения свойств может рассматриваться их сохранение на уровне 80% от исходных.
Скорость роста усталостной трещины da/dN определяют при испытаниях по стандарту ASTM E 647, но для низкоуглеродистых трубных сталей и давления не более 20 МПа оценка da/dN может быть получена вместо испытаний по модели из ASME B31.12–2019, которая разработана на основе комплексных исследований [16].
Структурное состояние стали существенным образом влияет на интенсивность ВО металла труб и оборудования. В зависимости от количества в структуре стали ловушек водорода и их типа (обратимые, необратимые, промежуточные) различается концентрация водорода у кончика растущей трещины. При этом разрушение стали значительно облегчается при наличии в ее структуре твердых и хрупких структурных составляющих (мартенсит, бейнит), в том числе на границах раздела фаз (прослойки цементита).
Результаты многочисленных исследований склонности трубных сталей к ВО свидетельствуют о том, что металл труб одного класса прочности может иметь различное изменение свойств в зависимости от типа и особенностей структуры. Структура трубной стали определяется ее химическим составом и технологией прокатки. У конструкционных сталей структура формируются в результате термической обработки.
Влияние водорода на механические свойства метала труб класса прочности К60 с номинальным наружным диаметром 1420 мм оценено для двух вариантов труб, которые различались по химическому составу стали и микроструктуре. Труба «А» изготовлена в 1980‑х гг. из стали с полосчатой ферритно-перлитной структурой, а для современной трубы «Б» использована сталь с дисперсной ферритно-бейнитной структурой.
При испытаниях на растяжение по методу SSRT (с использованием цилиндрических образцов с надрезом) получено (рис. 2), что с повышением концентрации водорода в МВС прочность ОМ труб практически не меняется (снижение не превышает 5–10%), а показатели пластичности ОМ труб (относительное сужение ψ, перемещение захвата машины в зоне сосредоточенной деформации Ас) имеют тенденцию к снижению, и это происходит по-разному для металла труб «А» и «Б» с разной структурой и составом стали.
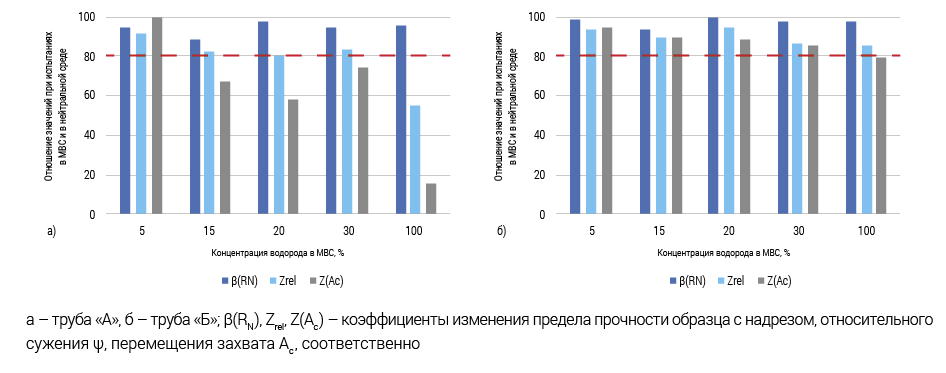
металла труб класса прочности К60 в водородсодержащей среде
При концентрации водорода в МВС на уровне 5% пластичность металла снижается мало (коэффициенты Zrel и ZАс ≈ 92–95%), но с увеличением концентрации водорода пластические свойства ОМ трубы «А» уменьшаются значительно (в 100% ГВ – Zrel ≈ 55%, ZАс ≈ 20%), а в случае трубы «Б» их снижение существенно меньше (Zrel ≈ 85% и ZАс ≈ 90%). Для металла сварного шва (надрез на образцах – по центру шва) закономерности аналогичны таковым для ОМ труб, но пластичность снижается меньше, при этом исходный уровень пластических свойств у металла шва существенно ниже, чем у ОМ трубы.
Результаты испытаний на трещиностойкость (с использованием образцов с нагружением болтом) показывают (таблица 2), что в МВС с концентрацией водорода 30% при давлении 10 МПа металл обеих труб может иметь подрастание трещины не более порогового значения 0,25 мм и требуемую величину KIH ≥ 55 МПа·м0,5. В среде чистого 100% водорода выявлена малая сопротивляемость развитию трещины для металла продольного сварного шва трубы «А». В ходе испытаний при одинаковом уровне нагружения в серии образцов отмечена нестабильность значений подрастания трещины.
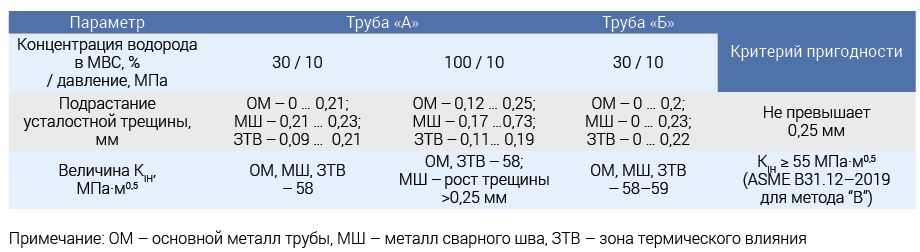
в водородсодержащей среде (при KIApp ≈ 120 МПа·м0,5)
По результатам испытаний на сопротивляемость ВО металла труб класса прочности К60 можно заключить, что в водородсодержащей среде при давлении 10 МПа с повышением концентрации водорода от 5% до 100% имеется тенденция к снижению пластичности и сопротивляемости развитию усталостной трещины, и этот эффект проявляется с разной интенсивностью в зависимости от структуры металла.
Заключение
В рамках развития водородной энергетики рассматриваются способы использования ГТС, имеющей большую протяженность и производительность, для трубопроводной транспортировки водорода в больших объемах: переназначение МГ или подмешивания водорода в транспортируемый газ. Однако технические параметры МГ для природного газа, такие как рабочее давление, диаметр трубы и класс прочности стали существенно отличаются от таковых у промышленных водородопроводов. Металл труб МГ имеет повышенную прочность и твердость, при высоком давлении он подвергается значительно более высоким окружным напряжениям, что способствует ВО стали и деградации ее свойств.
При воздействии газообразного водорода на металл труб высоких классов прочности (К60, Х70, или близких) и технологического оборудования вследствие ВО прогнозируется деградация свойств сталей (главным образом – снижение сопротивляемости развитию трещины и пластичности). Эффект проявляется даже при малом парциальном давлении водорода (несколько %) и значительно усиливается с ростом давления и концентрации. На примере стандартных труб класса прочности К60 диаметром 1420 мм показано, что охрупчивание происходит с разной интенсивностью в зависимости от структуры металла. В результате снижается надежность и долговечность газотранспортной системы.
Предписанный (в «базовом» стандарте ASME B31.12–2019) способ оценки трещиностойкости (по методу с постоянным раскрытием) нацелен на квалификацию продукции, отличается от подходов механики разрушения и не вполне подходит для трубных сталей с высокой пластичностью. Испытания на медленное растяжение SSRT позволяют ранжировать металл по склонности к ВО при большой разнице в определяемых значениях, но не имеют однозначного критерия для оценки сопротивляемости металла ВО.
При транспортировке водорода изменяются режимы работы компрессоров и их приводов. Степень сжатия водородсодержащего газа должна быть повышена из-за низкой объемной плотности энергии водорода, поэтому необходима замена или глубокая модернизация компрессоров. Для работы газотурбинных приводов компрессоров на оптимальных режимах требуется модернизация системы питания из-за отличий водорода как топлива по энергетическим характеристикам от природного газа. Повышенная вероятность утечек водорода через стыковые соединения влияет на безопасность.
Помимо технических также имеются проблемы логистики и экономики, которые вызваны: слабым развитием рынка потребления водорода вне сектора его промышленной переработки, неопределенностью выбора варианта трубопроводной транспортировки водорода (специализированные трубопроводы, переназначение МГ, подмешивание водорода в транспортируемый природный газ), сложностью интегрирования таких сетей в существующие ГТС. Результатом этих эффектов может являться низкая загрузка мощностей или их перевод в категорию незадействованных активов.
УДК 332.12, 662.769.2
DOI 10.46920/2409‑5516_2024_2193_56
EDN: DSIXMB
Риски использования газотранспортной системы для водородной энергетики
Risks of using the gas transportation system for hydrogen energy
Аннотация. В статье рассматриваются проблемы и риски использования существующей газотранспортной системы для транспортировки газообразного водорода. Приведены основные варианты логистики трубопроводной транспортировки водорода в больших объемах, включая переназначение магистральных газопроводов для водорода и подмешивание водорода в транспортируемый газ. Показаны различия в параметрах существующих промышленных водородопроводов и магистральных газопроводов. При трубопроводной транспортировке водорода имеются технические проблемы: водородное охрупчивание металла труб и оборудования, необходимость увеличения степени сжатия среды, повышенная вероятность утечек. Дан обзор стандартов на трубопроводы для транспортировки водорода, методов испытаний для оценки пригодности сталей водородной эксплуатации. Представлен пример деградации свойств металла труб класса прочности К60 с разным типом структуры стали под воздействием водорода и метановодородной смеси при высоком давлении.
Ключевые слова: водород, газотранспортная система, метановодородная смесь, водородное охрупчивание, трубная сталь, рабочее давление трубопровода.
Abstract. The problems and risks of using the existing gas transmission system for transporting hydrogen gas are considered. The main logistics options for pipeline transportation of hydrogen in large volumes are considered, including repurposing main gas pipelines for hydrogen and mixing hydrogen into the transported gas. The differences in the parameters of existing industrial hydrogen pipelines and main natural gas pipelines are shown. When transporting hydrogen through pipelines, there are technical problems: hydrogen embrittlement of the metal of pipes and equipment, the need to increase the degree of compression of the medium, and an increased likelihood of leaks. A review of standards for pipelines for hydrogen transportation and test methods for assessing the suitability of steels for hydrogen operation is given. An example of metal properties degradation of strength class K60 pipes with different types of steel structure under the influence of hydrogen and a methane-hydrogen mixture at high pressure is presented.
Keywords: hydrogen, gas transportation system, methane-hydrogen mixture, hydrogen embrittlement, pipe steel, pipeline operating pressure.